Technology Category
- Functional Applications - Fleet Management Systems (FMS)
- Sensors - Liquid Detection Sensors
Applicable Industries
- Metals
- Transportation
Applicable Functions
- Logistics & Transportation
- Sales & Marketing
Use Cases
- Last Mile Delivery
- Transportation Simulation
About The Customer
Southland Steel Fabricators is a family-owned business that has built a strong reputation over the last three decades for delivering high-quality, timely projects and superior customer service. The company serves numerous prominent clients in industries ranging from oil and gas, chemical, refining, and power generation, to space exploration rocket structures and more. Southland Steel aims to be a one-stop shop for the steel industry by providing services like steel fabrication and galvanization, 3D modeling, and complete project management. The company deploys as many as 10 trucks to carry out their operations and has invested heavily in its facilities and procedures to provide an unrivaled, personalized experience for its customers.
The Challenge
Southland Steel Fabricators, a family-owned business with a reputation for timely project completion and superior customer service, was facing challenges with its manual logistics operations. The company, which serves numerous prominent clients in industries ranging from oil and gas, chemical, refining, and power generation, to space exploration rocket structures and more, deploys as many as 10 trucks to carry out their operations. Despite investing heavily in its facilities and procedures, Southland Steel relied on manual logs and reports for its operations and brokered out its logistics. This led to important information falling through the cracks or getting misplaced, resulting in disorganized processes and unnecessary logistics costs. The pain of manual dispatch was particularly felt when the company landed a large contract for a job in Corpus Cristi, TX, necessitating a dispatch tool that could track their vehicles and assets across the 525 miles between the new job site and the company’s fabrication and galvanization plant in Greensburg, LA.
The Solution
Southland Steel decided to digitize its dispatch through the Motive Fleet dashboard. This provided a level of visibility into the company’s fleet operations that was previously unattainable, helping create detailed reports and invoices, and significantly improving the profitability of the branch. Within just the first month of using Motive, the company saved at least $25,000 in previously overlooked or lost charges. The logistics team at Southland Steel can now plan, assign, monitor, and review all their logistics in the Motive Fleet dashboard. Furthermore, Motive has improved relationships with the company’s drivers. Instead of having to chase down information about their load and deliveries or juggle multiple emails, text messages, and back-and-forth phone calls, drivers can now simply check their Motive app for all their job needs.
Operational Impact
Quantitative Benefit
Case Study missing?
Start adding your own!
Register with your work email and create a new case study profile for your business.
Related Case Studies.
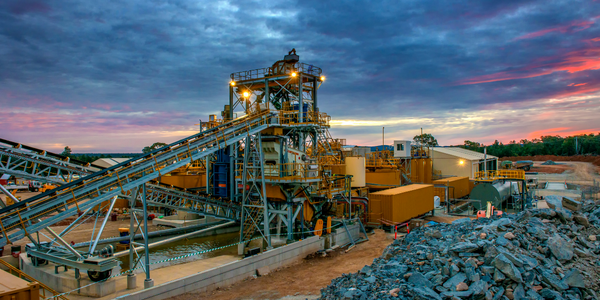
Case Study
Goldcorp: Internet of Things Enables the Mine of the Future
Goldcorp is committed to responsible mining practices and maintaining maximum safety for its workers. At the same time, the firm is constantly exploring ways to improve the efficiency of its operations, extend the life of its assets, and control costs. Goldcorp needed technology that can maximize production efficiency by tracking all mining operations, keep employees safe with remote operations and monitoring of hazardous work areas and control production costs through better asset and site management.
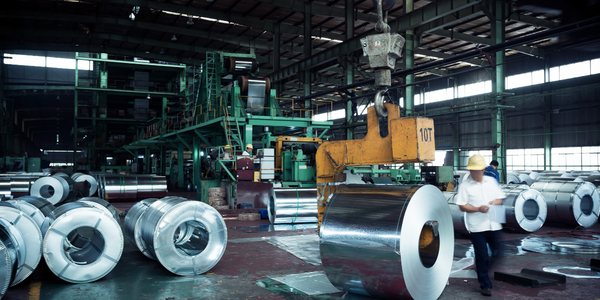
Case Study
KSP Steel Decentralized Control Room
While on-site in Pavlodar, Kazakhstan, the DAQRI team of Business Development and Solutions Architecture personnel worked closely with KSP Steel’s production leadership to understand the steel production process, operational challenges, and worker pain points.
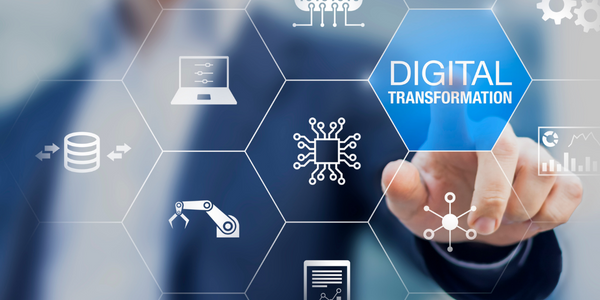
Case Study
Bluescope Steel on Path to Digitally Transform Operations and IT
Increasing competition and fluctuations in the construction market prompted BlueScope Steel to look toward digital transformation of its four businesses, including modern core applications and IT infrastructure. BlueScope needed to modernize its infrastructure and adopt new technologies to improve operations and supply chain efficiency while maintaining and updating an aging application portfolio.
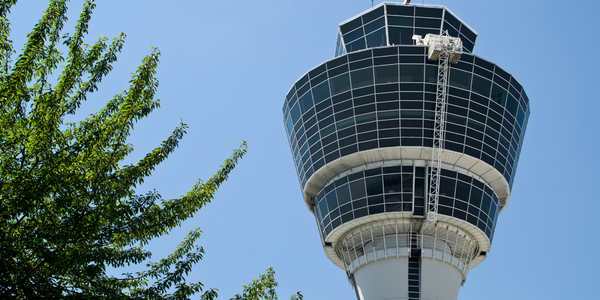
Case Study
Airport SCADA Systems Improve Service Levels
Modern airports are one of the busiest environments on Earth and rely on process automation equipment to ensure service operators achieve their KPIs. Increasingly airport SCADA systems are being used to control all aspects of the operation and associated facilities. This is because unplanned system downtime can cost dearly, both in terms of reduced revenues and the associated loss of customer satisfaction due to inevitable travel inconvenience and disruption.
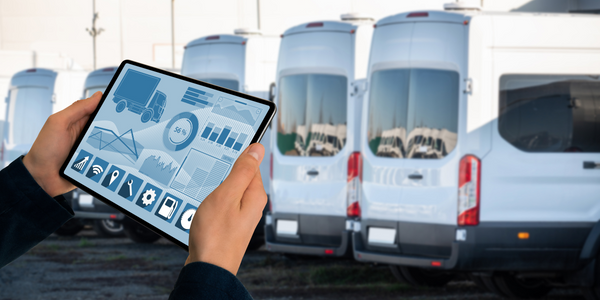
Case Study
IoT-based Fleet Intelligence Innovation
Speed to market is precious for DRVR, a rapidly growing start-up company. With a business model dependent on reliable mobile data, managers were spending their lives trying to negotiate data roaming deals with mobile network operators in different countries. And, even then, service quality was a constant concern.
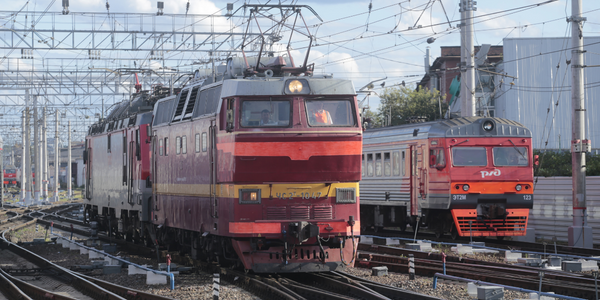
Case Study
Digitize Railway with Deutsche Bahn
To reduce maintenance costs and delay-causing failures for Deutsche Bahn. They need manual measurements by a position measurement system based on custom-made MEMS sensor clusters, which allow autonomous and continuous monitoring with wireless data transmission and long battery. They were looking for data pre-processing solution in the sensor and machine learning algorithms in the cloud so as to detect critical wear.