Technology Category
- Analytics & Modeling - Digital Twin / Simulation
- Networks & Connectivity - Cellular
Applicable Industries
- Equipment & Machinery
- Telecommunications
Applicable Functions
- Product Research & Development
- Quality Assurance
Use Cases
- Digital Twin
- Virtual Prototyping & Product Testing
Services
- System Integration
- Testing & Certification
About The Customer
Motorola is a global communications leader that has transformed the ubiquitous cell phone into today’s universal remote control for life. The company revolutionizes broadband, embedded systems, and wireless networks. The company that pioneered the first portable two-way radio for the U.S. Army in 1943 now helps individuals reach the people, things, and information they need in their homes, cars, workplaces, and everywhere in between. Today’s cell phones developed by Motorola are incredibly complex, with multiple printed-circuit boards and large, multifunctional liquid crystal displays (LCDs). They also have the ability to support multiple data protocols such as code division multiple access (CDMA), global system for mobile communications (GSM) and Worldwide Interoperability for Microwave Access (WiMAX) – all in a single, sleek hand-held device.
The Challenge
Motorola, a global communications leader, is faced with the challenge of developing increasingly complex cell phones that support multiple data protocols and are built to withstand rugged use. The company is driven by shortened design cycles, increasing product complexity, and reduced profit margins. Design cycles that took 18 months in 1998 are now pushing toward a six-month goal to meet business-critical product launches and fixed ship dates. To maintain a healthy profit margin, Motorola must keep down the overall cost of producing the product. The company also needs to understand 'real-world' reliability well before next-generation cell phones hit the shelves. This requires capturing product-life behavior, predicting areas needing improvement, and generating high-quality products within a greatly reduced time frame.
The Solution
To address these challenges, Motorola has increased its use of computer-aided engineering (CAE) earlier in the design cycle. The company is using Altair HyperWorks for up-front simulation along with prototype testing to aid in the development process. This approach has enabled the company to capture product-life behavior, predict areas needing improvement, and generate high-quality products within a greatly reduced time frame. The use and customization of advanced CAE software have streamlined the mechanical prototype process while greatly increasing design robustness. Significantly decreasing simulation time has enabled Motorola engineers to identify and correct potential issues early in the development cycle. Reduction in simulation cycle time is also critical to shorten time to market, which, in turn, has a positive impact on the company’s bottom line.
Operational Impact
Quantitative Benefit
Case Study missing?
Start adding your own!
Register with your work email and create a new case study profile for your business.
Related Case Studies.

Case Study
Smart Water Filtration Systems
Before working with Ayla Networks, Ozner was already using cloud connectivity to identify and solve water-filtration system malfunctions as well as to monitor filter cartridges for replacements.But, in June 2015, Ozner executives talked with Ayla about how the company might further improve its water systems with IoT technology. They liked what they heard from Ayla, but the executives needed to be sure that Ayla’s Agile IoT Platform provided the security and reliability Ozner required.

Case Study
IoT enabled Fleet Management with MindSphere
In view of growing competition, Gämmerler had a strong need to remain competitive via process optimization, reliability and gentle handling of printed products, even at highest press speeds. In addition, a digitalization initiative also included developing a key differentiation via data-driven services offers.
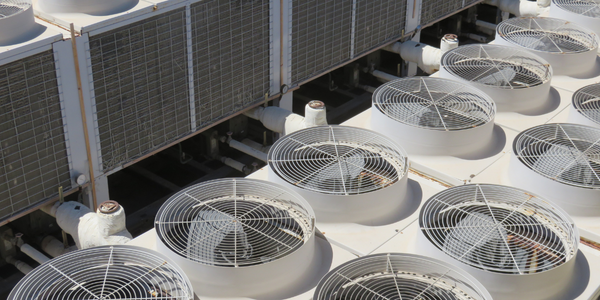
Case Study
Predictive Maintenance for Industrial Chillers
For global leaders in the industrial chiller manufacturing, reliability of the entire production process is of the utmost importance. Chillers are refrigeration systems that produce ice water to provide cooling for a process or industrial application. One of those leaders sought a way to respond to asset performance issues, even before they occur. The intelligence to guarantee maximum reliability of cooling devices is embedded (pre-alarming). A pre-alarming phase means that the cooling device still works, but symptoms may appear, telling manufacturers that a failure is likely to occur in the near future. Chillers who are not internet connected at that moment, provide little insight in this pre-alarming phase.

Case Study
Premium Appliance Producer Innovates with Internet of Everything
Sub-Zero faced the largest product launch in the company’s history:It wanted to launch 60 new products as scheduled while simultaneously opening a new “greenfield” production facility, yet still adhering to stringent quality requirements and manage issues from new supply-chain partners. A the same time, it wanted to increase staff productivity time and collaboration while reducing travel and costs.

Case Study
Integration of PLC with IoT for Bosch Rexroth
The application arises from the need to monitor and anticipate the problems of one or more machines managed by a PLC. These problems, often resulting from the accumulation over time of small discrepancies, require, when they occur, ex post technical operations maintenance.
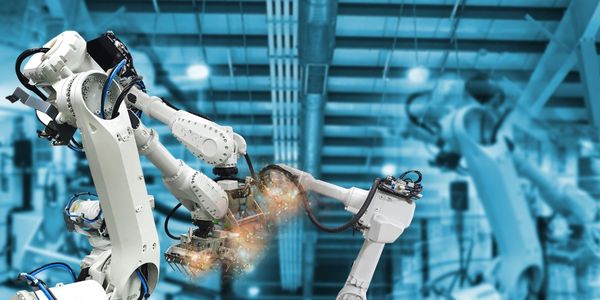
Case Study
Robot Saves Money and Time for US Custom Molding Company
Injection Technology (Itech) is a custom molder for a variety of clients that require precision plastic parts for such products as electric meter covers, dental appliance cases and spools. With 95 employees operating 23 molding machines in a 30,000 square foot plant, Itech wanted to reduce man hours and increase efficiency.