Company Size
11-200
Region
- America
Country
- United States
Product
- Sage 500 ERP
Tech Stack
- ERP System
Implementation Scale
- Enterprise-wide Deployment
Impact Metrics
- Cost Savings
- Productivity Improvements
Technology Category
- Functional Applications - Enterprise Resource Planning Systems (ERP)
Applicable Functions
- Discrete Manufacturing
Use Cases
- Inventory Management
- Manufacturing System Automation
Services
- System Integration
About The Customer
SpecPrint, Inc. is a family-owned company that has been in operation for almost 60 years. The company has cornered a unique niche market—manufacturing long-lasting adhesive labels. The decals that identify vacuum cleaners such as Kirbys come from SpecPrint. So do the labels on Murray lawnmowers, Champion oil filters, and numerous big-name household appliances. The company's high-quality silk-screened decals go on everything from tiny insulator labels for power lines to enormous control panels with operating instructions for heavy machinery. Utilizing substrates from paper to polycarbonates, SpecPrint can do just about any printing project. High-end nameplates are printed in reverse on a polycarbonate subsurface, then laminated with an adhesive on top of the ink, making the end-product practically indestructible. The company is based in Mt. Juliet, Tennessee and has 80 employees.
The Challenge
SpecPrint, Inc. had been running its accounting on an AS/400-based package for years. However, the system had a major drawback as it couldn’t handle “coproduct” manufacturing—when two products are made from a single order. This was a significant issue for SpecPrint as many of their products, such as lawn mower hood decals, often consist of mirror-image versions for either side of the mower. These need to be tracked as separate part numbers yet manufactured from the same order. The weaknesses of the legacy system resulted in constant overages and duplicate shipping. The final straw came when the vendor stopped supporting the product. SpecPrint needed a replacement that was PC-based, integrated all manufacturing, inventory, and accounting functions, and most importantly, provided coproduct management.
The Solution
SpecPrint chose Sage 500 ERP as it met all their requirements. The system is used to receive raw materials, compare Purchase Order data information with the Accounts Payable voucher, and set up routings for production. When a customer puts in an order and sends artwork, the system delivers data to the scheduler and transfers instructions to the shop floor. Labor, material, and overhead costs are applied to the job at hand for accurate job costing, which results in increased profitability. Parts are tracked as they go into inventory and shipping, where Sage 500 ERP generates invoices. The Material Requirements Planning (MRP) module automates the function of reordering raw materials for more accurate replenishment.
Operational Impact
Quantitative Benefit
Case Study missing?
Start adding your own!
Register with your work email and create a new case study profile for your business.
Related Case Studies.

Case Study
Plastic Spoons Case study: Injection Moulding
In order to meet customer expectations by supplying a wide variety of packaging units, from 36 to 1000 spoons per package, a new production and packaging line needed to be built. DeSter wanted to achieve higher production capacity, lower cycle time and a high degree of operator friendliness with this new production line.
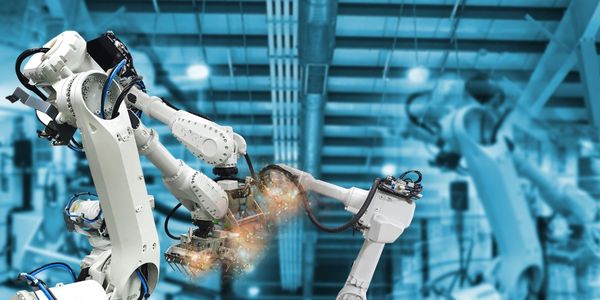
Case Study
Robot Saves Money and Time for US Custom Molding Company
Injection Technology (Itech) is a custom molder for a variety of clients that require precision plastic parts for such products as electric meter covers, dental appliance cases and spools. With 95 employees operating 23 molding machines in a 30,000 square foot plant, Itech wanted to reduce man hours and increase efficiency.
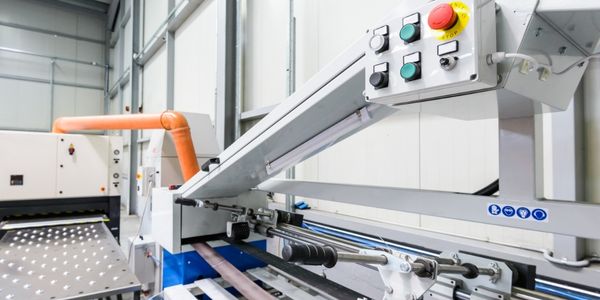
Case Study
Fully Automated Visual Inspection System
Tofflon has developed a fully automatic machine that uses light to inspect vials, medicine bottles, or infusion containers for glass fragments, aluminum particles, rubber grains, hairs, fibers, or other contaminants. It also detects damaged containers with cracks or inclusions (microscopic imperfections), automatically removing faulty or contaminated products. In order to cover all production processes for freeze-dried pharmaceuticals, Tofflon needed to create an open, consistent, and module-based automation concept.
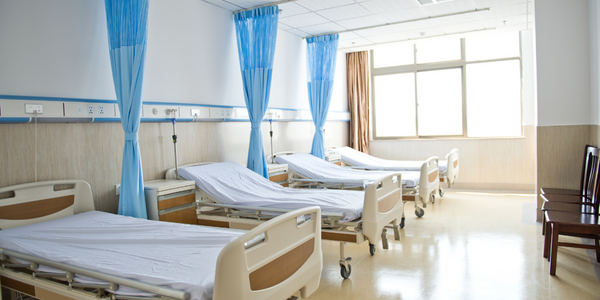
Case Study
Hospital Inventory Management
The hospital supply chain team is responsible for ensuring that the right medical supplies are readily available to clinicians when and where needed, and to do so in the most efficient manner possible. However, many of the systems and processes in use at the cancer center for supply chain management were not best suited to support these goals. Barcoding technology, a commonly used method for inventory management of medical supplies, is labor intensive, time consuming, does not provide real-time visibility into inventory levels and can be prone to error. Consequently, the lack of accurate and real-time visibility into inventory levels across multiple supply rooms in multiple hospital facilities creates additional inefficiency in the system causing over-ordering, hoarding, and wasted supplies. Other sources of waste and cost were also identified as candidates for improvement. Existing systems and processes did not provide adequate security for high-cost inventory within the hospital, which was another driver of cost. A lack of visibility into expiration dates for supplies resulted in supplies being wasted due to past expiry dates. Storage of supplies was also a key consideration given the location of the cancer center’s facilities in a dense urban setting, where space is always at a premium. In order to address the challenges outlined above, the hospital sought a solution that would provide real-time inventory information with high levels of accuracy, reduce the level of manual effort required and enable data driven decision making to ensure that the right supplies were readily available to clinicians in the right location at the right time.
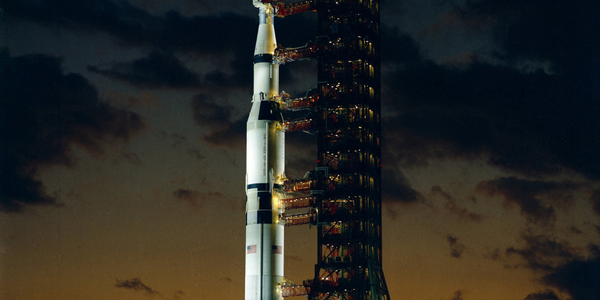
Case Study
SAP Leonardo Enabling Rocket Science
At times, ULA has as many as 15 different operating systems dedicated to overlapping processes, such as rocket design, testing, and launch. Multiple systems created unnecessary costs and unwanted confusion among workers at offices, factories, and launch sites in different location. In order to improve collaboration and transparency during vital activities that directly influence mission success, ULA wanted to improve data sharing and streamline manufacturing processes.