BÖWE BELL + HOWELL: Accelerating Automated Mail-Sorting System Design with SOLIDWORKS Office Premium
公司规模
Large Corporate
地区
- America
国家
- United States
产品
- SOLIDWORKS Professional
- SOLIDWORKS Premium
- SOLIDWORKS Workgroup PDM
- SOLIDWORKS Simulation
- SOLIDWORKS Enterprise PDM
技术栈
- 3D CAD
- Sheet Metal Design
- Cable Routing
- Integrated Analysis
实施规模
- Enterprise-wide Deployment
影响指标
- Productivity Improvements
- Customer Satisfaction
- Cost Savings
技术
- 功能应用 - 产品生命周期管理系统 (PLM)
- 分析与建模 - 预测分析
- 功能应用 - 计算机化维护管理系统 (CMMS)
适用行业
- 设备与机械
适用功能
- 产品研发
- 质量保证
用例
- 预测性维护
- 机器状态监测
- 远程资产管理
服务
- 软件设计与工程服务
- 系统集成
关于客户
Böwe Bell + Howell is one of the largest manufacturers of automated mail-processing systems globally. Their equipment, which can measure up to 14 feet wide by 285 feet long, is capable of processing up to 50,000 pieces of mail per hour. The company serves mailrooms of various sizes, helping them route documents efficiently. With a focus on innovation and efficiency, Böwe Bell + Howell transitioned from using AutoCAD® 2D design tools to a 3D CAD system in 2004 to enhance their design productivity and accelerate the development of large assemblies. Despite initial challenges with Autodesk Inventor® 3D software, the company ultimately found success with SOLIDWORKS® 3D CAD software.
挑战
Böwe Bell + Howell, a leading manufacturer of automated mail-processing systems, faced significant challenges with their existing 2D design tools and later with Autodesk Inventor® 3D software. The company needed to increase design productivity and accelerate large-assembly development. However, they encountered stability issues with Inventor, including the loss of drawings and data, which hindered their progress. Additionally, their former system struggled with handling sheet metal, weldments, and fasteners, which are critical components in their products. These challenges prompted Böwe Bell + Howell to reevaluate their 3D CAD solution in mid-2005.
解决方案
In mid-2005, Böwe Bell + Howell decided to transition to the SOLIDWORKS® 3D CAD software environment. They implemented eight seats of SOLIDWORKS Professional and four seats of SOLIDWORKS Premium due to its ease of use and capabilities in handling large assemblies, sheet metal, and cable routing. The company also integrated SOLIDWORKS Workgroup PDM software for managing workgroup drawings and SOLIDWORKS Simulation for evaluating design strength and performance. This transition allowed Böwe Bell + Howell to work in both 2D and 3D environments, meeting their customers' design needs more effectively. The use of 3D models also streamlined the creation of assembly and maintenance documentation, significantly reducing time-to-production. The robust capabilities of SOLIDWORKS software, including automated tools for sheet metal, weldment, and cable routing, enabled Böwe Bell + Howell engineers to develop new processing systems four times faster than with their previous CAD solution. The design configuration capabilities in SOLIDWORKS software allowed for quick customization of standard product designs to meet specific customer requirements, further enhancing efficiency and performance.
运营影响
数量效益
Case Study missing?
Start adding your own!
Register with your work email and create a new case study profile for your business.
相关案例.

Case Study
Smart Water Filtration Systems
Before working with Ayla Networks, Ozner was already using cloud connectivity to identify and solve water-filtration system malfunctions as well as to monitor filter cartridges for replacements.But, in June 2015, Ozner executives talked with Ayla about how the company might further improve its water systems with IoT technology. They liked what they heard from Ayla, but the executives needed to be sure that Ayla’s Agile IoT Platform provided the security and reliability Ozner required.

Case Study
IoT enabled Fleet Management with MindSphere
In view of growing competition, Gämmerler had a strong need to remain competitive via process optimization, reliability and gentle handling of printed products, even at highest press speeds. In addition, a digitalization initiative also included developing a key differentiation via data-driven services offers.
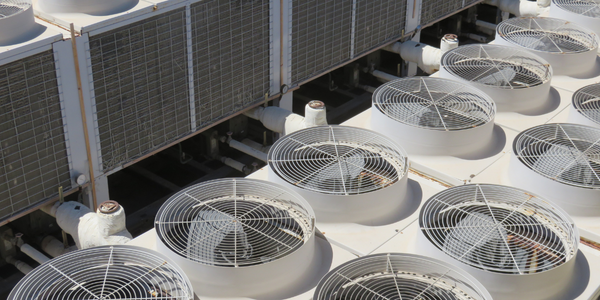
Case Study
Predictive Maintenance for Industrial Chillers
For global leaders in the industrial chiller manufacturing, reliability of the entire production process is of the utmost importance. Chillers are refrigeration systems that produce ice water to provide cooling for a process or industrial application. One of those leaders sought a way to respond to asset performance issues, even before they occur. The intelligence to guarantee maximum reliability of cooling devices is embedded (pre-alarming). A pre-alarming phase means that the cooling device still works, but symptoms may appear, telling manufacturers that a failure is likely to occur in the near future. Chillers who are not internet connected at that moment, provide little insight in this pre-alarming phase.

Case Study
Premium Appliance Producer Innovates with Internet of Everything
Sub-Zero faced the largest product launch in the company’s history:It wanted to launch 60 new products as scheduled while simultaneously opening a new “greenfield” production facility, yet still adhering to stringent quality requirements and manage issues from new supply-chain partners. A the same time, it wanted to increase staff productivity time and collaboration while reducing travel and costs.

Case Study
Integration of PLC with IoT for Bosch Rexroth
The application arises from the need to monitor and anticipate the problems of one or more machines managed by a PLC. These problems, often resulting from the accumulation over time of small discrepancies, require, when they occur, ex post technical operations maintenance.
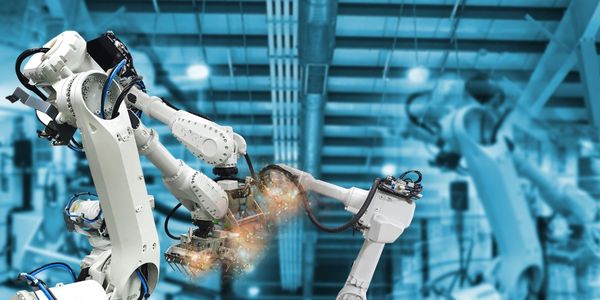
Case Study
Robot Saves Money and Time for US Custom Molding Company
Injection Technology (Itech) is a custom molder for a variety of clients that require precision plastic parts for such products as electric meter covers, dental appliance cases and spools. With 95 employees operating 23 molding machines in a 30,000 square foot plant, Itech wanted to reduce man hours and increase efficiency.