Customer Company Size
Large Corporate
Region
- Asia
Country
- Japan
Product
- Mule ESB Enterprise
- SAP ECC ERP system
- MuleSoft Enterprise Gateway for SAP
Tech Stack
- SAP ERP
- Oracle
- SQL Server
Implementation Scale
- Enterprise-wide Deployment
Impact Metrics
- Cost Savings
- Productivity Improvements
Technology Category
- Application Infrastructure & Middleware - API Integration & Management
- Application Infrastructure & Middleware - Data Exchange & Integration
Applicable Functions
- Logistics & Transportation
- Procurement
Use Cases
- Process Control & Optimization
- Supply Chain Visibility
Services
- System Integration
About The Customer
Ube Industries is a diversified company that was founded in 1897 as a coal mining company in Ube City, Japan. The company now offers a wide range of products through more than 140 group companies, two headquarters, and multiple factories. The company operates in a complex network of internal management portals, frequently delivered via SAP, to manage data from these companies and factories across disparate production, logistics, and accounting systems. The company operates both in Japan and worldwide, and its website can be found at www.ube-ind.co.jp/english.
The Challenge
Ube Industries had adopted a commercial enterprise application integration (EAI) tool over a decade ago. However, as the volume and type of endpoints requiring integration increased dramatically over time, Ube’s legacy EAI tool could not scale to meet growing business needs. By 2013, the number of endpoints had risen to over 100 and system failures happened often. Identifying the root cause became increasingly difficult and a single bug could impact large portions of the architecture. When system downtime did occur, transactions within the affected systems ground to a halt. Recovering from these system failures required manual intervention, which increased dependency on individual skills and lengthened resolution time. With support of that EAI tool ending in January 2013, the mission critical nature of the SAP logistics and accounting systems, and business impacts associated with failed or delayed payments and distributions, Ube decided to move to a new architecture.
The Solution
Ube’s team decided to move to a new hub system that leveraged an enterprise service bus (ESB). The ESB would integrate business data between SAP ERP, Oracle, SQL Server, and over 100 homegrown and legacy applications. To minimize migration time to market and resolve issues with the stability and maintainability of their existing architecture, Ube identified that the best integration solution should meet the following criteria: Ability to develop custom functions and logic with minimal system modifications, Easy to use development tooling, Availability of development resources, Certified, out-of-the box connectivity with the SAP ECC ERP system, High availability and scalability. The result of Ube's evaluation on several candidate EAI and ESB products showed that only Mule ESB Enterprise met all five criteria. As an open source platform, MuleSoft delivers the world's largest integration developer community with over 150,000 members. The Mule Studio graphical design environment provided the Ube team with an easy on-ramp and powerful tooling for custom development. The SAP Certified MuleSoft Enterprise Gateway for SAP provided Ube with bi-directional communication to all of Ube's SAP solutions via BAPI. Through collaboration with OGIS-RI (a Japanese system integrator and preferred Mule partner), Ube's team, Ube Industries and UIS (a Japanese system integrator and a group company of Ube Industries), SAP and 100 other enterprise systems with 1100 interfaces were connected in just 3 months on Mule ESB.
Operational Impact
Quantitative Benefit
Case Study missing?
Start adding your own!
Register with your work email and create a new case study profile for your business.
Related Case Studies.

Case Study
Remote Temperature Monitoring of Perishable Goods Saves Money
RMONI was facing temperature monitoring challenges in a cold chain business. A cold chain must be established and maintained to ensure goods have been properly refrigerated during every step of the process, making temperature monitoring a critical business function. Manual registration practice can be very costly, labor intensive and prone to mistakes.

Case Study
System 800xA at Indian Cement Plants
Chettinad Cement recognized that further efficiencies could be achieved in its cement manufacturing process. It looked to investing in comprehensive operational and control technologies to manage and derive productivity and energy efficiency gains from the assets on Line 2, their second plant in India.
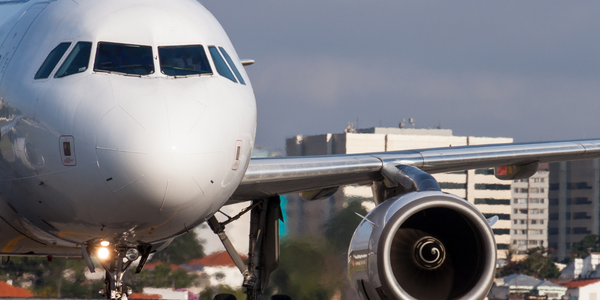
Case Study
Airbus Soars with Wearable Technology
Building an Airbus aircraft involves complex manufacturing processes consisting of thousands of moving parts. Speed and accuracy are critical to business and competitive advantage. Improvements in both would have high impact on Airbus’ bottom line. Airbus wanted to help operators reduce the complexity of assembling cabin seats and decrease the time required to complete this task.
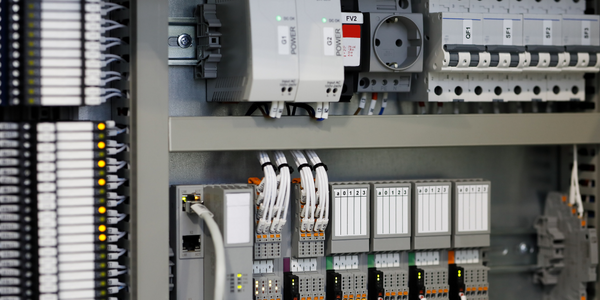
Case Study
Improving Production Line Efficiency with Ethernet Micro RTU Controller
Moxa was asked to provide a connectivity solution for one of the world's leading cosmetics companies. This multinational corporation, with retail presence in 130 countries, 23 global braches, and over 66,000 employees, sought to improve the efficiency of their production process by migrating from manual monitoring to an automatic productivity monitoring system. The production line was being monitored by ABB Real-TPI, a factory information system that offers data collection and analysis to improve plant efficiency. Due to software limitations, the customer needed an OPC server and a corresponding I/O solution to collect data from additional sensor devices for the Real-TPI system. The goal is to enable the factory information system to more thoroughly collect data from every corner of the production line. This will improve its ability to measure Overall Equipment Effectiveness (OEE) and translate into increased production efficiencies. System Requirements • Instant status updates while still consuming minimal bandwidth to relieve strain on limited factory networks • Interoperable with ABB Real-TPI • Small form factor appropriate for deployment where space is scarce • Remote software management and configuration to simplify operations