Customer Company Size
Large Corporate
Region
- America
Country
- United States
Product
- COMSOL Multiphysics
- FUJIFILM Dimatix Printheads
Tech Stack
- Multiphysics Simulation
- MEMS Fabrication
- Piezoelectric Devices Interface
Implementation Scale
- Enterprise-wide Deployment
Impact Metrics
- Productivity Improvements
- Innovation Output
- Cost Savings
Technology Category
- Analytics & Modeling - Predictive Analytics
- Analytics & Modeling - Digital Twin / Simulation
Applicable Industries
- Electronics
- Consumer Goods
Applicable Functions
- Product Research & Development
- Quality Assurance
Use Cases
- Predictive Maintenance
- Digital Twin
- Process Control & Optimization
Services
- Software Design & Engineering Services
- System Integration
About The Customer
FUJIFILM Dimatix is a leading producer of commercial inkjet printheads, known for their high-performance and innovative solutions in the printing industry. Their products are used in a wide range of applications, from commercial packaging and wide-format graphics to textiles and electronic applications. The company is committed to advancing inkjet technology and has a strong focus on research and development to maintain its competitive edge. By leveraging advanced simulation tools, FUJIFILM Dimatix aims to enhance the performance and efficiency of their printhead actuators, ensuring high-quality printing solutions for their diverse customer base.
The Challenge
The primary challenge faced by FUJIFILM Dimatix was to design unimorph diaphragm actuators for their newest ink deposition products. These actuators needed to be miniaturized to reduce costs while maximizing deflection and matching the actuator's impedance to the flow channels and nozzle. The goal was to generate a droplet meeting a target mass at a given velocity with a target maximum firing frequency for the available voltage. The complexity of the design required a deep understanding of the interactions between the piezoelectric materials and the surrounding components, necessitating a robust simulation approach to optimize the design parameters.
The Solution
To address the challenge, FUJIFILM Dimatix employed a two-stage modeling approach using COMSOL Multiphysics software. In the first stage, various actuator geometries were modeled to determine their functional parameters. These parameters were then used in a complete jet model to understand the system's response. The simulation included different layers for the silicon, metals, insulators, and PZT, as well as sections of the ink-filled pumping chamber and neighboring flow channels. By simulating the actuator's deflection under pressure and voltage loads, the team could extract valuable compliance and output data. This information was crucial for optimizing the design to meet the tight specifications and smaller geometries required for the new printheads.
Operational Impact
Quantitative Benefit
Case Study missing?
Start adding your own!
Register with your work email and create a new case study profile for your business.
Related Case Studies.
.png)
Case Study
Improving Vending Machine Profitability with the Internet of Things (IoT)
The vending industry is undergoing a sea change, taking advantage of new technologies to go beyond just delivering snacks to creating a new retail location. Intelligent vending machines can be found in many public locations as well as company facilities, selling different types of goods and services, including even computer accessories, gold bars, tickets, and office supplies. With increasing sophistication, they may also provide time- and location-based data pertaining to sales, inventory, and customer preferences. But at the end of the day, vending machine operators know greater profitability is driven by higher sales and lower operating costs.

Case Study
Remote Temperature Monitoring of Perishable Goods Saves Money
RMONI was facing temperature monitoring challenges in a cold chain business. A cold chain must be established and maintained to ensure goods have been properly refrigerated during every step of the process, making temperature monitoring a critical business function. Manual registration practice can be very costly, labor intensive and prone to mistakes.
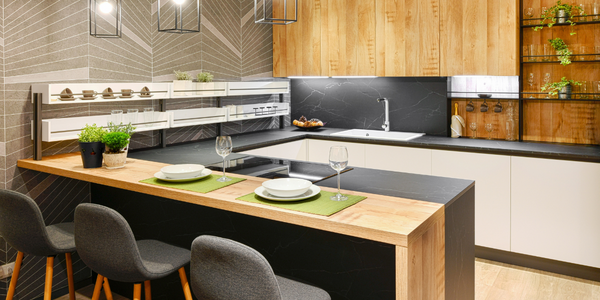
Case Study
Series Production with Lot-size-1 Flexibility
Nobilia manufactures customized fitted kitchens with a lot size of 1. They require maximum transparency of tracking design data and individual processing steps so that they can locate a particular piece of kitchen furniture in the sequence of processes.