WinMan ensures Lean and precise production at Lander Automotive
Company Size
1,000+
Region
- Europe
Country
- United Kingdom
Product
- WinMan ERP
- WinMan mobile functionality
Tech Stack
- CNC technology
- Kanban system
- Barcoding
Implementation Scale
- Enterprise-wide Deployment
Impact Metrics
- Customer Satisfaction
- Digital Expertise
- Productivity Improvements
Technology Category
- Analytics & Modeling - Real Time Analytics
- Functional Applications - Enterprise Resource Planning Systems (ERP)
- Functional Applications - Remote Monitoring & Control Systems
Applicable Industries
- Automotive
Applicable Functions
- Process Manufacturing
- Quality Assurance
- Warehouse & Inventory Management
Use Cases
- Inventory Management
- Predictive Maintenance
- Process Control & Optimization
- Real-Time Location System (RTLS)
Services
- Software Design & Engineering Services
- System Integration
About The Customer
Lander Automotive, based in Birmingham, is a tier one supplier to leading car manufacturers. The company specializes in the production of vehicle fluid and air carrying systems. Recently, Lander Automotive invested around £5 million in a new facility to service a major new order. The emphasis at this new plant is on precision planning of supplier inputs, minimal work in progress, and lean processes throughout. The new plant utilizes the latest CNC and automation technology and includes clean room manufacturing areas. Lander Automotive operates a lean production discipline with minimal work in progress and extensive use of Kanbans. The company relies on WinMan ERP software as a key enabler behind its lean operations, ensuring that supplies are in place at the right time to meet high production demands.
The Challenge
Lander Automotive, a tier one supplier to leading car makers, faced the challenge of ensuring precision planning of supplier inputs, minimal work in progress, and lean processes throughout their new facility. The new plant, which required a significant investment of approximately £5 million, needed to service a major new order to supply vehicle fluid and air carrying systems. The company needed to ensure that supplies were in place at the right time to meet the high demand of 10 million engine parts per year, corresponding to thousands of different part numbers, within specified 4-hour time slots. Additionally, Lander Automotive needed to maintain a lean production discipline with minimal work in progress and extensive use of Kanbans, while also ensuring traceability and accuracy of information throughout the production process.
The Solution
Lander Automotive implemented WinMan ERP software to ensure that supplies were in place at the right time to meet production demands. The software assesses everything that needs to be sourced to meet orders on production schedules and puts together bills of materials for each part number. It then generates orders which are automatically emailed to Lander’s suppliers. Weekly schedules are sent electronically to Lander, including two weeks’ worth of firm schedules and a further four weeks’ estimated schedules. Lander updates the firm schedules, deletes old estimated schedules, adds new ones, and re-assesses what it needs. A further daily MRP is run to fine-tune production plans. Kanbans are used throughout the production process, and parts are tracked with hand-held scanners and barcodes generated by WinMan as they pass through each production process. Shop floor data collection (SFDC) using WinMan mobile functionality is used extensively, providing precise information on the current state of each order. The production cell team leaders request the parts they need via WinMan, which translates into a picking list for the fork lift driver to collect from the secure stores. The picking list is displayed on a tablet PC on the fork lift truck, and as the driver picks the parts, they are scanned out of stores and come off the picking list. The parts are then delivered to flow racks on the production floor that act as intermediate Kanbans, and are decanted off into smaller Kanban boxes to replenish supplies at the cell. As the part goes through each stage of production, it is scanned in and out of each process using WinMan mobile functionality to check its progress. Finally, when the part is finished, it is scanned into the warehouse, and all the items used to make it are back-flushed from the stores inventory.
Operational Impact
Quantitative Benefit
Case Study missing?
Start adding your own!
Register with your work email and create a new case study profile for your business.
Related Case Studies.
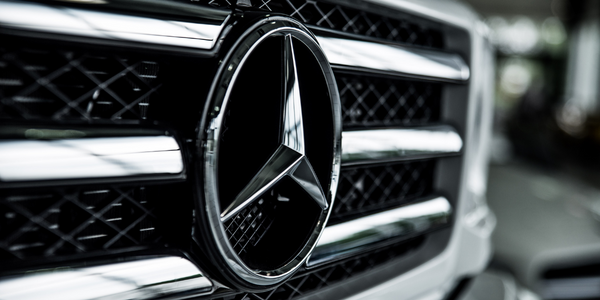
Case Study
Integral Plant Maintenance
Mercedes-Benz and his partner GAZ chose Siemens to be its maintenance partner at a new engine plant in Yaroslavl, Russia. The new plant offers a capacity to manufacture diesel engines for the Russian market, for locally produced Sprinter Classic. In addition to engines for the local market, the Yaroslavl plant will also produce spare parts. Mercedes-Benz Russia and his partner needed a service partner in order to ensure the operation of these lines in a maintenance partnership arrangement. The challenges included coordinating the entire maintenance management operation, in particular inspections, corrective and predictive maintenance activities, and the optimizing spare parts management. Siemens developed a customized maintenance solution that includes all electronic and mechanical maintenance activities (Integral Plant Maintenance).
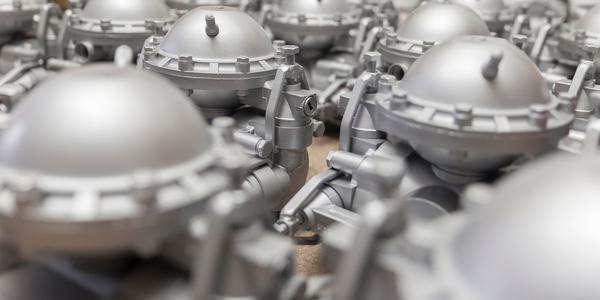
Case Study
Monitoring of Pressure Pumps in Automotive Industry
A large German/American producer of auto parts uses high-pressure pumps to deburr machined parts as a part of its production and quality check process. They decided to monitor these pumps to make sure they work properly and that they can see any indications leading to a potential failure before it affects their process.