Technology Category
- Networks & Connectivity - 5G
- Platform as a Service (PaaS) - Application Development Platforms
Applicable Industries
- Agriculture
- Equipment & Machinery
Applicable Functions
- Maintenance
- Quality Assurance
Use Cases
- Personnel Tracking & Monitoring
- Time Sensitive Networking
Services
- Testing & Certification
- Training
About The Customer
Bunge is a global leader in the food and agriculture industry. The company has over 23,000 dedicated associates, more than 300 diverse facilities, and a presence in over 40 countries. Bunge is the world leader in oilseed processing and a leading producer and supplier of specialty plant-based oils, fats, and protein. The company is committed to improving operational efficiency, worker engagement, and communication across its facilities. Bunge's collaboration with Poka is part of its continuous improvement efforts to reduce unplanned downtime, streamline shift handovers, and maintain high operational standards.
The Challenge
Bunge, a global leader in the food and agriculture industry, was facing challenges in operational efficiency, worker engagement, and communication. With over 23,000 associates, 300+ facilities, and a presence in more than 40 countries, the company needed a solution to directly connect workers with standard operating procedures (SOPs) and facilitate communication. The primary goal was to reduce unplanned downtime, streamline shift handovers, and improve the quality of inspections. The company was also looking for a way to improve the mean time between failures (MTBF), which would lead to longer intervals between major equipment breakdowns. The challenge was to find a solution that could address these issues efficiently and effectively.
The Solution
Bunge turned to Poka's digital platform to address their operational challenges. They trialled four of Poka’s modules: Connected Worker Platform, Knowledge Hub, Skills Management, and Communication. The Connected Worker Platform and Knowledge Hub provided up-to-date SOPs/SWIs all in one place, while the Skills Management module offered a Skills Matrix for blended training. The Communication module facilitated easy reach to experts across shifts and departments. Bunge rolled out Poka on two production lines and within a few months, they experienced a significant reduction in unplanned downtime and an increase in MTBF. This was attributed to the operators' ability to address minor issues promptly, communicate them efficiently, and prevent them from escalating into larger problems. Poka also improved the quality of shift handovers and inspections by offering features that support form scheduling and quality, increasing completion rates.
Operational Impact
Quantitative Benefit
Case Study missing?
Start adding your own!
Register with your work email and create a new case study profile for your business.
Related Case Studies.

Case Study
Smart Water Filtration Systems
Before working with Ayla Networks, Ozner was already using cloud connectivity to identify and solve water-filtration system malfunctions as well as to monitor filter cartridges for replacements.But, in June 2015, Ozner executives talked with Ayla about how the company might further improve its water systems with IoT technology. They liked what they heard from Ayla, but the executives needed to be sure that Ayla’s Agile IoT Platform provided the security and reliability Ozner required.

Case Study
IoT enabled Fleet Management with MindSphere
In view of growing competition, Gämmerler had a strong need to remain competitive via process optimization, reliability and gentle handling of printed products, even at highest press speeds. In addition, a digitalization initiative also included developing a key differentiation via data-driven services offers.
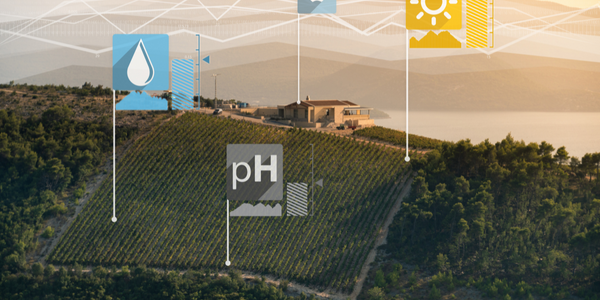
Case Study
Intelligent Farming with ThingWorx Analytics
Z Farms was facing three challenges: costly irrigation systems with water as a limited resource, narrow optimal ranges of soil moisture for growth with difficult maintenance and farm operators could not simply turn on irrigation systems like a faucet.
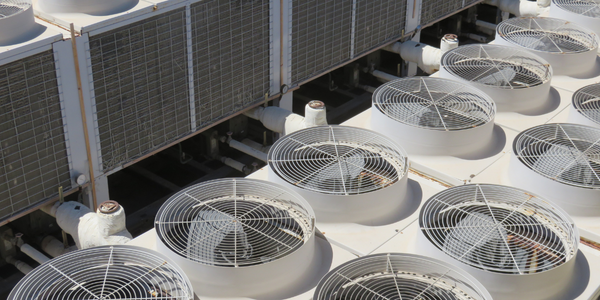
Case Study
Predictive Maintenance for Industrial Chillers
For global leaders in the industrial chiller manufacturing, reliability of the entire production process is of the utmost importance. Chillers are refrigeration systems that produce ice water to provide cooling for a process or industrial application. One of those leaders sought a way to respond to asset performance issues, even before they occur. The intelligence to guarantee maximum reliability of cooling devices is embedded (pre-alarming). A pre-alarming phase means that the cooling device still works, but symptoms may appear, telling manufacturers that a failure is likely to occur in the near future. Chillers who are not internet connected at that moment, provide little insight in this pre-alarming phase.

Case Study
Premium Appliance Producer Innovates with Internet of Everything
Sub-Zero faced the largest product launch in the company’s history:It wanted to launch 60 new products as scheduled while simultaneously opening a new “greenfield” production facility, yet still adhering to stringent quality requirements and manage issues from new supply-chain partners. A the same time, it wanted to increase staff productivity time and collaboration while reducing travel and costs.

Case Study
Integration of PLC with IoT for Bosch Rexroth
The application arises from the need to monitor and anticipate the problems of one or more machines managed by a PLC. These problems, often resulting from the accumulation over time of small discrepancies, require, when they occur, ex post technical operations maintenance.