Westin Design extract serious benefits from the WinMan system
Company Size
11-200
Region
- Europe
Country
- Ireland
- United Kingdom
Product
- WinMan ERP System
- WinMan Product Configurator
- WinMan Production Scheduling
- WinMan CRM/SRM
- WinMan Go mobile App
Tech Stack
- ERP System
- Product Configurator
- Production Scheduling
- CRM/SRM
- Mobile App
Implementation Scale
- Enterprise-wide Deployment
Impact Metrics
- Customer Satisfaction
- Digital Expertise
- Productivity Improvements
Technology Category
- Functional Applications - Enterprise Resource Planning Systems (ERP)
- Functional Applications - Product Data Management Systems
- Functional Applications - Warehouse Management Systems (WMS)
Applicable Industries
- Construction & Infrastructure
- Consumer Goods
Applicable Functions
- Business Operation
- Sales & Marketing
- Warehouse & Inventory Management
Use Cases
- Inventory Management
- Predictive Maintenance
- Supply Chain Visibility
- Track & Trace of Assets
- Warehouse Automation
Services
- Software Design & Engineering Services
- System Integration
- Training
About The Customer
Westin Design, based in Huddersfield, West Yorkshire, is a manufacturer and supplier of innovative and exclusive extraction solutions for high-end domestic range kitchens. The privately-owned company caters to kitchen design studios, architects, and developers for conversions, refurbishments, and new builds across the UK and Ireland. Over the past decade, Westin Design has experienced consistent year-on-year growth in turnover. They offer complete turnkey extraction solutions, including standard or custom hoods, built-in units, panels, and various fan options. As manufacturers, they provide customers with security of supply and control over design, quality, and delivery.
The Challenge
Westin Design faced the challenge of meeting the growing demand for high-end domestic kitchen extraction solutions while maintaining high productivity and on-time delivery. The company needed a system that could handle custom orders efficiently, streamline production scheduling, and improve customer and supplier relationship management. Additionally, they required a solution to manage their warehouse operations effectively and reduce stock levels in line with demand.
The Solution
Westin Design implemented the WinMan ERP system, which includes the Product Configurator, Production Scheduling, CRM/SRM, and Warehouse Management functions. The Product Configurator replaced previous data on spreadsheets, allowing for fast and consistent quotes for custom-made extractors. It builds a complete product structure for manufacturing, with options selected determining later choices and numerical entries. The Production Scheduling system uses the data from the Product Configurator to determine exact delivery dates and ensure timely processing of manufacturing and purchase orders. The CRM/SRM system provides a single access point for information related to customers and suppliers, streamlining relationship management and creating opportunities for increased sales. The Warehouse Management function allows for complete track and trace of all parts and finished goods, reducing stock levels by relating them to demand. Additionally, the WinMan Go mobile App was introduced for picking and packing, feeding data directly into the main WinMan system.
Operational Impact
Quantitative Benefit
Case Study missing?
Start adding your own!
Register with your work email and create a new case study profile for your business.
Related Case Studies.
.png)
Case Study
Improving Vending Machine Profitability with the Internet of Things (IoT)
The vending industry is undergoing a sea change, taking advantage of new technologies to go beyond just delivering snacks to creating a new retail location. Intelligent vending machines can be found in many public locations as well as company facilities, selling different types of goods and services, including even computer accessories, gold bars, tickets, and office supplies. With increasing sophistication, they may also provide time- and location-based data pertaining to sales, inventory, and customer preferences. But at the end of the day, vending machine operators know greater profitability is driven by higher sales and lower operating costs.

Case Study
IoT System for Tunnel Construction
The Zenitaka Corporation ('Zenitaka') has two major business areas: its architectural business focuses on structures such as government buildings, office buildings, and commercial facilities, while its civil engineering business is targeted at structures such as tunnels, bridges and dams. Within these areas, there presented two issues that have always persisted in regard to the construction of mountain tunnels. These issues are 'improving safety" and "reducing energy consumption". Mountain tunnels construction requires a massive amount of electricity. This is because there are many kinds of electrical equipment being used day and night, including construction machinery, construction lighting, and ventilating fan. Despite this, the amount of power consumption is generally not tightly managed. In many cases, the exact amount of power consumption is only ascertained when the bill from the power company becomes available. Sometimes, corporations install demand-monitoring equipment to help curb the maximum power demanded. However, even in these cases, the devices only allow the total volume of power consumption to be ascertained, or they may issue warnings to prevent the contracted volume of power from being exceeded. In order to tackle the issue of reducing power consumption, it was first necessary to obtain an accurate breakdown of how much power was being used in each particular area. In other words, we needed to be able to visualize the amount of power being consumed. Safety, was also not being managed very rigorously. Even now, tunnel construction sites often use a 'name label' system for managing entry into the work site. Specifically, red labels with white reverse sides that bear the workers' names on both sides are displayed at the tunnel work site entrance. The workers themselves then flip the name label to the appropriate side when entering or exiting from the work site to indicate whether or not they are working inside the tunnel at any given time. If a worker forgets to flip his or her name label when entering or exiting from the tunnel, management cannot be performed effectively. In order to tackle the challenges mentioned above, Zenitaka decided to build a system that could improve the safety of tunnel construction as well as reduce the amount of power consumed. In other words, this new system would facilitate a clear picture of which workers were working in each location at the mountain tunnel construction site, as well as which processes were being carried out at those respective locations at any given time. The system would maintain the safety of all workers while also carefully controlling the electrical equipment to reduce unnecessary power consumption. Having decided on the concept, our next concern was whether there existed any kind of robust hardware that would not break down at the construction work site, that could move freely in response to changes in the working environment, and that could accurately detect workers and vehicles using radio frequency identification (RFID). Given that this system would involve many components that were new to Zenitaka, we decided to enlist the cooperation of E.I.Sol Co., Ltd. ('E.I.Sol') as our joint development partner, as they had provided us with a highly practical proposal.
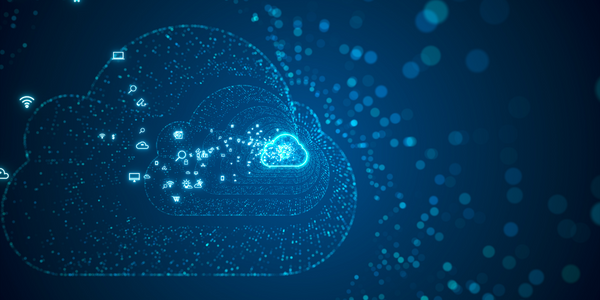
Case Study
Splunk Partnership Ties Together Big Data & IoT Services
Splunk was faced with the need to meet emerging customer demands for interfacing IoT projects to its suite of services. The company required an IoT partner that would be able to easily and quickly integrate with its Splunk Enterprise platform, rather than allocating development resources and time to building out an IoT interface and application platform.
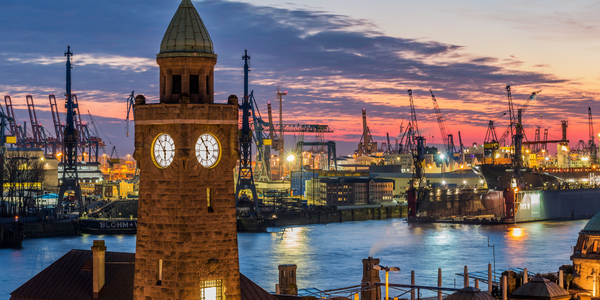
Case Study
Bridge monitoring in Hamburg Port
Kattwyk Bridge is used for both rail and road transport, and it has played an important role in the Port of Hamburg since 1973. However, the increasing pressure from traffic requires a monitoring solution. The goal of the project is to assess in real-time the bridge's status and dynamic responses to traffic and lift processes.
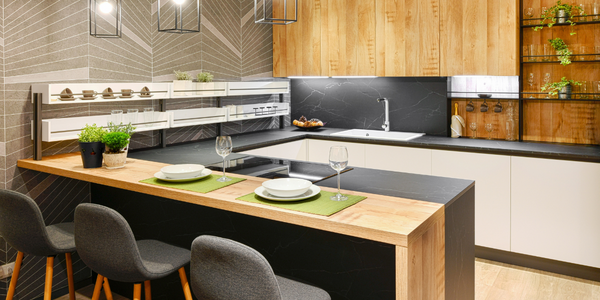
Case Study
Series Production with Lot-size-1 Flexibility
Nobilia manufactures customized fitted kitchens with a lot size of 1. They require maximum transparency of tracking design data and individual processing steps so that they can locate a particular piece of kitchen furniture in the sequence of processes.