Ballard Streamlines Manufacturing Process in the Cloud
公司规模
Large Corporate
地区
- America
国家
- United States
产品
- Oracle SCM Cloud
- RF-SMART
技术栈
- Cloud Computing
- Barcode Scanning
实施规模
- Enterprise-wide Deployment
影响指标
- Productivity Improvements
- Customer Satisfaction
- Digital Expertise
技术
- 功能应用 - 制造执行系统 (MES)
- 功能应用 - 库存管理系统
- 平台即服务 (PaaS) - 数据管理平台
适用功能
- 仓库和库存管理
用例
- 库存管理
- 自动化制造系统
- 仓库自动化
服务
- 系统集成
- 培训
关于客户
Ballard Power Systems is an alternative energy product developer and world-class manufacturer with over 30 years of experience in the field. As the world leader in proton exchange membrane fuel cell technology, they are committed to providing clean energy solutions. Ballard has a strong focus on innovation and sustainability, aiming to deliver high-quality products that contribute to a greener future. With a large-scale operation, Ballard needed to modernize their technology systems to improve visibility and efficiency across their manufacturing processes.
挑战
Ballard Power Systems, a leader in proton exchange membrane fuel cell technology, needed to consolidate and modernize their technology systems. They aimed to move away from stand-alone systems and find a centralized ERP that would provide better visibility into all areas of their operation. This corporate initiative led to the selection of Oracle SCM Cloud. However, Ballard also wanted to use barcoding and scanning to direct the flow of material through their shop floor. They needed an easy way to get shop floor information into Oracle SCM Cloud while leveraging its robust functionality and maintaining the simplicity of barcode scanning.
解决方案
Ballard chose Oracle SCM Cloud as the central repository to manage their business operations. To complement this, they selected RF-SMART as their mobile inventory and manufacturing execution solution based on the recommendation of their implementation partner. RF-SMART enabled Ballard to use barcoding and scanning to direct the flow of material through their shop floor. This integration allowed workers to follow prompts on handheld devices, simplifying transactions and eliminating the need for specific system knowledge. The mobile capabilities of RF-SMART allowed employees to walk and scan items throughout the warehouse, making transactions more efficient and real-time. Additionally, RF-SMART facilitated the printing of labels on demand, further streamlining the manufacturing process.
运营影响
Case Study missing?
Start adding your own!
Register with your work email and create a new case study profile for your business.
相关案例.

Case Study
Plastic Spoons Case study: Injection Moulding
In order to meet customer expectations by supplying a wide variety of packaging units, from 36 to 1000 spoons per package, a new production and packaging line needed to be built. DeSter wanted to achieve higher production capacity, lower cycle time and a high degree of operator friendliness with this new production line.
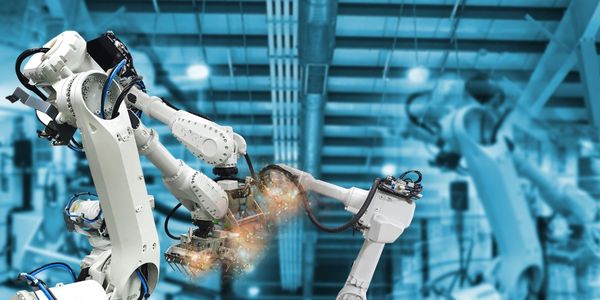
Case Study
Robot Saves Money and Time for US Custom Molding Company
Injection Technology (Itech) is a custom molder for a variety of clients that require precision plastic parts for such products as electric meter covers, dental appliance cases and spools. With 95 employees operating 23 molding machines in a 30,000 square foot plant, Itech wanted to reduce man hours and increase efficiency.
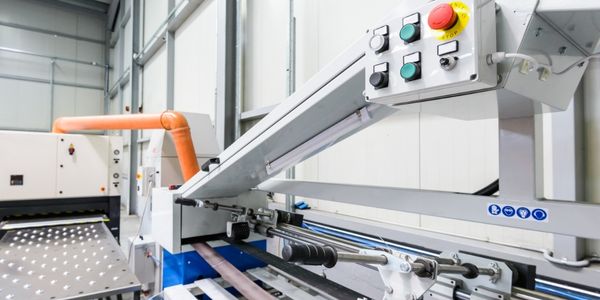
Case Study
Fully Automated Visual Inspection System
Tofflon has developed a fully automatic machine that uses light to inspect vials, medicine bottles, or infusion containers for glass fragments, aluminum particles, rubber grains, hairs, fibers, or other contaminants. It also detects damaged containers with cracks or inclusions (microscopic imperfections), automatically removing faulty or contaminated products. In order to cover all production processes for freeze-dried pharmaceuticals, Tofflon needed to create an open, consistent, and module-based automation concept.
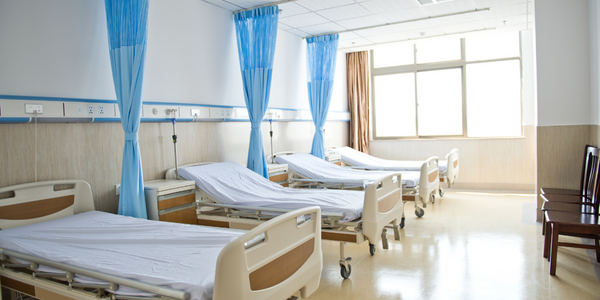
Case Study
Hospital Inventory Management
The hospital supply chain team is responsible for ensuring that the right medical supplies are readily available to clinicians when and where needed, and to do so in the most efficient manner possible. However, many of the systems and processes in use at the cancer center for supply chain management were not best suited to support these goals. Barcoding technology, a commonly used method for inventory management of medical supplies, is labor intensive, time consuming, does not provide real-time visibility into inventory levels and can be prone to error. Consequently, the lack of accurate and real-time visibility into inventory levels across multiple supply rooms in multiple hospital facilities creates additional inefficiency in the system causing over-ordering, hoarding, and wasted supplies. Other sources of waste and cost were also identified as candidates for improvement. Existing systems and processes did not provide adequate security for high-cost inventory within the hospital, which was another driver of cost. A lack of visibility into expiration dates for supplies resulted in supplies being wasted due to past expiry dates. Storage of supplies was also a key consideration given the location of the cancer center’s facilities in a dense urban setting, where space is always at a premium. In order to address the challenges outlined above, the hospital sought a solution that would provide real-time inventory information with high levels of accuracy, reduce the level of manual effort required and enable data driven decision making to ensure that the right supplies were readily available to clinicians in the right location at the right time.
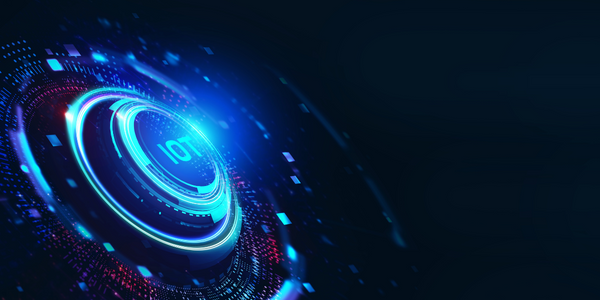
Case Study
IoT Solution for Cold Chain
Most of the customer's warehouses run on utility and generator power. Since these warehouses are in remote locations, power outages are a very common scenario. Diesel fuel, thereby, becomes a significant cost for these warehouses. Energy consumption was also very high due to the lack of a consistent temperature throughout the facility. This lack of a consistent temperature in all areas and no way to control it, resulted in the customer losing a significant amount of their temperature sensitive goods due to spoilage.