Winners of the Sedex Best Example of Continuous Improvement Award 2017
Customer Company Size
Large Corporate
Country
- United Kingdom
Product
- Sedex Advance
- SMETA audit assessment
Tech Stack
- Supply Chain Data Management
- Sustainability Framework
Implementation Scale
- Enterprise-wide Deployment
Impact Metrics
- Cost Savings
- Environmental Impact Reduction
- Customer Satisfaction
- Employee Satisfaction
- Waste Reduction
Technology Category
- Functional Applications - Enterprise Resource Planning Systems (ERP)
Applicable Industries
- Retail
- Food & Beverage
Applicable Functions
- Procurement
- Quality Assurance
Use Cases
- Supply Chain Visibility
- Predictive Quality Analytics
- Regulatory Compliance Monitoring
Services
- System Integration
- Training
About The Customer
M&S are an international multi-channel retailer that sell clothing, food, beauty and homewear products, with a turnover split between food (58%) and general merchandise (42%). M&S have always been at the forefront of the food business, offering their customers a range of high-quality, innovative products. Their food development teams who are responsible for identifying upcoming trends and creating M&S’s signature ranges is what sets them apart from their competition. In 2016/17, they introduced 1,600 new food lines, as well as introducing new foods to their customers – from the biancoli, a cross between the cauliflower and broccoli, to new dishes from South East Asia. Understanding their customers’ demands, M&S have made their foods healthier over the past few years – from removing artificial colourings and preservatives, to extending their Eat Well and Made Without ranges.
The Challenge
M&S Food has a complex supply chain, having direct contracts with around 400 suppliers producing products at over 800 sites in 44 countries. Raw materials and commodities are sourced from more than 70 countries, and M&S estimate around 30,000 farms are used globally. M&S have always placed their main emphasis on the quality of its food products, with industry experts constantly working to bring their customers the best products. The M&S buying teams work with their suppliers to source unusual and new ingredients, to bring something new and different to their customers. However, as their network continues to expand, in both home and international markets, customers are more concerned with where and how their products are being sourced, made, and delivered. This global nature of their business means M&S and their supply chain face a number of sustainability challenges. Their customers and employees are increasingly interested in all aspects of their products’ integrity, and expect M&S to engage with their suppliers to ensure fair working conditions and respect for human rights throughout the value chain.
The Solution
M&S believes a successful business must also be environmentally and socially sustainable. Through their Plan A initiative, M&S promotes and rewards sustainable behaviour within their supply base. The How We Do Business Scorecard: M&S Food uses a supplier scorecard, with the ‘How We Do Business’ element of the scorecard supported by a sustainability framework that considers the environmental, ethical, and lean manufacturing elements which detail the building blocks to enable change in performance. This framework took 18 months to be developed and is based on: M&S’s Supplier Exchange meetings where suppliers can share their learning and experiences; and from speaking to industry experts from organisations such as the Ethical Trading Initiative (ETI) and the Carbon Trust. Suppliers must complete their scorecards each year and since these are based on this overall framework, multiple sustainability indicators are factored into the overall rating. The supplier will then be assigned a rating of either Bronze, Silver, or Gold, which depicts their overall performance against the mandatory requirements M&S has given them. The Silver Validation: Even achieving a silver status is a difficult process that requires suppliers to implement changes that must have genuine positive impacts. It is not a rating that is easily given out and the changes these suppliers implement must have genuine positive impacts to their workings. Most of M&S’s suppliers are at Bronze level, and improving to Silver status shows they are performing above the norm in the industry. It takes a supplier an average of two years of continuous work on their environmental, ethical, and lean manufacturing elements to progress from Bronze to Silver status. Once a supplier has achieved Silver status on all three frameworks (environmental, ethical, and lean manufacturing), it shows M&S that their products are being made in a more sustainable factory. Therefore, all of that supplier’s products qualify for the Plan A certification, helping M&S achieve their improved sourcing and production aims. M&S’ Plan A team will validate the three elements of a supplier to ensure that sustainability is fully embedded within the site’s operations.
Operational Impact
Quantitative Benefit
Case Study missing?
Start adding your own!
Register with your work email and create a new case study profile for your business.
Related Case Studies.

Case Study
The Kellogg Company
Kellogg keeps a close eye on its trade spend, analyzing large volumes of data and running complex simulations to predict which promotional activities will be the most effective. Kellogg needed to decrease the trade spend but its traditional relational database on premises could not keep up with the pace of demand.

Case Study
HEINEKEN Uses the Cloud to Reach 10.5 Million Consumers
For 2012 campaign, the Bond promotion, it planned to launch the campaign at the same time everywhere on the planet. That created unprecedented challenges for HEINEKEN—nowhere more so than in its technology operation. The primary digital content for the campaign was a 100-megabyte movie that had to play flawlessly for millions of viewers worldwide. After all, Bond never fails. No one was going to tolerate a technology failure that might bruise his brand.Previously, HEINEKEN had supported digital media at its outsourced datacenter. But that datacenter lacked the computing resources HEINEKEN needed, and building them—especially to support peak traffic that would total millions of simultaneous hits—would have been both time-consuming and expensive. Nor would it have provided the geographic reach that HEINEKEN needed to minimize latency worldwide.
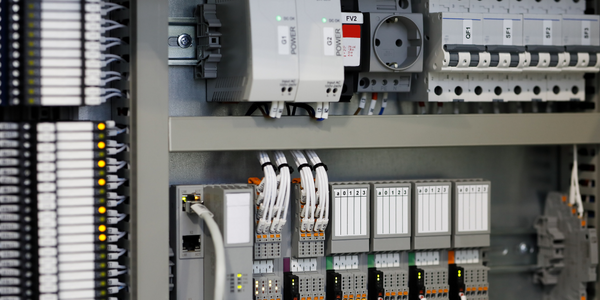
Case Study
Improving Production Line Efficiency with Ethernet Micro RTU Controller
Moxa was asked to provide a connectivity solution for one of the world's leading cosmetics companies. This multinational corporation, with retail presence in 130 countries, 23 global braches, and over 66,000 employees, sought to improve the efficiency of their production process by migrating from manual monitoring to an automatic productivity monitoring system. The production line was being monitored by ABB Real-TPI, a factory information system that offers data collection and analysis to improve plant efficiency. Due to software limitations, the customer needed an OPC server and a corresponding I/O solution to collect data from additional sensor devices for the Real-TPI system. The goal is to enable the factory information system to more thoroughly collect data from every corner of the production line. This will improve its ability to measure Overall Equipment Effectiveness (OEE) and translate into increased production efficiencies. System Requirements • Instant status updates while still consuming minimal bandwidth to relieve strain on limited factory networks • Interoperable with ABB Real-TPI • Small form factor appropriate for deployment where space is scarce • Remote software management and configuration to simplify operations

Case Study
Energy Management System at Sugar Industry
The company wanted to use the information from the system to claim under the renewable energy certificate scheme. The benefit to the company under the renewable energy certificates is Rs 75 million a year. To enable the above, an end-to-end solution for load monitoring, consumption monitoring, online data monitoring, automatic meter data acquisition which can be exported to SAP and other applications is required.
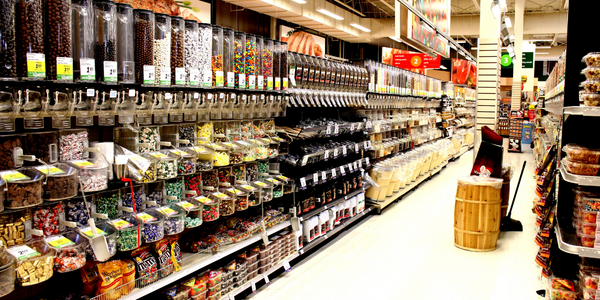
Case Study
How Sirqul’s IoT Platform is Crafting Carrefour’s New In-Store Experiences
Carrefour Taiwan’s goal is to be completely digital by end of 2018. Out-dated manual methods for analysis and assumptions limited Carrefour’s ability to change the customer experience and were void of real-time decision-making capabilities. Rather than relying solely on sales data, assumptions, and disparate systems, Carrefour Taiwan’s CEO led an initiative to find a connected IoT solution that could give the team the ability to make real-time changes and more informed decisions. Prior to implementing, Carrefour struggled to address their conversion rates and did not have the proper insights into the customer decision-making process nor how to make an immediate impact without losing customer confidence.