World Class Training with Digital Work Instructions: A Case Study on a Fortune 500 Food and Beverage Company
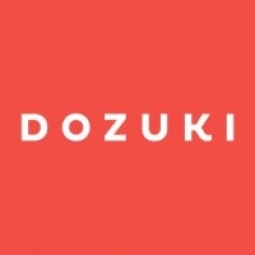
Technology Category
- Functional Applications - Manufacturing Execution Systems (MES)
Applicable Industries
- Education
- Retail
Applicable Functions
- Facility Management
- Maintenance
Use Cases
- Personnel Tracking & Monitoring
- Virtual Training
Services
- Training
About The Customer
The customer in this case study is a Fortune 500 manufacturer of branded consumer foods and pet food products sold through retail stores. Over the past 150 years, they have built a portfolio of more than 100 brands worldwide. Their goal is to manufacture human and pet food products that provide great taste, nutrition, convenience, and value for consumers. To achieve this, they recognized the need for a frontline digital transformation to create a world-class training and upskilling program. They have already deployed Dozuki, a digital work instruction platform, at five of their facilities, with plans for more.
The Challenge
The company was grappling with several challenges, including increasing staff retirements, lack of digitized processes, and absence of a formal training program. These issues were leading to spikes in quality problems and downtime. As new frontline employees joined, there was no program in place to upskill them properly to meet production demands, leading to a repetitive cycle of issues. The company was losing approximately $3 million per year due to poor frontline training. Their facilities historically relied on job shadowing and word of mouth for operator training, which was proving to be inadequate. With high numbers of retiring staff and outdated documentation held in paper binders, standardizing process information was a pressing need. Changeover errors in their sensitive assembly lines for perishable products were costing the company millions of dollars a year in defects, supply chain issues, and profit losses.
The Solution
The company chose Dozuki as a central solution for maintaining changeover processes. Dozuki provided their frontline employees with easy and instant access to key information from a tablet, replacing the previous system where knowledge was concentrated with a single person per shift. Initially, Dozuki was piloted at one facility and after showing positive results, it was rolled out across the enterprise. With Dozuki, work instructions now had photos and videos embedded in them, providing a visual aid to reinforce processes and reduce errors. All frontline operators were granted permission to be authors, enabling them to create a process if they didn’t see something on their site. The company also started deploying training courses to their maintenance technicians, some of whom have been in their roles for over 16 years. This digital training helped close gaps in basic manufacturing frontline knowledge, reducing potential downtime.
Operational Impact
Quantitative Benefit
Case Study missing?
Start adding your own!
Register with your work email and create a new case study profile for your business.
Related Case Studies.
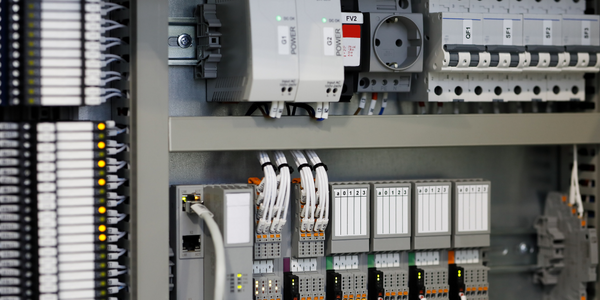
Case Study
Improving Production Line Efficiency with Ethernet Micro RTU Controller
Moxa was asked to provide a connectivity solution for one of the world's leading cosmetics companies. This multinational corporation, with retail presence in 130 countries, 23 global braches, and over 66,000 employees, sought to improve the efficiency of their production process by migrating from manual monitoring to an automatic productivity monitoring system. The production line was being monitored by ABB Real-TPI, a factory information system that offers data collection and analysis to improve plant efficiency. Due to software limitations, the customer needed an OPC server and a corresponding I/O solution to collect data from additional sensor devices for the Real-TPI system. The goal is to enable the factory information system to more thoroughly collect data from every corner of the production line. This will improve its ability to measure Overall Equipment Effectiveness (OEE) and translate into increased production efficiencies. System Requirements • Instant status updates while still consuming minimal bandwidth to relieve strain on limited factory networks • Interoperable with ABB Real-TPI • Small form factor appropriate for deployment where space is scarce • Remote software management and configuration to simplify operations
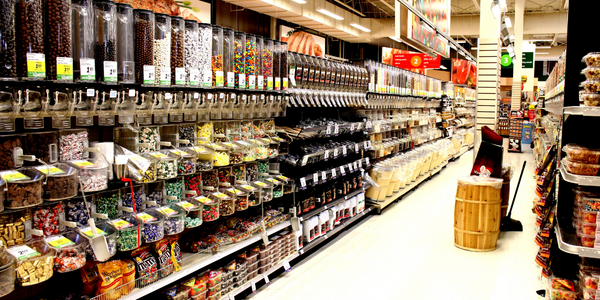
Case Study
How Sirqul’s IoT Platform is Crafting Carrefour’s New In-Store Experiences
Carrefour Taiwan’s goal is to be completely digital by end of 2018. Out-dated manual methods for analysis and assumptions limited Carrefour’s ability to change the customer experience and were void of real-time decision-making capabilities. Rather than relying solely on sales data, assumptions, and disparate systems, Carrefour Taiwan’s CEO led an initiative to find a connected IoT solution that could give the team the ability to make real-time changes and more informed decisions. Prior to implementing, Carrefour struggled to address their conversion rates and did not have the proper insights into the customer decision-making process nor how to make an immediate impact without losing customer confidence.
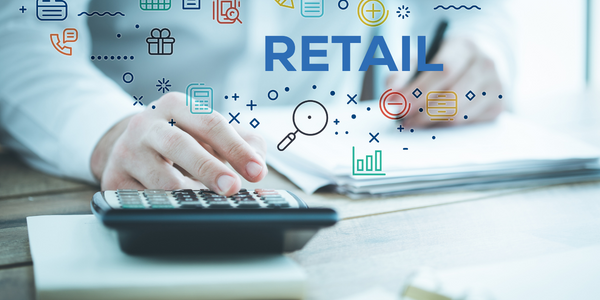
Case Study
Digital Retail Security Solutions
Sennco wanted to help its retail customers increase sales and profits by developing an innovative alarm system as opposed to conventional connected alarms that are permanently tethered to display products. These traditional security systems were cumbersome and intrusive to the customer shopping experience. Additionally, they provided no useful data or analytics.
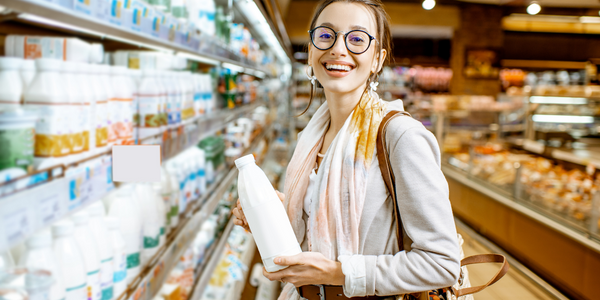
Case Study
Ensures Cold Milk in Your Supermarket
As of 2014, AK-Centralen has over 1,500 Danish supermarkets equipped, and utilizes 16 operators, and is open 24 hours a day, 365 days a year. AK-Centralen needed the ability to monitor the cooling alarms from around the country, 24 hours a day, 365 days a year. Each and every time the door to a milk cooler or a freezer does not close properly, an alarm goes off on a computer screen in a control building in southwestern Odense. This type of alarm will go off approximately 140,000 times per year, equating to roughly 400 alarms in a 24-hour period. Should an alarm go off, then there is only a limited amount of time to act before dairy products or frozen pizza must be disposed of, and this type of waste can quickly start to cost a supermarket a great deal of money.
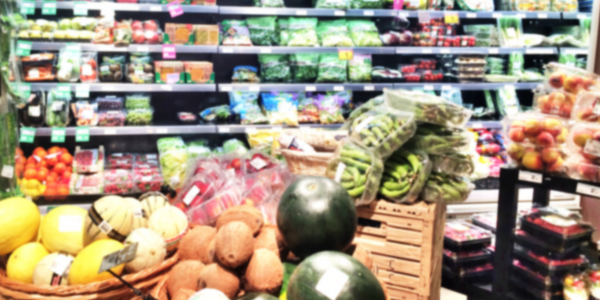
Case Study
Supermarket Energy Savings
The client had previously deployed a one-meter-per-store monitoring program. Given the manner in which energy consumption changes with external temperature, hour of the day, day of week and month of year, a single meter solution lacked the ability to detect the difference between a true problem and a changing store environment. Most importantly, a single meter solution could never identify root cause of energy consumption changes. This approach never reduced the number of truck-rolls or man-hours required to find and resolve issues.