WinMan helps EGL Homecare stay ahead of the competition
Company Size
200-1,000
Region
- Europe
Country
- United Kingdom
Product
- WinMan
- Pegasus
Tech Stack
- Material Requirements Planning (MRP)
- Manufacturing IT Solution
Implementation Scale
- Enterprise-wide Deployment
Impact Metrics
- Customer Satisfaction
- Digital Expertise
- Productivity Improvements
Technology Category
- Functional Applications - Enterprise Resource Planning Systems (ERP)
- Functional Applications - Manufacturing Execution Systems (MES)
Applicable Industries
- Consumer Goods
- Retail
Applicable Functions
- Quality Assurance
Use Cases
- Inventory Management
- Manufacturing System Automation
- Process Control & Optimization
Services
- System Integration
- Training
About The Customer
EGL Homecare Limited is a leading European manufacturer of sponges, scourers, and non-woven cloths, based in Shoeburyness, Essex. Established in 1979, the company has grown significantly and now employs around 250 full and part-time staff, with a turnover exceeding £22 million. EGL holds a dominant position in the UK market, with over 75% market share in the all-purpose wiping cloths (retail) sector and 60% in the scourer/sponge sector. The company serves major supermarket and retail groups, producing a mix of 80% manufactured and 20% factored products. EGL's operations involve advanced manufacturing machinery and a high-speed production process to meet the demands of its extensive customer base.
The Challenge
EGL Homecare Limited faced significant challenges due to its rapid growth and the increasing complexity of its manufacturing operations. The company was producing over 1.25 million retail selling units per week, requiring a continuous flow of 15 to 20 truckloads a day. This high production volume put a strain on their existing IT control systems, leading to issues such as lack of plant visibility and difficulties in tracking work order progress. Additionally, the company faced common manufacturing problems like late delivery of raw materials, resource planning and scheduling issues, and movement of Work in Progress (WIP) through the factory. The need for a more robust and efficient system became evident as these challenges began to hinder EGL's ability to meet customer demands and maintain its market leadership.
The Solution
To address the challenges, EGL Homecare decided to replace its existing Pegasus system with WinMan, a more advanced manufacturing IT solution. The decision followed a comprehensive evaluation process, including a six-month business process mapping exercise conducted by an external consultant. The selection process involved visiting manufacturing trade shows and rigorously testing various solutions. WinMan emerged as the clear winner due to its ability to meet EGL's stock control requirements, provide a streamlined Material Requirements Planning (MRP) methodology, and support strategic production planning. The implementation of WinMan was accompanied by necessary hardware upgrades to support EGL's anticipated growth. The company also managed a significant cultural change, training key department leaders who then trained their respective teams. Despite initial challenges, the new system quickly proved its value by highlighting inefficiencies and improving trust in data accuracy.
Operational Impact
Quantitative Benefit
Case Study missing?
Start adding your own!
Register with your work email and create a new case study profile for your business.
Related Case Studies.
.png)
Case Study
Improving Vending Machine Profitability with the Internet of Things (IoT)
The vending industry is undergoing a sea change, taking advantage of new technologies to go beyond just delivering snacks to creating a new retail location. Intelligent vending machines can be found in many public locations as well as company facilities, selling different types of goods and services, including even computer accessories, gold bars, tickets, and office supplies. With increasing sophistication, they may also provide time- and location-based data pertaining to sales, inventory, and customer preferences. But at the end of the day, vending machine operators know greater profitability is driven by higher sales and lower operating costs.
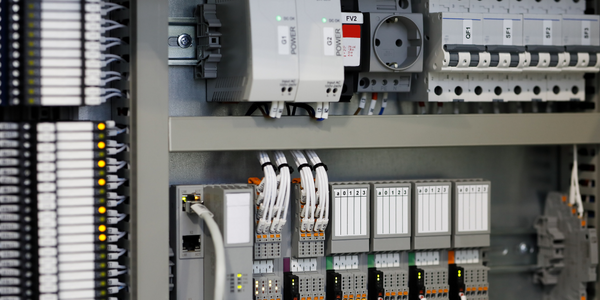
Case Study
Improving Production Line Efficiency with Ethernet Micro RTU Controller
Moxa was asked to provide a connectivity solution for one of the world's leading cosmetics companies. This multinational corporation, with retail presence in 130 countries, 23 global braches, and over 66,000 employees, sought to improve the efficiency of their production process by migrating from manual monitoring to an automatic productivity monitoring system. The production line was being monitored by ABB Real-TPI, a factory information system that offers data collection and analysis to improve plant efficiency. Due to software limitations, the customer needed an OPC server and a corresponding I/O solution to collect data from additional sensor devices for the Real-TPI system. The goal is to enable the factory information system to more thoroughly collect data from every corner of the production line. This will improve its ability to measure Overall Equipment Effectiveness (OEE) and translate into increased production efficiencies. System Requirements • Instant status updates while still consuming minimal bandwidth to relieve strain on limited factory networks • Interoperable with ABB Real-TPI • Small form factor appropriate for deployment where space is scarce • Remote software management and configuration to simplify operations
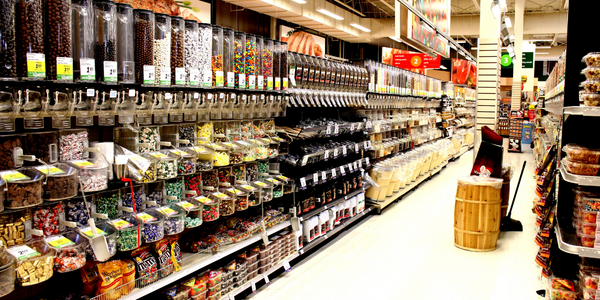
Case Study
How Sirqul’s IoT Platform is Crafting Carrefour’s New In-Store Experiences
Carrefour Taiwan’s goal is to be completely digital by end of 2018. Out-dated manual methods for analysis and assumptions limited Carrefour’s ability to change the customer experience and were void of real-time decision-making capabilities. Rather than relying solely on sales data, assumptions, and disparate systems, Carrefour Taiwan’s CEO led an initiative to find a connected IoT solution that could give the team the ability to make real-time changes and more informed decisions. Prior to implementing, Carrefour struggled to address their conversion rates and did not have the proper insights into the customer decision-making process nor how to make an immediate impact without losing customer confidence.
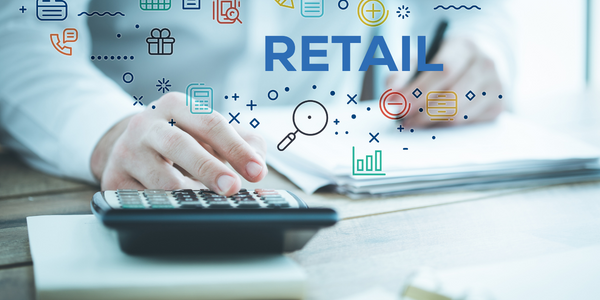
Case Study
Digital Retail Security Solutions
Sennco wanted to help its retail customers increase sales and profits by developing an innovative alarm system as opposed to conventional connected alarms that are permanently tethered to display products. These traditional security systems were cumbersome and intrusive to the customer shopping experience. Additionally, they provided no useful data or analytics.