Company Size
1,000+
Product
- JDA® Order Sequencing & Slotting
Tech Stack
- Not mentioned
Implementation Scale
- Enterprise-wide Deployment
Impact Metrics
- Customer Satisfaction
- Productivity Improvements
Technology Category
- Functional Applications - Manufacturing Execution Systems (MES)
Applicable Industries
- Automotive
Applicable Functions
- Discrete Manufacturing
Use Cases
- Manufacturing System Automation
Services
- Software Design & Engineering Services
- System Integration
About The Customer
Fiat Chrysler Automobiles (FCA) is the world’s seventh-largest auto manufacturer, shipping 4.6 million cars in 2014. Its brands include Alfa Romeo, Chrysler, Dodge, Fiat, Jeep, Lancia, Ram, Ferrari, and Maserati. These vehicles are produced at facilities in more than 40 countries and then shipped to customers around the world. The company relies on its global supply chain as a competitive advantage and is constantly seeking ways to improve the speed of delivery and increase flexibility.
The Challenge
Fiat Chrysler Automobiles (FCA), the world’s seventh-largest auto manufacturer, faced challenges in increasing production speed and consistency due to the growth of global demand for automobiles. The company was running its plants and suppliers at full capacity, which led to capacity chokepoints. Identifying and managing these constraints became a priority for FCA. The company needed a solution that could help them identify these capacity chokepoints as early as possible and work to resolve them, thereby improving the speed of delivery.
The Solution
FCA implemented JDA’s Manufacturing Planning solution, specifically the JDA® Order Sequencing & Slotting, to manage constraints and maximize production capacity. The solution provides built-in optimizers and operating constraints, ensuring that order schedules maximize productivity across multiple facilities. Based on specific order requirements such as customer priority, delivery commitments, and product features, vehicles are placed into the optimal manufacturing sequence at FCA. The technology enables FCA to identify problems with the order flow much earlier than its previous process, allowing for corrective action with the dealers and markets, and ensuring smooth production flow.
Operational Impact
Case Study missing?
Start adding your own!
Register with your work email and create a new case study profile for your business.
Related Case Studies.
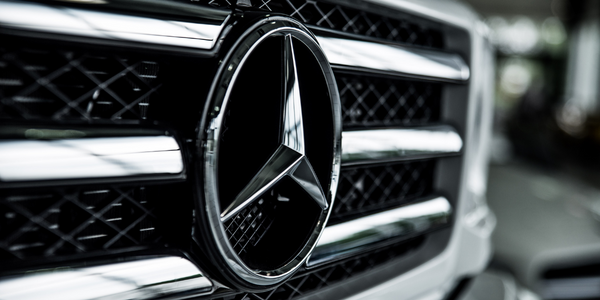
Case Study
Integral Plant Maintenance
Mercedes-Benz and his partner GAZ chose Siemens to be its maintenance partner at a new engine plant in Yaroslavl, Russia. The new plant offers a capacity to manufacture diesel engines for the Russian market, for locally produced Sprinter Classic. In addition to engines for the local market, the Yaroslavl plant will also produce spare parts. Mercedes-Benz Russia and his partner needed a service partner in order to ensure the operation of these lines in a maintenance partnership arrangement. The challenges included coordinating the entire maintenance management operation, in particular inspections, corrective and predictive maintenance activities, and the optimizing spare parts management. Siemens developed a customized maintenance solution that includes all electronic and mechanical maintenance activities (Integral Plant Maintenance).
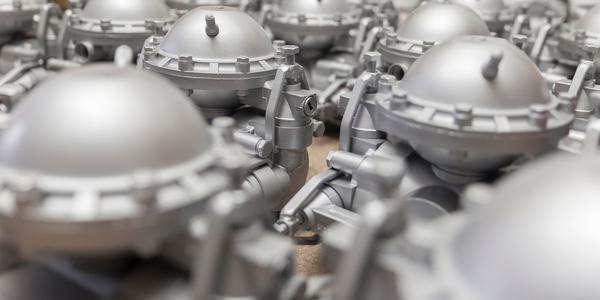
Case Study
Monitoring of Pressure Pumps in Automotive Industry
A large German/American producer of auto parts uses high-pressure pumps to deburr machined parts as a part of its production and quality check process. They decided to monitor these pumps to make sure they work properly and that they can see any indications leading to a potential failure before it affects their process.