Technology Category
- Functional Applications - Fleet Management Systems (FMS)
- Robots - Autonomous Guided Vehicles (AGV)
Applicable Industries
- Automotive
- Electronics
Use Cases
- Autonomous Transport Systems
- Transportation Simulation
About The Customer
The customers of this service are the residents of Grand Rapids, Michigan, who need a flexible and convenient mode of public transportation. The service is particularly beneficial for those who live or work in the downtown area and the Westside neighborhoods. Many riders use the service to facilitate trips to other forms of transit at Amtrak’s Vernon J. Ehlers Station and Rapid Central Station, the city’s primary hub for bus travel. Other popular destinations include restaurants, shops, and offices throughout the city. The service is also accessible to wheelchair users, making it inclusive and accessible to all.
The Challenge
The city of Grand Rapids, Michigan, was facing a challenge with its public transit system. The existing system was based on a fixed route autonomous shuttle following the City’s Downtown Area Shuttle West Route. This system was restrictive as it only allowed passengers to travel to a fixed set and sequence of stops. The city was looking for a solution that would allow passengers to travel anywhere they wish at any time, providing a more flexible and convenient mode of transportation. The challenge was to transition from a fixed route system to an entirely on-demand service, while also integrating autonomous vehicle technology.
The Solution
In July 2021, the city of Grand Rapids launched an on-demand autonomous microtransit service, AVGR, in partnership with Via, May Mobility, and Gentex Corporation. The service was composed of five May Mobility vehicles, including one wheelchair-accessible vehicle. Passengers could book free trips across downtown Grand Rapids, Monday through Friday, from 7am to 7pm, using Via’s white-labeled rider app. Once a trip was booked, the app directed riders to a convenient nearby pickup point to meet their shared ride. Via’s platform powered the routing and fleet assignment. The service zone was expanded from 1 square mile to 4.2 square miles. AVGR vehicles were equipped with technology to enhance the customer experience, including Via’s in-vehicle screens for boarding confirmation and real-time trip information, and sensing pods for tracking lost objects, monitoring passenger safety, and maintaining vehicle cleanliness.
Operational Impact
Quantitative Benefit
Case Study missing?
Start adding your own!
Register with your work email and create a new case study profile for your business.
Related Case Studies.

Case Study
Remote Temperature Monitoring of Perishable Goods Saves Money
RMONI was facing temperature monitoring challenges in a cold chain business. A cold chain must be established and maintained to ensure goods have been properly refrigerated during every step of the process, making temperature monitoring a critical business function. Manual registration practice can be very costly, labor intensive and prone to mistakes.
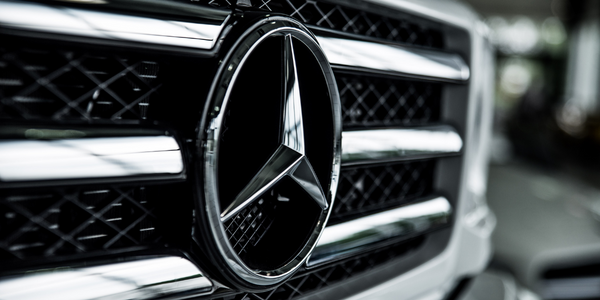
Case Study
Integral Plant Maintenance
Mercedes-Benz and his partner GAZ chose Siemens to be its maintenance partner at a new engine plant in Yaroslavl, Russia. The new plant offers a capacity to manufacture diesel engines for the Russian market, for locally produced Sprinter Classic. In addition to engines for the local market, the Yaroslavl plant will also produce spare parts. Mercedes-Benz Russia and his partner needed a service partner in order to ensure the operation of these lines in a maintenance partnership arrangement. The challenges included coordinating the entire maintenance management operation, in particular inspections, corrective and predictive maintenance activities, and the optimizing spare parts management. Siemens developed a customized maintenance solution that includes all electronic and mechanical maintenance activities (Integral Plant Maintenance).