3PL Triplefin moves to Manhattan SCALE™
公司规模
200-1,000
地区
- America
国家
- United States
产品
- Manhattan SCALE™
技术栈
- Warehouse Management System (WMS)
- Supply Chain Management (SCM)
实施规模
- Enterprise-wide Deployment
影响指标
- Cost Savings
- Customer Satisfaction
- Productivity Improvements
技术
- 功能应用 - 企业资源规划系统 (ERP)
- 功能应用 - 仓库管理系统 (WMS)
适用行业
- 消费品
- 药品
适用功能
- 物流运输
- 仓库和库存管理
用例
- 库存管理
- 供应链可见性(SCV)
- 仓库自动化
服务
- 软件设计与工程服务
- 系统集成
关于客户
Triplefin, founded in 1981 and headquartered in Cincinnati, Ohio, is a premier provider of outsourced order-to-cash business process solutions to leading companies in the pharmaceutical and consumer products industries. With approximately 165 employees and $130 million in annual revenues, the company supports some of the most successful brands in the world with diversified offerings. Triplefin is ISO certified and operates two facilities in Cincinnati with 230,000 square feet of distribution space. The company has built its business by offering superior levels of customer care and service, helping its clients maximize the value of their customer relationships.
挑战
As Triplefin's client roster increased to nearly 40 companies, the technology platform it was using became unreliable. Developed internally and enhanced several times, this warehouse and distribution system was very difficult to maintain. The system began to shut down once or twice a week, requiring an increase in maintenance staff. These shutdowns created a huge increase in labor expenses, as the workforce became idle while the system was being repaired and then had to work overtime to keep up with the distribution and shipping workload. This situation put a strain on the company's staff and its bottom line.
解决方案
Triplefin decided to implement Manhattan SCALE to stabilize processes and manage the varying requirements of its 38 different clients. Manhattan Associates was chosen for its reliable, flexible solutions that are well-respected in the industry. Manhattan helped Triplefin configure a process to migrate 38 clients as quickly as possible, on budget, and without any service disruptions. The company began by moving two clients per month, with DC floor personnel using two inventory guns to simultaneously accommodate SCALE and the old system. As employees became more proficient with SCALE, the company began to cut-over more clients per month, eventually moving six clients to SCALE during the last month of deployment.
运营影响
数量效益
Case Study missing?
Start adding your own!
Register with your work email and create a new case study profile for your business.
相关案例.
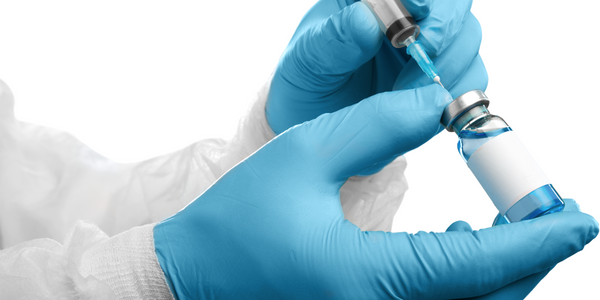
Case Study
Case Study: Pfizer
Pfizer’s high-performance computing software and systems for worldwide research and development support large-scale data analysis, research projects, clinical analytics, and modeling. Pfizer’s computing services are used across the spectrum of research and development efforts, from the deep biological understanding of disease to the design of safe, efficacious therapeutic agents.
.png)
Case Study
Improving Vending Machine Profitability with the Internet of Things (IoT)
The vending industry is undergoing a sea change, taking advantage of new technologies to go beyond just delivering snacks to creating a new retail location. Intelligent vending machines can be found in many public locations as well as company facilities, selling different types of goods and services, including even computer accessories, gold bars, tickets, and office supplies. With increasing sophistication, they may also provide time- and location-based data pertaining to sales, inventory, and customer preferences. But at the end of the day, vending machine operators know greater profitability is driven by higher sales and lower operating costs.
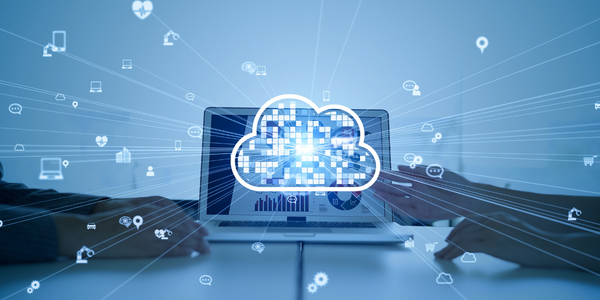
Case Study
Fusion Middleware Integration on Cloud for Pharma Major
Customer wanted a real-time, seamless, cloud based integration between the existing on premise and cloud based application using SOA technology on Oracle Fusion Middleware Platform, a Contingent Worker Solution to collect, track, manage and report information for on-boarding, maintenance and off-boarding of contingent workers using a streamlined and Integrated business process, and streamlining of integration to the back-end systems and multiple SaaS applications.
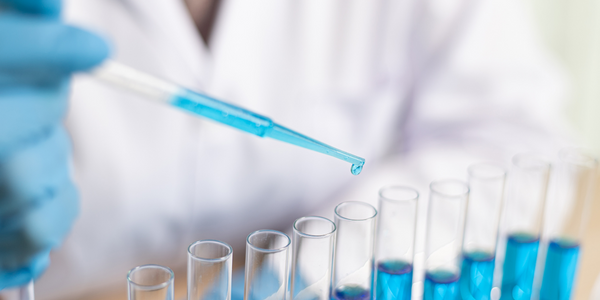
Case Study
Process Control System Support
In many automated production facilities, changes are made to SIMATIC PCS 7 projects on a daily basis, with individual processes often optimised by multiple workers due to shift changes. Documentation is key here, as this keeps workers informed about why a change was made. Furthermore, SIMATIC PCS 7 installations are generally used in locations where documentation is required for audits and certification. The ability to track changes between two software projects is not only an invaluable aid during shift changes, but also when searching for errors or optimising a PCS 7 installation. Every change made to the system is labour-intensive and time-consuming. Moreover, there is also the risk that errors may occur. If a change is saved in the project, then the old version is lost unless a backup copy was created in advance. If no backup was created, it will no longer be possible to return to the previous state if and when programming errors occur. Each backup denotes a version used by the SIMATIC PCS 7 system to operate an installation. To correctly interpret a version, information is required on WHO changed WHAT, WHERE, WHEN and WHY: - Who created the version/who is responsible for the version? - Who released the version? - What was changed in the version i.e. in which block or module of the SIMATIC PCS 7 installation were the changes made? - When was the version created? Is this the latest version or is there a more recent version? - Why were the changes made to the version? If they are part of a regular maintenance cycle, then is the aim to fix an error or to improve production processes? - Is this particular version also the version currently being used in production? The fact that SIMATIC PCS 7 projects use extremely large quantities of data complicates the situation even further, and it can take a long time to load and save information as a result. Without a sustainable strategy for operating a SIMATIC PCS 7 installation, searching for the right software version can become extremely time-consuming and the installation may run inefficiently as a result.
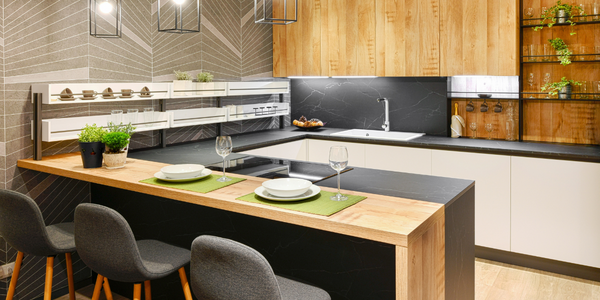
Case Study
Series Production with Lot-size-1 Flexibility
Nobilia manufactures customized fitted kitchens with a lot size of 1. They require maximum transparency of tracking design data and individual processing steps so that they can locate a particular piece of kitchen furniture in the sequence of processes.