Zanders Finds Efficient Warehouse Solutions through Raymond
Customer Company Size
Large Corporate
Region
- America
Country
- United States
Product
- Raymond ReNewed™ electric lift trucks
- Raymond® lift trucks
- Raymond Swing-Reach® trucks
- Raymond intelliguide™ Digital Wire Guidance System
Tech Stack
- Digital Wire Guidance System
- Electric Lift Trucks
- Integrated Carousel System
Implementation Scale
- Enterprise-wide Deployment
Impact Metrics
- Cost Savings
- Customer Satisfaction
- Productivity Improvements
Technology Category
- Automation & Control - Automation & Process Control Systems
- Functional Applications - Warehouse Management Systems (WMS)
Applicable Industries
- Consumer Goods
- Retail
Applicable Functions
- Logistics & Transportation
- Warehouse & Inventory Management
Use Cases
- Fleet Management
- Inventory Management
- Warehouse Automation
Services
- System Integration
About The Customer
Zanders Sporting Goods, located in Sparta, Ill., is a company that specializes in providing material handling solutions to U.S. firearms dealers. The company is known for its efficient warehouse operations, which are crucial for maintaining positive relationships with its more than 22,023 customers. Zanders offers same-day shipping and rapid special orders, making the efficiency of its material handling solutions a key component of its business model. The company has a strong focus on optimizing its warehouse operations to meet the increasing product demand from its dealers.
The Challenge
In an effort to streamline its material handling operations and better accommodate increased product demand from its dealers, Zanders consolidated a number of its facilities into one location in 2010. It also implemented narrow aisles to increase its storage capacity, so the company needed to re-evaluate its lift truck fleet and how it moved products throughout the warehouse. With goals of shipping orders out faster, reducing product damage and decreasing the number of times products are handled, the company began working with Heubel Material Handling, Inc., an authorized Raymond Sales and Service Center.
The Solution
With the help of Heubel, Zanders was able to save space by implementing an integrated carousel system, a fleet of Raymond ReNewed™ electric lift trucks, and a wire guidance system for lift trucks in its very narrow aisles. Zanders also adopted a maintenance and service plan for its lift trucks and carousel system to increase lift truck uptime and better manage its fleet. As a result of these plans, the company was able to complete dealer orders at a faster rate and reduce product damage, increasing efficiency by 20 percent to 30 percent. Additionally, with the installation of the Raymond intelliguide™ Digital Wire Guidance System, Zanders was able to allow operators to steadily transport products down narrow aisles by electronically engaging a guide wire on the warehouse floor. This addition decreases the possibility of collisions or product damage, and enables operators to focus on handling the load and picking orders instead of steering.
Operational Impact
Quantitative Benefit
Case Study missing?
Start adding your own!
Register with your work email and create a new case study profile for your business.
Related Case Studies.
.png)
Case Study
Improving Vending Machine Profitability with the Internet of Things (IoT)
The vending industry is undergoing a sea change, taking advantage of new technologies to go beyond just delivering snacks to creating a new retail location. Intelligent vending machines can be found in many public locations as well as company facilities, selling different types of goods and services, including even computer accessories, gold bars, tickets, and office supplies. With increasing sophistication, they may also provide time- and location-based data pertaining to sales, inventory, and customer preferences. But at the end of the day, vending machine operators know greater profitability is driven by higher sales and lower operating costs.
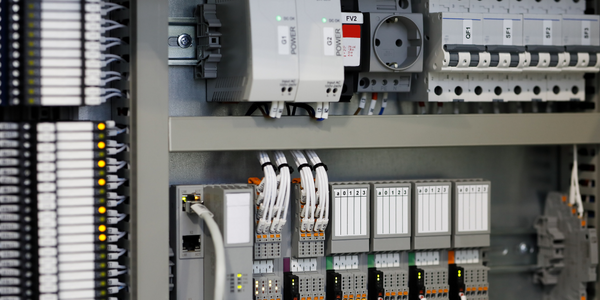
Case Study
Improving Production Line Efficiency with Ethernet Micro RTU Controller
Moxa was asked to provide a connectivity solution for one of the world's leading cosmetics companies. This multinational corporation, with retail presence in 130 countries, 23 global braches, and over 66,000 employees, sought to improve the efficiency of their production process by migrating from manual monitoring to an automatic productivity monitoring system. The production line was being monitored by ABB Real-TPI, a factory information system that offers data collection and analysis to improve plant efficiency. Due to software limitations, the customer needed an OPC server and a corresponding I/O solution to collect data from additional sensor devices for the Real-TPI system. The goal is to enable the factory information system to more thoroughly collect data from every corner of the production line. This will improve its ability to measure Overall Equipment Effectiveness (OEE) and translate into increased production efficiencies. System Requirements • Instant status updates while still consuming minimal bandwidth to relieve strain on limited factory networks • Interoperable with ABB Real-TPI • Small form factor appropriate for deployment where space is scarce • Remote software management and configuration to simplify operations
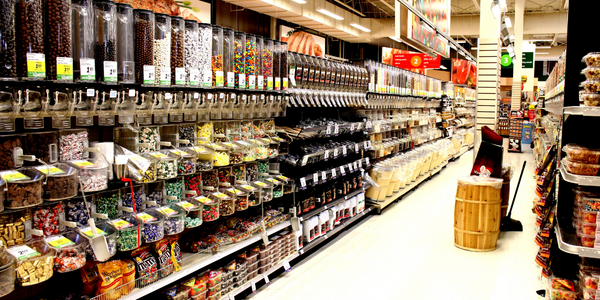
Case Study
How Sirqul’s IoT Platform is Crafting Carrefour’s New In-Store Experiences
Carrefour Taiwan’s goal is to be completely digital by end of 2018. Out-dated manual methods for analysis and assumptions limited Carrefour’s ability to change the customer experience and were void of real-time decision-making capabilities. Rather than relying solely on sales data, assumptions, and disparate systems, Carrefour Taiwan’s CEO led an initiative to find a connected IoT solution that could give the team the ability to make real-time changes and more informed decisions. Prior to implementing, Carrefour struggled to address their conversion rates and did not have the proper insights into the customer decision-making process nor how to make an immediate impact without losing customer confidence.
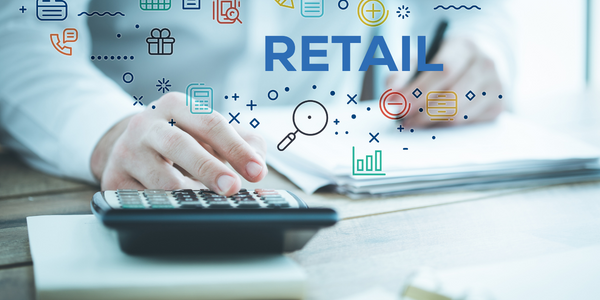
Case Study
Digital Retail Security Solutions
Sennco wanted to help its retail customers increase sales and profits by developing an innovative alarm system as opposed to conventional connected alarms that are permanently tethered to display products. These traditional security systems were cumbersome and intrusive to the customer shopping experience. Additionally, they provided no useful data or analytics.