Customer Company Size
Large Corporate
Region
- Europe
Country
- Finland
Product
- Tikkurila Paints
Tech Stack
- Sphera’s Product Compliance Software
- Sphera’s Chemical Management System
Implementation Scale
- Enterprise-wide Deployment
Impact Metrics
- Productivity Improvements
- Cost Savings
Technology Category
- Functional Applications - Enterprise Resource Planning Systems (ERP)
Applicable Industries
- Chemicals
Applicable Functions
- Quality Assurance
- Product Research & Development
Use Cases
- Regulatory Compliance Monitoring
Services
- System Integration
- Software Design & Engineering Services
About The Customer
Tikkurila is a paint manufacturing company that was founded in 1862. The company is headquartered in Finland and distributes its products to 40 countries. In 2020, Tikkurila generated a revenue of €582 million and employed 2,400 people. For more than 150 years, Tikkurila has provided consumers and professionals with user-friendly, sustainable paint solutions for surface protection and decoration. The company prides itself on product safety and quality, which are among the cornerstones of its operations. From family homes to unique business environments like hospitals, Tikkurila product labeling must meet customer needs and expectations as well as regulatory requirements.
The Challenge
Tikkurila, a paint manufacturing company, has been providing consumers and professionals with user-friendly, sustainable paint solutions for over 150 years. The company prides itself on product safety and quality, which are among the cornerstones of its operations. Tikkurila's product labeling must meet customer needs and expectations as well as regulatory requirements. The company works hard to systematically determine the health, safety, and environmental impact of the raw materials used in its paints. Product teams must develop material safety data sheets (SDS) and labels in up to 15 languages as it markets more than 2,000 products. However, Tikkurila’s facilities across 11 countries used different methods to create safety data sheets and labels, including outsourcing for translation. They realized that they needed a more efficient way to create their SDSs if they were going to continue to grow.
The Solution
Tikkurila has integrated Sphera’s Product Compliance solution with its formula management system, so materials information flows seamlessly across platforms. The company also uses Sphera’s Chemical Management system to archive safety documents widely and make them available online throughout the company. By using the same system to generate safety data sheets and product labels across multiple locations, Tikkurila’s product safety teams are helping drive operational efficiency. The sites now have greater flexibility because their product safety teams can now generate standardized, best-in-class SDSs and labels in multiple languages. For example, employees in Finland can now confidently produce safety documents in Polish, Swedish, and other languages using the Sphera solution. As a result, these four Tikkurila sites will reduce costs and expedite completion of SDSs by eliminating the need for external translators.
Operational Impact
Quantitative Benefit
Case Study missing?
Start adding your own!
Register with your work email and create a new case study profile for your business.
Related Case Studies.
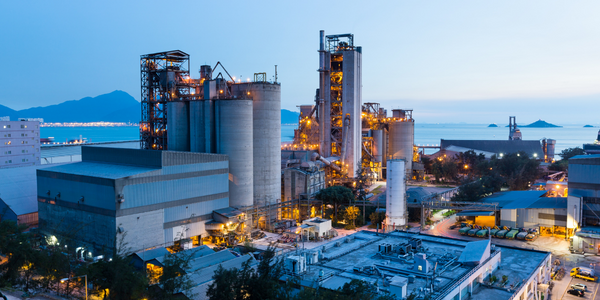
Case Study
Honeywell - Tata Chemicals Improves Data Accessibility with OneWireless
Tata was facing data accessibility challenges in the cement plant control room tapping signals from remote process control areas and other distant locations, including the gas scrubber. Tata needed a wireless solution to extend its control network securely to remote locations that would also provide seamless communication with existing control applications.

Case Study
Advanced Elastomer Systems Upgrades Production
In order to maintain its share of the international market for thermoplastic elastomers AES recently expanded its Florida plant by adding a new production line. While the existing lines were operating satisfactorily using a PROVOX distributed control system with traditional analog I/O, AES wanted advanced technology on the new line for greater economy, efficiency, and reliability. AES officials were anxious to get this line into production to meet incoming orders, but two hurricanes slowed construction.
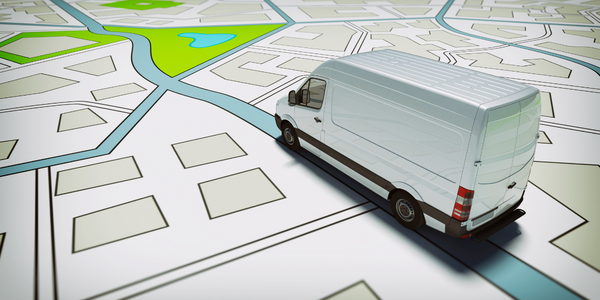
Case Study
Wireless GPS Tracking & Security Monitoring
Enhancing the security of hazardous freight and ensuring compliance with Homeland Security’s Transportation Security Administration mandate that all trains carrying chemicals capable of creating a toxic inhalation condition are equipped with on-board safety monitoring systems.
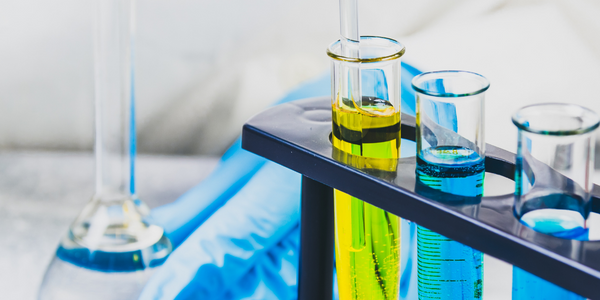
Case Study
Field Device Asset Management For Chemical Company in China
Chinese chemical subsidiary of multinational corporation serves customers throughout the world. Sales offices and research and technology centers are strategically located to provide rapid response to customer requests. Just two workers were assigned to maintain thousands of intelligent instruments in three production units, so they could do little more than react to device issues as they appeared. This costly maintenance method inevitably led to unexpected downtime when a critical instrument failed. Plant management recognized the need to change from reactive to predictive maintenance for all assets, including instruments and control valves, but help was needed in implementing such a technology-based initiative.
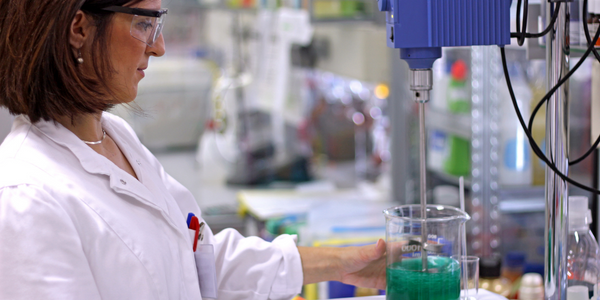
Case Study
Industrial Workforce Mobility for Improved Safety & Operations
Huntsman Corporation, a global manufacturer and marketer of differentiated chemicals, undertook an aggressive program to eliminate injuries, product defects, and environmental releases at their Port Neches facility. Termed “Project Zero”, this program required a completely mobile solution to empower operations and maintenance personnel to capture defects, track work progress and make process and safety related decisions in real-time.