Swizzels Matlow Optimises Supply Chain Performance
Customer Company Size
Large Corporate
Region
- Europe
Country
- United Kingdom
Product
- Manhattan SCALE™
- Zetes Radio Frequency Picking Technology
Tech Stack
- Warehouse Management System (WMS)
- Radio Frequency Picking Technology
Implementation Scale
- Enterprise-wide Deployment
Impact Metrics
- Customer Satisfaction
- Productivity Improvements
- Digital Expertise
Technology Category
- Functional Applications - Warehouse Management Systems (WMS)
Applicable Industries
- Food & Beverage
Applicable Functions
- Warehouse & Inventory Management
- Logistics & Transportation
Use Cases
- Inventory Management
- Warehouse Automation
- Supply Chain Visibility
Services
- System Integration
- Training
About The Customer
Swizzels Matlow, a family-owned business, has a rich history dating back to 1928 when Alfred and Maurice Matlow started Matlow Bros. Ltd. The company, known for its popular sweets like Love Hearts, Drumstick, and New Refreshers, employs over 500 people. Its distribution center in Adlington, Cheshire, processes over 1,000 pallets of stock per week. The company has grown significantly over the years, driven by increasing customer demand. However, the existing paper-based system for managing stock location within the distribution center was becoming a bottleneck, necessitating an upgrade to a more advanced warehouse management system.
The Challenge
Swizzels Matlow faced significant challenges with their existing paper-based warehouse management system. The manual system required staff to re-enter information into a computer, leading to mistakes and duplication of effort. The growing business, driven by increased customer demand, needed a more efficient and reliable system to manage stock location and improve operational efficiency. The lack of real-time visibility and the potential for errors in re-keying information were major concerns, impacting customer service levels and overall business performance.
The Solution
Swizzels Matlow selected Manhattan SCALE™ as their new warehouse management system after a thorough review of the market. The Manhattan solution was chosen for its flexibility, reliability, and strong market reputation. The implementation included an expansion of the distribution center, increasing capacity by almost 10%, and the integration of radio frequency picking technology supplied by Zetes. The company involved staff from the beginning, with a Manhattan consultant on-site for three months before the go-live. Training was provided to three 'super-users' who then trained an additional 20 staff members. The transition to the new system was smooth, with the company back to full capacity within two days of going live.
Operational Impact
Quantitative Benefit
Case Study missing?
Start adding your own!
Register with your work email and create a new case study profile for your business.
Related Case Studies.

Case Study
The Kellogg Company
Kellogg keeps a close eye on its trade spend, analyzing large volumes of data and running complex simulations to predict which promotional activities will be the most effective. Kellogg needed to decrease the trade spend but its traditional relational database on premises could not keep up with the pace of demand.

Case Study
HEINEKEN Uses the Cloud to Reach 10.5 Million Consumers
For 2012 campaign, the Bond promotion, it planned to launch the campaign at the same time everywhere on the planet. That created unprecedented challenges for HEINEKEN—nowhere more so than in its technology operation. The primary digital content for the campaign was a 100-megabyte movie that had to play flawlessly for millions of viewers worldwide. After all, Bond never fails. No one was going to tolerate a technology failure that might bruise his brand.Previously, HEINEKEN had supported digital media at its outsourced datacenter. But that datacenter lacked the computing resources HEINEKEN needed, and building them—especially to support peak traffic that would total millions of simultaneous hits—would have been both time-consuming and expensive. Nor would it have provided the geographic reach that HEINEKEN needed to minimize latency worldwide.

Case Study
Energy Management System at Sugar Industry
The company wanted to use the information from the system to claim under the renewable energy certificate scheme. The benefit to the company under the renewable energy certificates is Rs 75 million a year. To enable the above, an end-to-end solution for load monitoring, consumption monitoring, online data monitoring, automatic meter data acquisition which can be exported to SAP and other applications is required.

Case Study
Coca Cola Swaziland Conco Case Study
Coco Cola Swaziland, South Africa would like to find a solution that would enable the following results: - Reduce energy consumption by 20% in one year. - Formulate a series of strategic initiatives that would enlist the commitment of corporate management and create employee awareness while helping meet departmental targets and investing in tools that assist with energy management. - Formulate a series of tactical initiatives that would optimize energy usage on the shop floor. These would include charging forklifts and running cold rooms only during off-peak periods, running the dust extractors only during working hours and basing lights and air-conditioning on someone’s presence. - Increase visibility into the factory and other processes. - Enable limited, non-intrusive control functions for certain processes.

Case Study
Temperature Monitoring for Restaurant Food Storage
When it came to implementing a solution, Mr. Nesbitt had an idea of what functionality that he wanted. Although not mandated by Health Canada, Mr. Nesbitt wanted to ensure quality control issues met the highest possible standards as part of his commitment to top-of-class food services. This wish list included an easy-to use temperature-monitoring system that could provide a visible display of the temperatures of all of his refrigerators and freezers, including historical information so that he could review the performance of his equipment. It also had to provide alert notification (but email alerts and SMS text message alerts) to alert key staff in the event that a cooling system was exceeding pre-set warning limits.
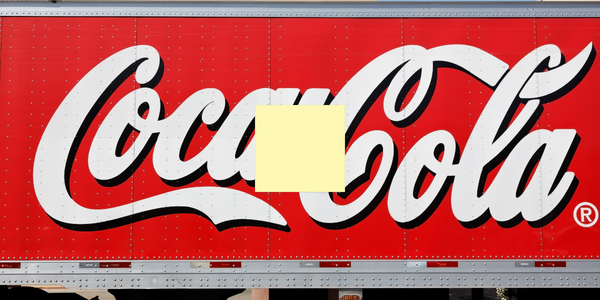
Case Study
Coca-Cola Refreshments, U.S.
Coca-Cola Refreshments owns and manages Coca-Cola branded refrigerators in retail establishments. Legacy systems were used to locate equipment information by logging onto multiple servers which took up to 8 hours to update information on 30-40 units. The company had no overall visibility into equipment status or maintenance history.