Customer Company Size
SME
Region
- Europe
- Africa
- America
- Asia
- Pacific
Country
- Germany
Product
- Symestic MES platform
- Symestic IoT box
- EMnify global SIM
- EMnify Web Portal
- EMnify OpenVPN
Tech Stack
- Cloud-based MES
- IoT communication
- Edge computing
- Data visualization
- Risk evaluation
Implementation Scale
- Enterprise-wide Deployment
Impact Metrics
- Productivity Improvements
- Cost Savings
- Waste Reduction
Technology Category
- Application Infrastructure & Middleware - Data Visualization
- Functional Applications - Manufacturing Execution Systems (MES)
- Networks & Connectivity - Cellular
- Platform as a Service (PaaS) - Device Management Platforms
- Processors & Edge Intelligence - Embedded & Edge Computers
Applicable Functions
- Discrete Manufacturing
- Quality Assurance
Use Cases
- Manufacturing System Automation
- Edge Computing & Edge Intelligence
- Predictive Maintenance
Services
- Cloud Planning, Design & Implementation Services
- System Integration
About The Customer
Symestic is a German company that was founded in 1999. The company aims to help global manufacturers increase operational efficiency with a cloud-based Manufacturing Execution System (MES) platform that is affordable, scalable, and easy to implement. Symestic's MES solution allows companies to capture and analyze vital production metrics and process data, then derive informed decisions to optimize shop floor activities. The company's IoT box, embedded with edge computing capabilities, can pre-process data and only communicate relevant events to the cloud for analysis. Symestic's MES platform provides a powerful toolset for data visualization, risk evaluation, issue detection, and production reporting. The pay-per-use SaaS model helps to break down adoption barriers often seen in traditional MES systems.
The Challenge
Symestic, a German company founded in 1999, aims to help global manufacturers increase operational efficiency with a cloud-based Manufacturing Execution System (MES) platform that is affordable, scalable, and easy to implement. However, to transmit machine data from their IoT edge gateways (known as Symestic IoT boxes) to the MES application, the company needed an IoT communication solution that goes beyond a normal SIM card. They required a solution that would provide full transparency and control to provide a robust MES solution to worldwide production plants, including those of large German manufacturers like BITO, Brita, and Erlenbacher.
The Solution
Symestic partnered with EMnify to use their global SIM and platform for IoT communication. The EMnify solution does not depend on a local carrier, so Symestic does not have to talk to multiple operators. Using the EMnify global SIM, Symestic can rest assured that their IoT boxes are always using the best cellular network available. EMnify's management portal provides real-time insights into the device connection status, allowing Symestic’s operations team to monitor existing data consumption and the remaining allowance to ensure customers have uninterrupted data communication. Additionally, EMnify’s OpenVPN lets the team remotely log into the IoT boxes for troubleshooting without having to dispatch technicians to the site.
Operational Impact
Quantitative Benefit
Case Study missing?
Start adding your own!
Register with your work email and create a new case study profile for your business.
Related Case Studies.

Case Study
Remote Monitoring & Predictive Maintenance App for a Solar Energy System
The maintenance & tracking of various modules was an overhead for the customer due to the huge labor costs involved. Being an advanced solar solutions provider, they wanted to ensure early detection of issues and provide the best-in-class customer experience. Hence they wanted to automate the whole process.
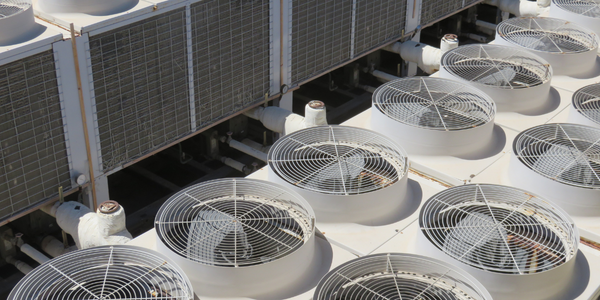
Case Study
Predictive Maintenance for Industrial Chillers
For global leaders in the industrial chiller manufacturing, reliability of the entire production process is of the utmost importance. Chillers are refrigeration systems that produce ice water to provide cooling for a process or industrial application. One of those leaders sought a way to respond to asset performance issues, even before they occur. The intelligence to guarantee maximum reliability of cooling devices is embedded (pre-alarming). A pre-alarming phase means that the cooling device still works, but symptoms may appear, telling manufacturers that a failure is likely to occur in the near future. Chillers who are not internet connected at that moment, provide little insight in this pre-alarming phase.

Case Study
Plastic Spoons Case study: Injection Moulding
In order to meet customer expectations by supplying a wide variety of packaging units, from 36 to 1000 spoons per package, a new production and packaging line needed to be built. DeSter wanted to achieve higher production capacity, lower cycle time and a high degree of operator friendliness with this new production line.
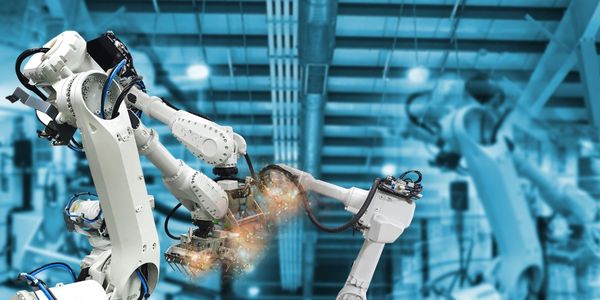
Case Study
Robot Saves Money and Time for US Custom Molding Company
Injection Technology (Itech) is a custom molder for a variety of clients that require precision plastic parts for such products as electric meter covers, dental appliance cases and spools. With 95 employees operating 23 molding machines in a 30,000 square foot plant, Itech wanted to reduce man hours and increase efficiency.
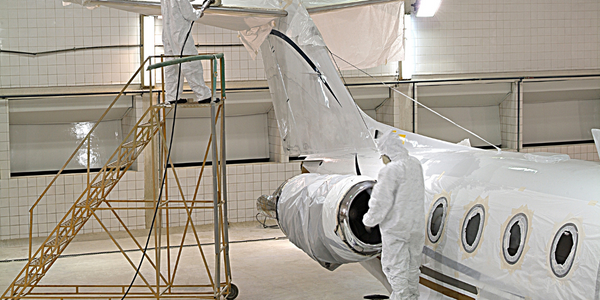
Case Study
Aircraft Predictive Maintenance and Workflow Optimization
First, aircraft manufacturer have trouble monitoring the health of aircraft systems with health prognostics and deliver predictive maintenance insights. Second, aircraft manufacturer wants a solution that can provide an in-context advisory and align job assignments to match technician experience and expertise.
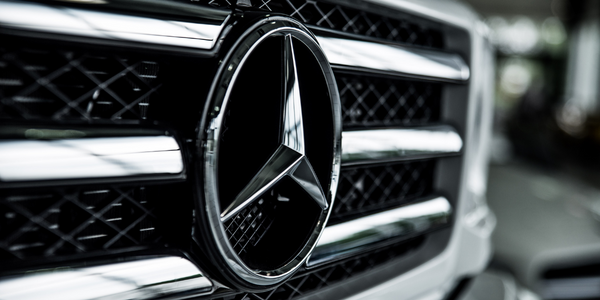
Case Study
Integral Plant Maintenance
Mercedes-Benz and his partner GAZ chose Siemens to be its maintenance partner at a new engine plant in Yaroslavl, Russia. The new plant offers a capacity to manufacture diesel engines for the Russian market, for locally produced Sprinter Classic. In addition to engines for the local market, the Yaroslavl plant will also produce spare parts. Mercedes-Benz Russia and his partner needed a service partner in order to ensure the operation of these lines in a maintenance partnership arrangement. The challenges included coordinating the entire maintenance management operation, in particular inspections, corrective and predictive maintenance activities, and the optimizing spare parts management. Siemens developed a customized maintenance solution that includes all electronic and mechanical maintenance activities (Integral Plant Maintenance).