Warehouse Management helps GUESS? makeover its warehouse and distribution system
Company Size
1,000+
Region
- America
- Asia
Country
- Canada
- China
- Hong Kong
- United States
Product
- Manhattan Associates’ Warehouse Management
- Jesta I.S. (formerly Essentus)
- JDA
Tech Stack
- IBM i
- Motorola RF equipment
Implementation Scale
- Enterprise-wide Deployment
Impact Metrics
- Cost Savings
- Customer Satisfaction
- Productivity Improvements
Technology Category
- Functional Applications - Enterprise Resource Planning Systems (ERP)
- Functional Applications - Warehouse Management Systems (WMS)
Applicable Industries
- Consumer Goods
- Retail
Applicable Functions
- Logistics & Transportation
- Warehouse & Inventory Management
Use Cases
- Inventory Management
- Supply Chain Visibility
- Warehouse Automation
Services
- Software Design & Engineering Services
- System Integration
About The Customer
In 1981, the Marciano brothers set out to change the perception of jeans forever by launching the GUESS? clothing line. Retailers were skeptical, but after a leading retailer’s sample order sold out in hours, retailers around the globe changed their minds about denim and GUESS?. Today, GUESS? is one of the most widely recognized brands in the world. It sells its lines through more than 300 retail specialty stores, a wide range of department stores and online. In addition, it licenses its name for many accessories, including eyewear, footwear, jewelry and watches.
The Challenge
GUESS?’s distribution center was insufficient to meet rapidly growing demand and unable to reach most customers efficiently. The company’s success placed great pressure on its distribution and warehouse management capabilities. In 1999, most customers were east of the Mississippi and being served by one DC in Los Angeles, California. This geographic challenge—combined with the fact that the DC was “exploding at the seams” due to increased demand—prompted GUESS? to revamp its distribution network.
The Solution
With guidance from KSA, a premier global management consulting firm, GUESS? opened a new DC in Louisville, Kentucky to serve as a prototype for upgrades to the Los Angeles facility. KSA recommended using an advanced warehouse management system to run the new location. GUESS? initiated a relationship with Manhattan Associates, based on the strength of Manhattan’s supply chain software and its reputation as the warehouse management expert for retailers and consumer goods manufacturers shipping to retail. Manhattan’s supply chain software has been flexible enough to support several different inventory methods for GUESS?. At one point the company mixed all multi-channel inventory together. Today, the company segregates wholesale and retail (including direct-to-consumer) inventory to better support its company structure as two business sectors under separate P&Ls. Each business unit within GUESS? utilizes an independent host system: Jesta I.S. (formerly Essentus) for wholesale and JDA for retail. When the two businesses shared inventory, retail orders from JDA were passed to Jesta and then sent to Warehouse Management for fulfillment. This offered more control as inventory was allocated from wholesale to retail, giving the wholesale business preference on inventory at crunch times.
Operational Impact
Quantitative Benefit
Case Study missing?
Start adding your own!
Register with your work email and create a new case study profile for your business.
Related Case Studies.
.png)
Case Study
Improving Vending Machine Profitability with the Internet of Things (IoT)
The vending industry is undergoing a sea change, taking advantage of new technologies to go beyond just delivering snacks to creating a new retail location. Intelligent vending machines can be found in many public locations as well as company facilities, selling different types of goods and services, including even computer accessories, gold bars, tickets, and office supplies. With increasing sophistication, they may also provide time- and location-based data pertaining to sales, inventory, and customer preferences. But at the end of the day, vending machine operators know greater profitability is driven by higher sales and lower operating costs.
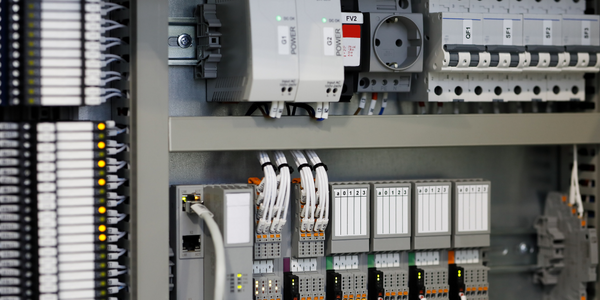
Case Study
Improving Production Line Efficiency with Ethernet Micro RTU Controller
Moxa was asked to provide a connectivity solution for one of the world's leading cosmetics companies. This multinational corporation, with retail presence in 130 countries, 23 global braches, and over 66,000 employees, sought to improve the efficiency of their production process by migrating from manual monitoring to an automatic productivity monitoring system. The production line was being monitored by ABB Real-TPI, a factory information system that offers data collection and analysis to improve plant efficiency. Due to software limitations, the customer needed an OPC server and a corresponding I/O solution to collect data from additional sensor devices for the Real-TPI system. The goal is to enable the factory information system to more thoroughly collect data from every corner of the production line. This will improve its ability to measure Overall Equipment Effectiveness (OEE) and translate into increased production efficiencies. System Requirements • Instant status updates while still consuming minimal bandwidth to relieve strain on limited factory networks • Interoperable with ABB Real-TPI • Small form factor appropriate for deployment where space is scarce • Remote software management and configuration to simplify operations
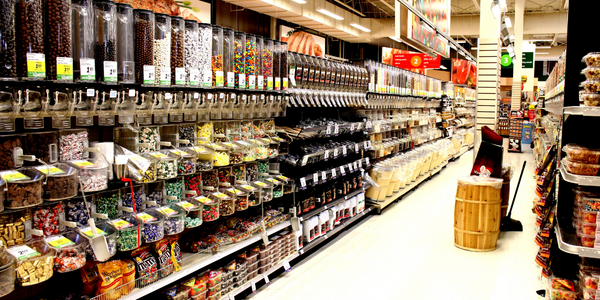
Case Study
How Sirqul’s IoT Platform is Crafting Carrefour’s New In-Store Experiences
Carrefour Taiwan’s goal is to be completely digital by end of 2018. Out-dated manual methods for analysis and assumptions limited Carrefour’s ability to change the customer experience and were void of real-time decision-making capabilities. Rather than relying solely on sales data, assumptions, and disparate systems, Carrefour Taiwan’s CEO led an initiative to find a connected IoT solution that could give the team the ability to make real-time changes and more informed decisions. Prior to implementing, Carrefour struggled to address their conversion rates and did not have the proper insights into the customer decision-making process nor how to make an immediate impact without losing customer confidence.
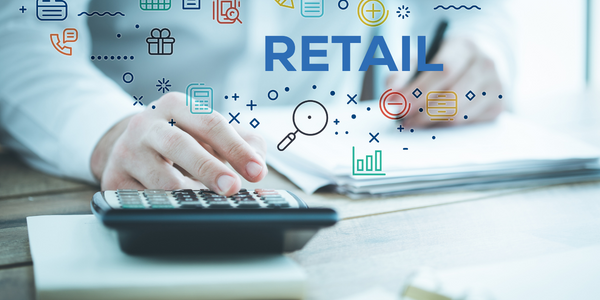
Case Study
Digital Retail Security Solutions
Sennco wanted to help its retail customers increase sales and profits by developing an innovative alarm system as opposed to conventional connected alarms that are permanently tethered to display products. These traditional security systems were cumbersome and intrusive to the customer shopping experience. Additionally, they provided no useful data or analytics.