Customer Company Size
SME
Region
- Europe
Country
- Italy
Product
- EcoStruxure for Food & Beverage
- Modicon M340 PLCs
- Harmony HMIs
- Altivar variable speed drives
- Modicon MCM safety controllers
Tech Stack
- Ethernet network
- Vijeo Designer graphic interface
- EcoStruxure Machine SCADA Expert
- EcoStruxure Machine Advisor
Implementation Scale
- Enterprise-wide Deployment
Impact Metrics
- Productivity Improvements
- Brand Awareness
- Customer Satisfaction
- Innovation Output
- Waste Reduction
Technology Category
- Functional Applications - Inventory Management Systems
- Functional Applications - Manufacturing Execution Systems (MES)
Applicable Industries
- Food & Beverage
Applicable Functions
- Discrete Manufacturing
- Quality Assurance
- Warehouse & Inventory Management
Use Cases
- Inventory Management
- Predictive Maintenance
- Condition Monitoring
Services
- System Integration
- Software Design & Engineering Services
About The Customer
For three generations, Mulino Marino has been a family-run business. It was founded in 1956 when Felice Marino purchased a small flour mill equipped for natural stone and roller grinding. The mill originally consisted of three water-powered millstones. In the ensuing years, it continued to evolve, increasingly taking the organic path and adding the processing of a myriad of specialty grains, cereals, and seeds such as spelt, rye, rice, and buckwheat, all of which require different grinding styles. Today, the company is certified 100% organic (EU regulation 2092/91), with a fully Italian supply chain and a highly automated production process while still paying careful attention to the preservation of traditions and the quality of its products.
The Challenge
Mulino Marino, a family-run mill in northern Italy, recognized the need to increase its production to keep up with growing demand. The changes in consumer tastes and purchasing behavior in recent decades presented new challenges: How to be more attentive to market demands for more sustainability, traceability, and organics, as well as to increased requests for alternative multigrain and multi-seed flours, which required the development of new recipes, processes, and products. These challenges, coupled with a dearth of experience and expertise amongst the younger generation of workers, highlighted the need to incorporate new technologies. The company’s strong sustainability ethos and its concern for a depleted earth also drove it to invest in energy management solutions such as solar panels, with the rest of its energy requirements coming from other renewable sources.
The Solution
Mulino Marino turned to Euro Beta, Schneider Electric’s Alliance system integrator partner, to help it achieve its goals. Euro Beta has deployed a range of EcoStruxure for Food & Beverage solutions. A network of Modicon M340 PLCs with Harmony HMIs, Altivar variable speed drives, and Modicon MCM safety controllers are all interconnected on an Ethernet network. The various areas that make up the mill (wheat storage, sack packaging, flour mills, rolling mills, grain mixing, etc) have been automated so that each can be managed independently and/or centralized on the console. The recipe process for the various flours, for example, can now be managed automatically by setting the parameters from the operator HMI panels that use a Vijeo Designer graphic interface. And there is still more in the works, including the installation of EcoStruxure Machine SCADA Expert on the central PC console to improve data management from the various systems and, potentially, from SQL databases, new building solutions for the showroom, as well as the implementation of EcoStruxure Machine Advisor for production monitoring.
Operational Impact
Case Study missing?
Start adding your own!
Register with your work email and create a new case study profile for your business.
Related Case Studies.

Case Study
The Kellogg Company
Kellogg keeps a close eye on its trade spend, analyzing large volumes of data and running complex simulations to predict which promotional activities will be the most effective. Kellogg needed to decrease the trade spend but its traditional relational database on premises could not keep up with the pace of demand.

Case Study
HEINEKEN Uses the Cloud to Reach 10.5 Million Consumers
For 2012 campaign, the Bond promotion, it planned to launch the campaign at the same time everywhere on the planet. That created unprecedented challenges for HEINEKEN—nowhere more so than in its technology operation. The primary digital content for the campaign was a 100-megabyte movie that had to play flawlessly for millions of viewers worldwide. After all, Bond never fails. No one was going to tolerate a technology failure that might bruise his brand.Previously, HEINEKEN had supported digital media at its outsourced datacenter. But that datacenter lacked the computing resources HEINEKEN needed, and building them—especially to support peak traffic that would total millions of simultaneous hits—would have been both time-consuming and expensive. Nor would it have provided the geographic reach that HEINEKEN needed to minimize latency worldwide.

Case Study
Energy Management System at Sugar Industry
The company wanted to use the information from the system to claim under the renewable energy certificate scheme. The benefit to the company under the renewable energy certificates is Rs 75 million a year. To enable the above, an end-to-end solution for load monitoring, consumption monitoring, online data monitoring, automatic meter data acquisition which can be exported to SAP and other applications is required.

Case Study
Coca Cola Swaziland Conco Case Study
Coco Cola Swaziland, South Africa would like to find a solution that would enable the following results: - Reduce energy consumption by 20% in one year. - Formulate a series of strategic initiatives that would enlist the commitment of corporate management and create employee awareness while helping meet departmental targets and investing in tools that assist with energy management. - Formulate a series of tactical initiatives that would optimize energy usage on the shop floor. These would include charging forklifts and running cold rooms only during off-peak periods, running the dust extractors only during working hours and basing lights and air-conditioning on someone’s presence. - Increase visibility into the factory and other processes. - Enable limited, non-intrusive control functions for certain processes.

Case Study
Temperature Monitoring for Restaurant Food Storage
When it came to implementing a solution, Mr. Nesbitt had an idea of what functionality that he wanted. Although not mandated by Health Canada, Mr. Nesbitt wanted to ensure quality control issues met the highest possible standards as part of his commitment to top-of-class food services. This wish list included an easy-to use temperature-monitoring system that could provide a visible display of the temperatures of all of his refrigerators and freezers, including historical information so that he could review the performance of his equipment. It also had to provide alert notification (but email alerts and SMS text message alerts) to alert key staff in the event that a cooling system was exceeding pre-set warning limits.
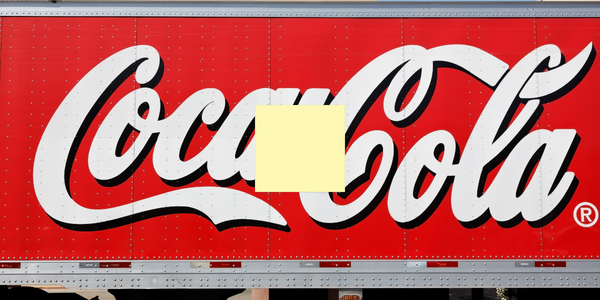
Case Study
Coca-Cola Refreshments, U.S.
Coca-Cola Refreshments owns and manages Coca-Cola branded refrigerators in retail establishments. Legacy systems were used to locate equipment information by logging onto multiple servers which took up to 8 hours to update information on 30-40 units. The company had no overall visibility into equipment status or maintenance history.