Company Size
1,000+
Region
- America
Country
- United States
Product
- JDA Demand Manager
- JDA Enterprise Architecture
- JDA Inventory Optimization
- JDA Supply Chain Planner
- JDA Factory Planner
Tech Stack
- Advanced Planning Systems
Implementation Scale
- Enterprise-wide Deployment
Impact Metrics
- Customer Satisfaction
- Productivity Improvements
Technology Category
- Functional Applications - Inventory Management Systems
- Functional Applications - Manufacturing Execution Systems (MES)
Applicable Industries
- Electronics
Applicable Functions
- Discrete Manufacturing
- Logistics & Transportation
Use Cases
- Inventory Management
- Supply Chain Visibility
About The Customer
SanDisk Corporation is a global leader in flash memory storage solutions. Its state-of-the-art solutions can be found in many of the world’s largest data centers, embedded in advanced smartphones, tablets, and PCs, and at hundreds of thousands of retail stores worldwide. As SanDisk’s business grew, the company needed to migrate from homegrown, spreadsheet-based planning tools to robust, scalable solutions that would support its expanding original equipment manufacturer (OEM) channels and retail presence.
The Challenge
SanDisk Corporation, a global leader in flash memory storage solutions, needed to increase its supply chain flexibility and responsiveness to customer demand. As the company's business grew, it needed to migrate from homegrown, spreadsheet-based planning tools to robust, scalable solutions that would support its expanding original equipment manufacturer (OEM) channels and retail presence. SanDisk sought an integrated advanced planning solution that would help the company maintain profitable growth and maximize its margins while continuing to meet customer demand and increase customer satisfaction.
The Solution
SanDisk selected JDA Software’s Manufacturing Planning solutions to enhance its planning processes. The company now produces a daily integrated supply chain plan that includes demand, material supply and capacity constraints and utilization, allocation, and execution objectives. The end-to-end supply chain plan is seamlessly integrated and funnels supply plan information from the long-range materials and capacity plan to the daily production plan. This is incorporated with the demand plan, which includes a single version of the forecast that aligns with business unit, sales and finance goals. This single forecast is incorporated into the weekly and monthly planning cycles. With the integrated business plan, SanDisk now has visibility into demand and supply across the entire organization.
Operational Impact
Quantitative Benefit
Case Study missing?
Start adding your own!
Register with your work email and create a new case study profile for your business.
Related Case Studies.

Case Study
Remote Temperature Monitoring of Perishable Goods Saves Money
RMONI was facing temperature monitoring challenges in a cold chain business. A cold chain must be established and maintained to ensure goods have been properly refrigerated during every step of the process, making temperature monitoring a critical business function. Manual registration practice can be very costly, labor intensive and prone to mistakes.
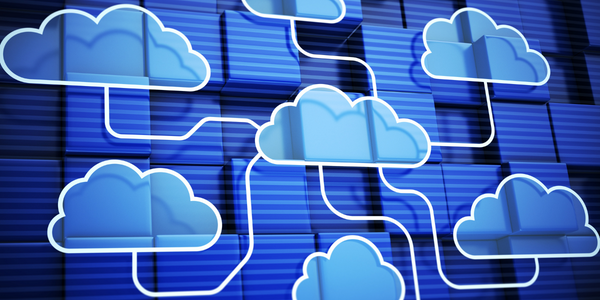
Case Study
Cloud Solution for Energy Management Platform-Schneider Electric
Schneider Electric required a cloud solution for its energy management platform to manage high computational operations, which were essential for catering to client requirements. As the business involves storage and analysis of huge amounts of data, the company also needed a convenient and scalable storage solution to facilitate operations efficiently.
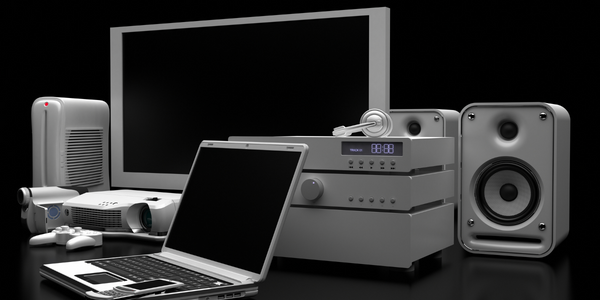
Case Study
Leveraging the IoT to Gain a Competitive Edge in International Competition
Many large manufacturers in and outside Japan are competing for larger market share in the same space, expecting a growing demand for projectors in the areas of entertainment, which requires glamor and strong visual performance as well as digital signage that can attract people’s attention. “It is becoming more and more difficult to differentiate ourselves with stand-alone hardware products,” says Kazuyuki Kitagawa, Director of Service & Support at Panasonic AVC Networks. “In order for Panasonic to grow market share and overall business, it is essential for us to develop solutions that deliver significant added value.” Panasonic believes projection failure and quality deterioration should never happen. This is what and has driven them to make their projectors IoT-enabled. More specifically, Panasonic has developed a system that collects data from projectors, visualizes detailed operational statuses, and predicts issues and address them before failure occurs. Their projectors are embedded with a variety of sensors that measure power supply, voltage, video input/ output signals, intake/exhaust air temperatures, cooling fan operations, and light bulb operating time. These sensors have been used to make the projector more intelligent, automatically suspending operation when the temperature rises excessively, and automatically switching light bulbs. Although this was a great first step, Panasonic projectors were still not equipped with any capability to send the data over a network.