Technology Category
- Application Infrastructure & Middleware - Data Exchange & Integration
- Application Infrastructure & Middleware - Middleware, SDKs & Libraries
Applicable Industries
- Consumer Goods
- Pharmaceuticals
Applicable Functions
- Procurement
- Product Research & Development
Services
- System Integration
- Testing & Certification
About The Customer
Valisure is America’s first pharmacy to chemically validate all its products at no additional cost to consumers. The company was founded by Adam Clark-Joseph and David Light, friends since their Yale days, after Adam suffered serious complications due to batch variability of his anticonvulsant medication. Shocked by the lack of adequate safeguards, they were determined to create a solution. They assembled a team of scientists, entrepreneurs, and experts to develop and deploy a solution, resulting in the creation of Valisure. The company is dedicated to preventing anyone from suffering adverse effects from low-quality medications.
The Challenge
Valisure, a pharmacy dedicated to chemically validating all its products, faced several challenges. The company had a unique proposition of validating and signing each lot of every medication sold, but they lacked a platform to display and market this differentiation. They also needed to certify with LegitScript to offer their prescription medications online. Additionally, they had signed a contract with a new payment provider, which needed to be integrated with their PrimeRx ERP. Their investors were demanding significant progress in launching a solution, putting their future funding at risk. Lastly, Valisure could only sell specific prescription medications to clients in certain states. They needed a solution that could limit the ability to view or purchase prescription medications based on the state the client was ordering for.
The Solution
To address these challenges, Clarity, a technology solutions provider, was brought in. They had a tight deadline of one month to launch a custom eCommerce solution that was also HIPAA compliant. Leveraging their experience from a previous HIPAA compliant client project, Clarity replicated that environment for Valisure. They integrated the new payment gateway, built out a custom registration process for prescription drug approval, and launched the site for HIPAA validation, all within the 4-week timeframe. The PrimeRx integration was pushed to a future phase and a custom design was dropped. The front-end CMS used was DNN’s Evoq Professional, and technologies like HTML5, CSS3, Modernizr, Clarity Connect, JavaScript, JQuery, Telerik controls, and various DNN modules were used for various features and functionality.
Operational Impact
Quantitative Benefit
Case Study missing?
Start adding your own!
Register with your work email and create a new case study profile for your business.
Related Case Studies.
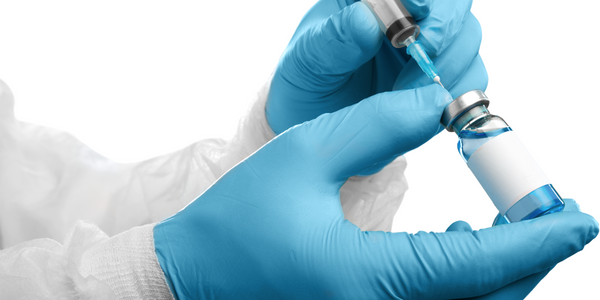
Case Study
Case Study: Pfizer
Pfizer’s high-performance computing software and systems for worldwide research and development support large-scale data analysis, research projects, clinical analytics, and modeling. Pfizer’s computing services are used across the spectrum of research and development efforts, from the deep biological understanding of disease to the design of safe, efficacious therapeutic agents.
.png)
Case Study
Improving Vending Machine Profitability with the Internet of Things (IoT)
The vending industry is undergoing a sea change, taking advantage of new technologies to go beyond just delivering snacks to creating a new retail location. Intelligent vending machines can be found in many public locations as well as company facilities, selling different types of goods and services, including even computer accessories, gold bars, tickets, and office supplies. With increasing sophistication, they may also provide time- and location-based data pertaining to sales, inventory, and customer preferences. But at the end of the day, vending machine operators know greater profitability is driven by higher sales and lower operating costs.
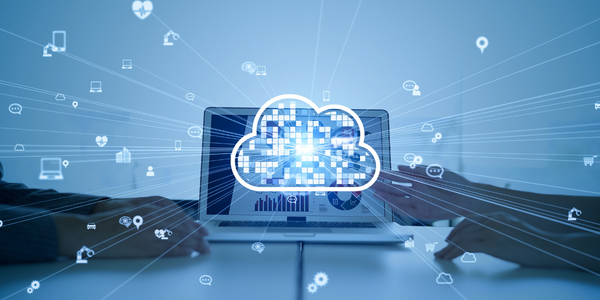
Case Study
Fusion Middleware Integration on Cloud for Pharma Major
Customer wanted a real-time, seamless, cloud based integration between the existing on premise and cloud based application using SOA technology on Oracle Fusion Middleware Platform, a Contingent Worker Solution to collect, track, manage and report information for on-boarding, maintenance and off-boarding of contingent workers using a streamlined and Integrated business process, and streamlining of integration to the back-end systems and multiple SaaS applications.
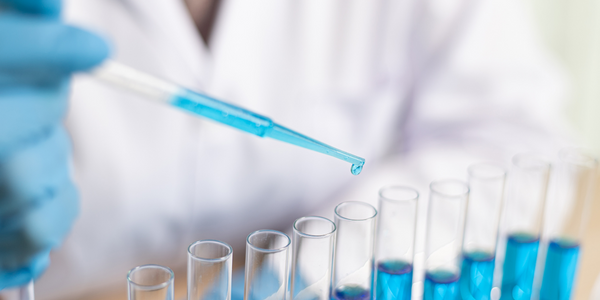
Case Study
Process Control System Support
In many automated production facilities, changes are made to SIMATIC PCS 7 projects on a daily basis, with individual processes often optimised by multiple workers due to shift changes. Documentation is key here, as this keeps workers informed about why a change was made. Furthermore, SIMATIC PCS 7 installations are generally used in locations where documentation is required for audits and certification. The ability to track changes between two software projects is not only an invaluable aid during shift changes, but also when searching for errors or optimising a PCS 7 installation. Every change made to the system is labour-intensive and time-consuming. Moreover, there is also the risk that errors may occur. If a change is saved in the project, then the old version is lost unless a backup copy was created in advance. If no backup was created, it will no longer be possible to return to the previous state if and when programming errors occur. Each backup denotes a version used by the SIMATIC PCS 7 system to operate an installation. To correctly interpret a version, information is required on WHO changed WHAT, WHERE, WHEN and WHY: - Who created the version/who is responsible for the version? - Who released the version? - What was changed in the version i.e. in which block or module of the SIMATIC PCS 7 installation were the changes made? - When was the version created? Is this the latest version or is there a more recent version? - Why were the changes made to the version? If they are part of a regular maintenance cycle, then is the aim to fix an error or to improve production processes? - Is this particular version also the version currently being used in production? The fact that SIMATIC PCS 7 projects use extremely large quantities of data complicates the situation even further, and it can take a long time to load and save information as a result. Without a sustainable strategy for operating a SIMATIC PCS 7 installation, searching for the right software version can become extremely time-consuming and the installation may run inefficiently as a result.
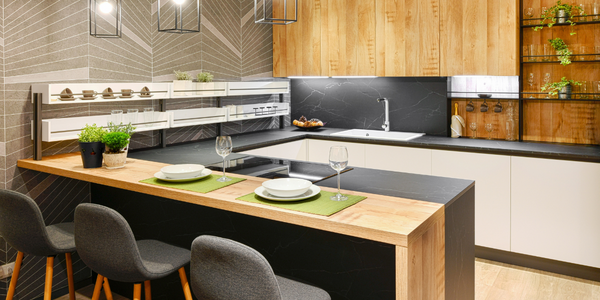
Case Study
Series Production with Lot-size-1 Flexibility
Nobilia manufactures customized fitted kitchens with a lot size of 1. They require maximum transparency of tracking design data and individual processing steps so that they can locate a particular piece of kitchen furniture in the sequence of processes.