Visual Quality Detection

Visual quality detection automates the analysis of products on the production line or equipment in production facilities for quality control using machine vision. Machine vision is the technology and methods used to provide image-based automatic inspection. It is a system that uses visual computing technology to mechanically “see” the activities that take place one by one along the production line. The components of an automatic inspection system usually include lighting, a camera or other image acquiring device, a processor, software, and output devices. Machine vision surpasses human vision at the quantitative and qualitative measurement of a structured scene because of its speed, accuracy, and repeatability. A machine vision system can easily assess object details too small to be seen by the human eye, and inspect them with greater reliability and lesser error. On a production line, machine vision systems can inspect hundreds or thousands of parts per minute reliably and repeatedly, far exceeding the inspection capabilities of humans. It also uses Artificial Intelligence to mimick human level intelligence to distinguish anomalies, parts, and characters, while tolerating natural variations in complex patterns. It merges the adaptability of human visual inspection with the speed and reliability of a computerized system.
- Automotive
- Transportation
- Discrete Manufacturing
- Product Development
- Quality Assurance
The overall machine vision market is expected to grow from USD 8.12 billion in 2015 to USD 14.43 billion by 2022, at a CAGR of 8.15% between 2016 and 2022.
Source: Markets and Markets
Quality Assurance Improvement: Visual quality detection systems enable businesses to enhance their quality assurance processes by identifying defects and anomalies in products or components. By implementing these systems, companies can minimize production errors, reduce scrap and rework costs, and improve overall product quality.
Operational Efficiency: Visual quality detection streamlines production processes by automating the inspection and verification of product quality. This automation reduces the need for manual inspection, accelerates production cycles, and increases throughput, resulting in higher operational efficiency and productivity.
Customer Satisfaction: Consistently delivering products with high visual quality is essential for maintaining customer satisfaction and loyalty. Visual quality detection systems help ensure that products meet or exceed customer expectations regarding appearance, finish, and aesthetic attributes, leading to greater customer satisfaction and brand reputation.
Manufacturing Managers: Manufacturing managers are responsible for implementing visual quality detection systems within production facilities. They oversee the selection, deployment, and integration of inspection technologies, as well as the training of personnel to operate and maintain these systems effectively.
Quality Control Inspectors: Quality control inspectors play a crucial role in visual quality detection processes. They utilize inspection equipment and software to identify defects, deviations, and imperfections in manufactured products, ensuring compliance with quality standards, specifications, and regulatory requirements.
Product Designers: Product designers collaborate with manufacturing teams to establish visual quality standards and criteria for products. They provide input on design specifications, tolerances, and surface finishes to ensure that products meet aesthetic requirements and align with brand identity and customer preferences.
Machine Vision Systems: Visual quality detection relies on machine vision systems to acquire, process, and interpret visual data from images or video streams. These systems employ cameras, lenses, and sensors to capture high-resolution images, which are then analyzed using image processing algorithms to detect defects and anomalies.
Deep Learning and AI: Advanced visual quality detection systems leverage deep learning and artificial intelligence (AI) algorithms to improve defect detection accuracy and reliability. These algorithms can learn from labeled training data to recognize complex patterns and variations in visual characteristics, enhancing the system's ability to detect subtle defects and variations.
Image Analysis Algorithms: Visual quality detection systems rely on image analysis algorithms to process and analyze images of products or components. These algorithms extract features, detect patterns, and identify anomalies indicative of defects or quality issues, generating actionable insights for decision-making.
Defect Classification Data: Visual quality detection systems capture data on detected defects, including their type, location, severity, and frequency. This data allows manufacturers to categorize and classify defects, track their occurrence over time, and implement corrective actions to address root causes and prevent recurrence.
Hardware Implementation: Deployment of visual quality detection systems involves the installation and configuration of hardware components, such as cameras, lighting systems, and image capture devices. These components must be strategically positioned and calibrated to ensure optimal image quality and accuracy during inspections.
Software Integration: Visual quality detection systems require integration with software applications for image processing, analysis, and defect detection. This integration involves configuring software settings, developing inspection algorithms, and interfacing with existing manufacturing systems, such as production control software and enterprise resource planning (ERP) systems.
Case Studies.
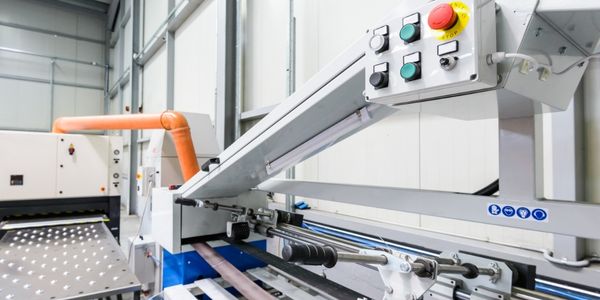

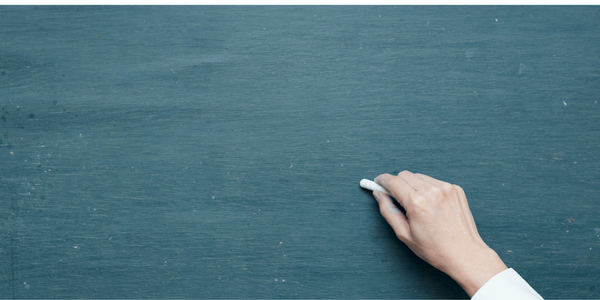