Technology Category
- Sensors - Chemical Sensors
- Sensors - Liquid Detection Sensors
Applicable Industries
- Chemicals
- Plastics
Use Cases
- Personnel Tracking & Monitoring
- Remote Surgery
About The Customer
The Plastic Surgeon is a fine finishing cosmetic repair company based in the UK. The company employs over 250 staff members who operate throughout the UK. The Plastic Surgeon serves thousands of clients across a range of sectors. Health and safety are high on the company's list of priorities, forming part of their strategic plan. The company uses a significant number of chemical products in their operations, including high-risk substances like fillers, adhesives, and solvent-based paints.
The Challenge
The Plastic Surgeon, a UK-based cosmetic repair company, faced a significant challenge in managing the safety of their large team spread across the UK. The company uses a wide range of chemical products, including high-risk substances like fillers, adhesives, and solvent-based paints. Ensuring the safety of their staff from these hazardous substances was a top priority, but the company found it difficult to control these substances and understand their contents. This knowledge was crucial to provide the right protection for their staff. The challenge was not only to manage the hazardous substances but also to effectively communicate the correct protection measures to the staff working on site.
The Solution
The Plastic Surgeon turned to Sypol's CMS to manage the hazardous substances they use in their operations. Sypol's CMS provides access to thousands of COSHH assessments, which are essential for the everyday running of their business. These assessments help the company determine the right protection measures for their staff. In addition to the CMS, The Plastic Surgeon also benefits from the advice and guidance provided by the Sypol helpdesk team. This support is invaluable for the company to effectively communicate the correct protection needed when working on site. By leveraging Sypol's CMS and helpdesk support, The Plastic Surgeon can ensure the safety of their staff and maintain compliance with health and safety regulations.
Operational Impact
Case Study missing?
Start adding your own!
Register with your work email and create a new case study profile for your business.
Related Case Studies.

Case Study
Plastic Spoons Case study: Injection Moulding
In order to meet customer expectations by supplying a wide variety of packaging units, from 36 to 1000 spoons per package, a new production and packaging line needed to be built. DeSter wanted to achieve higher production capacity, lower cycle time and a high degree of operator friendliness with this new production line.
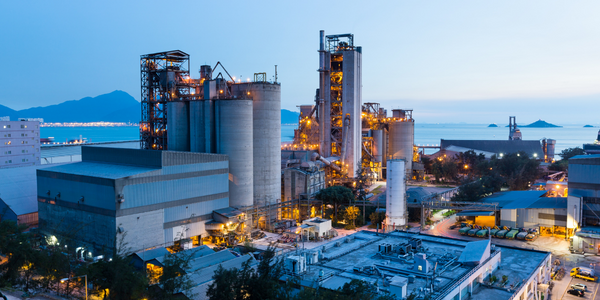
Case Study
Honeywell - Tata Chemicals Improves Data Accessibility with OneWireless
Tata was facing data accessibility challenges in the cement plant control room tapping signals from remote process control areas and other distant locations, including the gas scrubber. Tata needed a wireless solution to extend its control network securely to remote locations that would also provide seamless communication with existing control applications.

Case Study
Advanced Elastomer Systems Upgrades Production
In order to maintain its share of the international market for thermoplastic elastomers AES recently expanded its Florida plant by adding a new production line. While the existing lines were operating satisfactorily using a PROVOX distributed control system with traditional analog I/O, AES wanted advanced technology on the new line for greater economy, efficiency, and reliability. AES officials were anxious to get this line into production to meet incoming orders, but two hurricanes slowed construction.
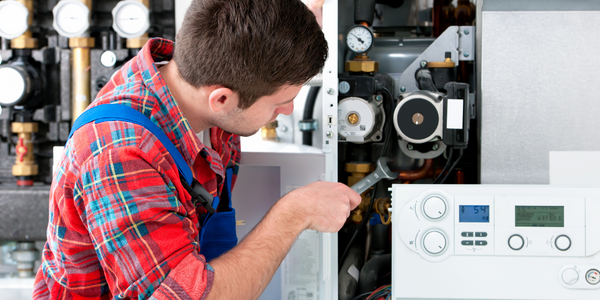
Case Study
Boiler Control System for Plastic Manufacturing Applications
Factory automation applications must be equipped to handle and monitor the myriads of information from attached devices. For plastic manufacturing applications, the boiler control system plays a critical role by gathering and regulating information to ensure production is accurate and smooth. In this particular case, the customer combines eight subsystems that include power meters, water meters, alarm output, displays, and I/O status to be controlled by several intelligent controllers with Modbus RTU interface. The Modbus TCP protocol is used for this application due to the distance. System Requirements: • Modbus serial to Modbus TCP translation • Multiple slaves/masters support • Automatic Modbus TCP response time detection
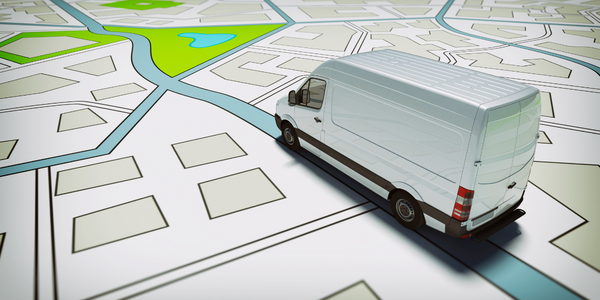
Case Study
Wireless GPS Tracking & Security Monitoring
Enhancing the security of hazardous freight and ensuring compliance with Homeland Security’s Transportation Security Administration mandate that all trains carrying chemicals capable of creating a toxic inhalation condition are equipped with on-board safety monitoring systems.