公司规模
SME
地区
- America
国家
- Canada
产品
- BatchMaster ERP
技术栈
- Microsoft Office
- Microsoft Excel
- Microsoft Access
实施规模
- Enterprise-wide Deployment
影响指标
- Productivity Improvements
- Cost Savings
技术
- 功能应用 - 企业资源规划系统 (ERP)
适用行业
- 消费品
- 药品
适用功能
- 离散制造
用例
- 库存管理
- 自动化制造系统
服务
- 系统集成
- 培训
关于客户
Cosmaceutical Research Lab, Inc., located in Surrey, British Columbia, is a contract manufacturer of liquids, lotions, and creams for the cosmetic and pharmaceutical industry. The company's chemists have over 20 years of experience in the industry, including product formulation, reverse formulations, and research and development. The company, which started with four employees in a 1200 sq. ft. facility, has recently moved into a new 50,000 sq. ft. building housing its 41 employees. Cosmaceutical serves two industries, personal care products and OTC pharmaceutical products. As an end-to-end contract manufacturer, the company goes from research and concept development through to final packaging.
挑战
Cosmaceutical, a contract manufacturer of liquids, lotions, and creams for the cosmetic and pharmaceutical industry, was facing challenges with its existing non-integrated systems. The company was using a series of Microsoft Office tools including Excel spreadsheets and custom applications written in Access. As the company grew, these systems became a limiting factor. Duplicate data entry and accuracy were becoming a problem. The systems covered all aspects of the business, but they didn't communicate with each other, leading to islands of information. One department didn't know what another department was doing. The company needed an integrated system so that anyone in the company could see what was happening with a product at any given time.
解决方案
In 2005, Cosmaceutical commenced its search for a new integrated system. After considering five software products, the company shortlisted three and finally chose BatchMaster ERP. The company started its implementation in January 2006, and appointed Ruth Ghuman, controller, as the project champion. They took the train-the-trainer approach, where BatchMaster trained Ruth on the software, and she then created training programs for all of their users. The company was ready to go live in September 2006, but as that was their busiest time of the year, they decided to wait until January 2007. Today, Cosmaceutical relies on BatchMaster to run its business. BatchMaster is used in every department throughout the company.
运营影响
数量效益
Case Study missing?
Start adding your own!
Register with your work email and create a new case study profile for your business.
相关案例.
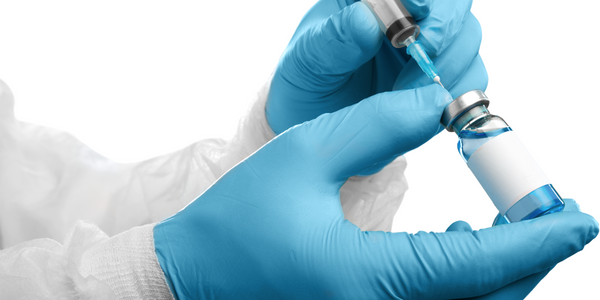
Case Study
Case Study: Pfizer
Pfizer’s high-performance computing software and systems for worldwide research and development support large-scale data analysis, research projects, clinical analytics, and modeling. Pfizer’s computing services are used across the spectrum of research and development efforts, from the deep biological understanding of disease to the design of safe, efficacious therapeutic agents.
.png)
Case Study
Improving Vending Machine Profitability with the Internet of Things (IoT)
The vending industry is undergoing a sea change, taking advantage of new technologies to go beyond just delivering snacks to creating a new retail location. Intelligent vending machines can be found in many public locations as well as company facilities, selling different types of goods and services, including even computer accessories, gold bars, tickets, and office supplies. With increasing sophistication, they may also provide time- and location-based data pertaining to sales, inventory, and customer preferences. But at the end of the day, vending machine operators know greater profitability is driven by higher sales and lower operating costs.
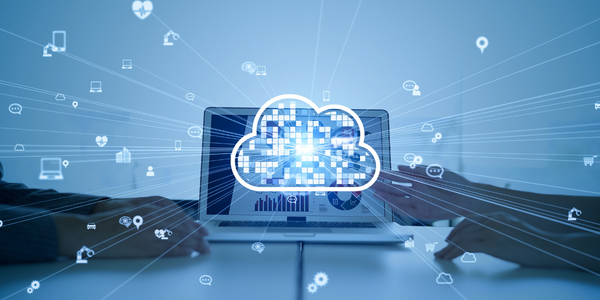
Case Study
Fusion Middleware Integration on Cloud for Pharma Major
Customer wanted a real-time, seamless, cloud based integration between the existing on premise and cloud based application using SOA technology on Oracle Fusion Middleware Platform, a Contingent Worker Solution to collect, track, manage and report information for on-boarding, maintenance and off-boarding of contingent workers using a streamlined and Integrated business process, and streamlining of integration to the back-end systems and multiple SaaS applications.
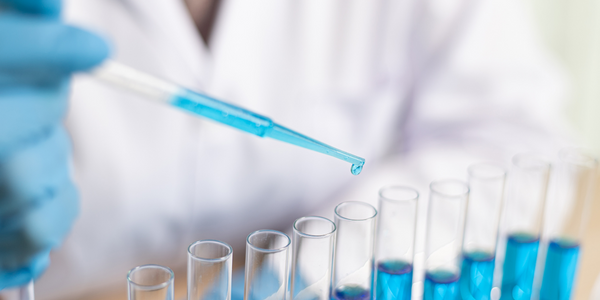
Case Study
Process Control System Support
In many automated production facilities, changes are made to SIMATIC PCS 7 projects on a daily basis, with individual processes often optimised by multiple workers due to shift changes. Documentation is key here, as this keeps workers informed about why a change was made. Furthermore, SIMATIC PCS 7 installations are generally used in locations where documentation is required for audits and certification. The ability to track changes between two software projects is not only an invaluable aid during shift changes, but also when searching for errors or optimising a PCS 7 installation. Every change made to the system is labour-intensive and time-consuming. Moreover, there is also the risk that errors may occur. If a change is saved in the project, then the old version is lost unless a backup copy was created in advance. If no backup was created, it will no longer be possible to return to the previous state if and when programming errors occur. Each backup denotes a version used by the SIMATIC PCS 7 system to operate an installation. To correctly interpret a version, information is required on WHO changed WHAT, WHERE, WHEN and WHY: - Who created the version/who is responsible for the version? - Who released the version? - What was changed in the version i.e. in which block or module of the SIMATIC PCS 7 installation were the changes made? - When was the version created? Is this the latest version or is there a more recent version? - Why were the changes made to the version? If they are part of a regular maintenance cycle, then is the aim to fix an error or to improve production processes? - Is this particular version also the version currently being used in production? The fact that SIMATIC PCS 7 projects use extremely large quantities of data complicates the situation even further, and it can take a long time to load and save information as a result. Without a sustainable strategy for operating a SIMATIC PCS 7 installation, searching for the right software version can become extremely time-consuming and the installation may run inefficiently as a result.
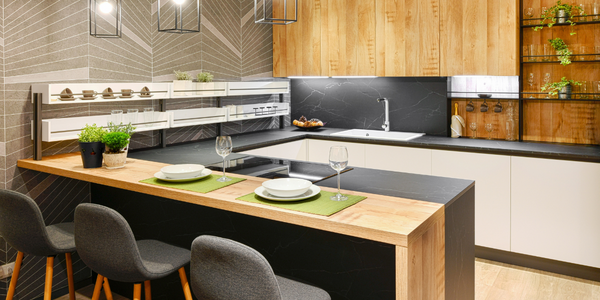
Case Study
Series Production with Lot-size-1 Flexibility
Nobilia manufactures customized fitted kitchens with a lot size of 1. They require maximum transparency of tracking design data and individual processing steps so that they can locate a particular piece of kitchen furniture in the sequence of processes.