Unearthing Profitability via Cost to Serve Optimization
Company Size
1,000+
Region
- America
Country
- United States
Product
- anyLogistixTM
Tech Stack
- Supply Chain Design and Optimization
Implementation Scale
- Enterprise-wide Deployment
Impact Metrics
- Cost Savings
- Productivity Improvements
Technology Category
- Analytics & Modeling - Predictive Analytics
- Functional Applications - Enterprise Resource Planning Systems (ERP)
Applicable Industries
- Agriculture
- Chemicals
Applicable Functions
- Logistics & Transportation
- Warehouse & Inventory Management
Use Cases
- Inventory Management
- Predictive Maintenance
- Supply Chain Visibility
Services
- System Integration
- Training
About The Customer
For over 100 years, Tessenderlo Group, a 1.6B € diversified industrial organization, has been delivering world-class products and solutions around agriculture and bio-residuals. Presently, the organization operates at more than 100 locations across the globe, including 15 production plants and over 100 distribution terminals. Tessenderlo Group is known for its commitment to innovation and sustainability, providing essential products and services that support the agricultural sector and contribute to environmental conservation. The company has a strong presence in North America, where it has experienced significant growth and expansion.
The Challenge
As the population of a market increases, so does the demand for agriculture products. In North America, Tessenderlo has enjoyed steady organic growth since its inception. However, growth does not come without its challenges. With constraints in their network becoming more evident, Tessenderlo recognized transportation asset availability, accessibility of transport modes, production capacity utilization, and operating costs needed to improve. Presented with this daunting task, Tessenderlo quickly realized it was in their best interest to hone in on these challenges by creating a practice dedicated to Supply Chain Analytics.
The Solution
In order to rapidly get their Supply Chain Analytics capabilities off the ground, the Tessenderlo North American team selected anyLogistixTM as their primary Supply Chain Design and Optimization platform given the exceptional customer service and rapid time-to-value for solutions. The initial project Tessenderlo tackled was to optimize the cost-to-serve for two of its core product offerings. These products were produced and distributed out of multiple plant locations, creating complexities around competing production resources, available storage, and transportation assets. With the guidance of the anyLogistixTM team, the Tessenderlo Supply Chain Analytics practice decided on the following approach: Create a baseline scenario model to best understand the current state of the supply chain with a key focus on plant capacity utilization, production costs allocation, transportation spending, and terminal distribution costs. Run a series of scenarios to identify an array of optimal methods to serve end customers. The primary objective was to uncover how asset utilization and associated costs (plant, production, storage, transportation, etc.) varied when shifting production and distribution among the various plants. Review the top 10 scenarios with the Tessenderlo key stakeholder project team to validate the results and decide on the most appropriate future state scenario to implement.
Operational Impact
Quantitative Benefit
Case Study missing?
Start adding your own!
Register with your work email and create a new case study profile for your business.
Related Case Studies.
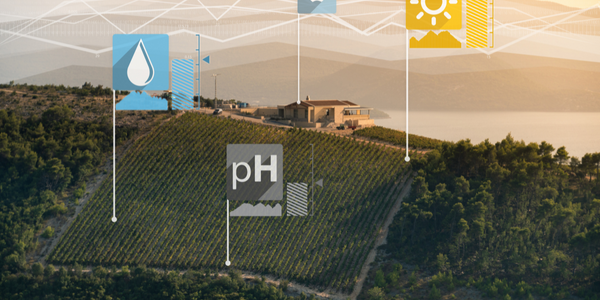
Case Study
Intelligent Farming with ThingWorx Analytics
Z Farms was facing three challenges: costly irrigation systems with water as a limited resource, narrow optimal ranges of soil moisture for growth with difficult maintenance and farm operators could not simply turn on irrigation systems like a faucet.
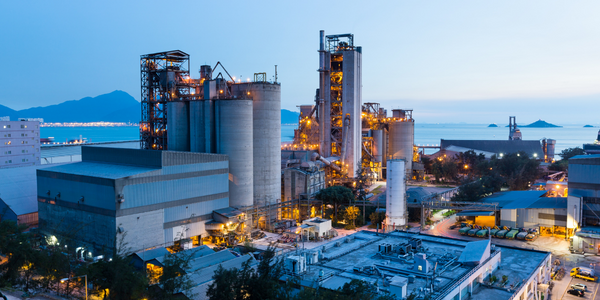
Case Study
Honeywell - Tata Chemicals Improves Data Accessibility with OneWireless
Tata was facing data accessibility challenges in the cement plant control room tapping signals from remote process control areas and other distant locations, including the gas scrubber. Tata needed a wireless solution to extend its control network securely to remote locations that would also provide seamless communication with existing control applications.
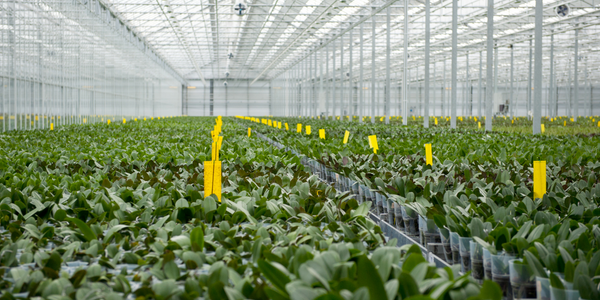
Case Study
Greenhouse Intelligent Monitoring and Control Solution
Farming Orchids is the most successful form of precision farming in Taiwan, and also the most exported flower. Orchids need a specific temperature and humidity conditions to grow and bloom, and its flowering time may not be in line with market demands, so the price collapses when there is overproduction. Therefore, some farmers began to import automated greenhouse control systems for breeding and forcing, which not only improves quality, but also effectively controls the production period and yield to ensure revenue. In 2012, an orchid farmer built a Forcing Greenhouse of about 200 pings (approximately 661 Square Meters) in Tainan, Taiwan. The system integrator adopted Advantech’s APAX-5000 series programmable automation controllers to build the control platform, coupled with Advantech WebAccess HMI/SCADA software, to achieve cloud monitoring. The staff of the orchid field can monitor important data anytime via smart phone, iPad, and other handheld devices, and control the growth and flowering conditions. System requirements: In the past, most environmental control systems of orchid greenhouses in Taiwan used PLCs (Programmable Logic Controller) with poorscalability and control, and could not be connected to the Internet formonitoring from the cloud. For advanced database analysis and networking capability, the PC platform must be adopted. Therefore, PAC Systems (Programmable Automation Controller) with both PLC programming capabilities andPC functions is a better choice.The environmental control of the Orchid greenhouse switches on and off devices like fan, shade net, cooling/heat pump, liquid flow control, water-cooling wall etc. It is controlled by a control panel of electric controllers, and is driven by a motor, to adjust the greenhouse temperature, humidity, and other environmental conditions to the set parameters.
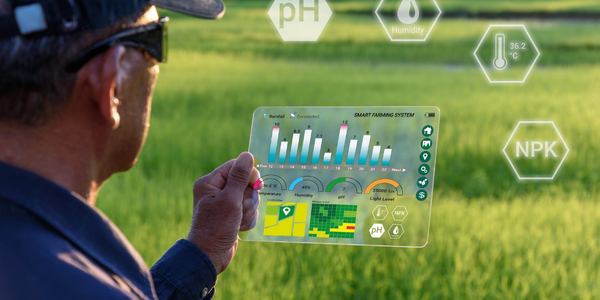
Case Study
Enabling Internet of Things Innovation in Agriculture
DigiBale, wanted to apply technology know-how and IP from implementations successfully to more agriculture sectors including cotton, forestry, sugarcane and cattle. However, farmers and growers still have worries about the connected technology.