Serapid Increases Accuracy with JobBOSS
Customer Company Size
SME
Region
- America
Country
- United States
Product
- JobBOSS enterprise resource planning (ERP)
- SolidWorks computer-assisted design (CAD)
- CAD BOM Import
Tech Stack
- ERP
- CAD
Implementation Scale
- Enterprise-wide Deployment
Impact Metrics
- Productivity Improvements
- Cost Savings
- Customer Satisfaction
Technology Category
- Functional Applications - Enterprise Resource Planning Systems (ERP)
- Functional Applications - Product Data Management Systems
Applicable Industries
- Aerospace
- Construction & Infrastructure
Applicable Functions
- Discrete Manufacturing
- Procurement
Use Cases
- Manufacturing System Automation
- Inventory Management
Services
- Software Design & Engineering Services
- System Integration
About The Customer
Serapid is a manufacturer of products and systems for the precision movement of heavy loads. These systems are used in a variety of applications for diverse industries including metal forming industries, aerospace manufacturers, defense contractors, theater design and architectural construction firms. The company’s U.S. office employs 24 people in its Sterling Heights, Michigan shop. In 2014, the company ran around 400 jobs, with 100 components and 100 production lines for each particular job on average. It uses JobBOSS enterprise resource planning (ERP) and SolidWorks computer-assisted design (CAD) programs as part of their software suite to manage their business.
The Challenge
Serapid, a manufacturer of products and systems for the precision movement of heavy loads, was previously using spreadsheets to create a Bill of Materials (BOM) based on the CAD model of parts it was making. Each job would get its own sheet, and then the data would be integrated into a larger master file used for purchasing supplies. This manual method took a long time to complete because various amounts of information had to be inputted, and company engineers had to “translate” to purchasing managers what exactly they wanted. Even small jobs with 20 or less components took an hour to fill out because of the number of steps and manual entry involved. Larger jobs tended to be too much of a hassle to enter the full BOM.
The Solution
Serapid sought out a solution to wean them off of Excel to bring efficiency to their operations. When Serapid implemented JobBOSS into its operations, it used a third-party CAD BOM importer so that data from the part’s 3-D model could be translated into information on the raw materials required. However, the implementation went poorly, with the software failing to integrate JobBOSS with Solidworks. In response, JobBOSS signed Serapid up for the company’s in-house CAD BOM importer. While it was still in beta at the time, Serapid nevertheless joined in and was able to contribute feedback on the product direction throughout the beta process. The results were a complete turnaround in terms of service and performance. The implementation was a success, and the company continues to use the CAD BOM Import, which is now available to all customers of the ERP software.
Operational Impact
Quantitative Benefit
Case Study missing?
Start adding your own!
Register with your work email and create a new case study profile for your business.
Related Case Studies.
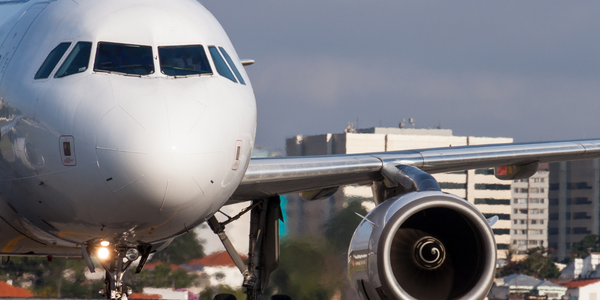
Case Study
Airbus Soars with Wearable Technology
Building an Airbus aircraft involves complex manufacturing processes consisting of thousands of moving parts. Speed and accuracy are critical to business and competitive advantage. Improvements in both would have high impact on Airbus’ bottom line. Airbus wanted to help operators reduce the complexity of assembling cabin seats and decrease the time required to complete this task.

Case Study
IoT System for Tunnel Construction
The Zenitaka Corporation ('Zenitaka') has two major business areas: its architectural business focuses on structures such as government buildings, office buildings, and commercial facilities, while its civil engineering business is targeted at structures such as tunnels, bridges and dams. Within these areas, there presented two issues that have always persisted in regard to the construction of mountain tunnels. These issues are 'improving safety" and "reducing energy consumption". Mountain tunnels construction requires a massive amount of electricity. This is because there are many kinds of electrical equipment being used day and night, including construction machinery, construction lighting, and ventilating fan. Despite this, the amount of power consumption is generally not tightly managed. In many cases, the exact amount of power consumption is only ascertained when the bill from the power company becomes available. Sometimes, corporations install demand-monitoring equipment to help curb the maximum power demanded. However, even in these cases, the devices only allow the total volume of power consumption to be ascertained, or they may issue warnings to prevent the contracted volume of power from being exceeded. In order to tackle the issue of reducing power consumption, it was first necessary to obtain an accurate breakdown of how much power was being used in each particular area. In other words, we needed to be able to visualize the amount of power being consumed. Safety, was also not being managed very rigorously. Even now, tunnel construction sites often use a 'name label' system for managing entry into the work site. Specifically, red labels with white reverse sides that bear the workers' names on both sides are displayed at the tunnel work site entrance. The workers themselves then flip the name label to the appropriate side when entering or exiting from the work site to indicate whether or not they are working inside the tunnel at any given time. If a worker forgets to flip his or her name label when entering or exiting from the tunnel, management cannot be performed effectively. In order to tackle the challenges mentioned above, Zenitaka decided to build a system that could improve the safety of tunnel construction as well as reduce the amount of power consumed. In other words, this new system would facilitate a clear picture of which workers were working in each location at the mountain tunnel construction site, as well as which processes were being carried out at those respective locations at any given time. The system would maintain the safety of all workers while also carefully controlling the electrical equipment to reduce unnecessary power consumption. Having decided on the concept, our next concern was whether there existed any kind of robust hardware that would not break down at the construction work site, that could move freely in response to changes in the working environment, and that could accurately detect workers and vehicles using radio frequency identification (RFID). Given that this system would involve many components that were new to Zenitaka, we decided to enlist the cooperation of E.I.Sol Co., Ltd. ('E.I.Sol') as our joint development partner, as they had provided us with a highly practical proposal.
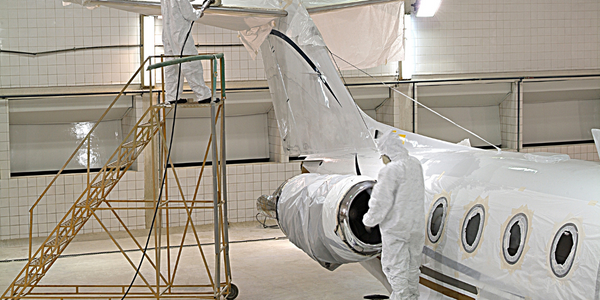
Case Study
Aircraft Predictive Maintenance and Workflow Optimization
First, aircraft manufacturer have trouble monitoring the health of aircraft systems with health prognostics and deliver predictive maintenance insights. Second, aircraft manufacturer wants a solution that can provide an in-context advisory and align job assignments to match technician experience and expertise.
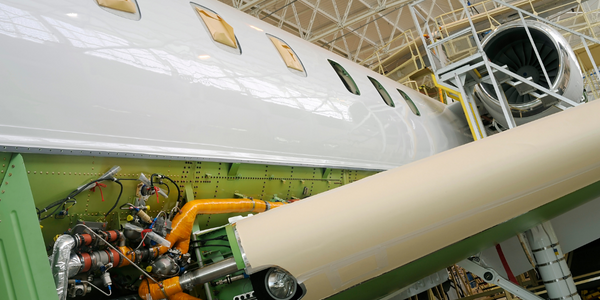
Case Study
Aerospace & Defense Case Study Airbus
For the development of its new wide-body aircraft, Airbus needed to ensure quality and consistency across all internal and external stakeholders. Airbus had many challenges including a very aggressive development schedule and the need to ramp up production quickly to satisfy their delivery commitments. The lack of communication extended design time and introduced errors that drove up costs.
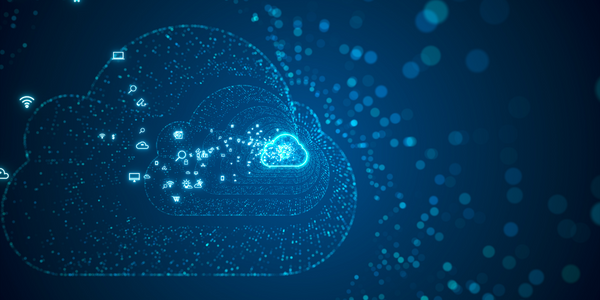
Case Study
Splunk Partnership Ties Together Big Data & IoT Services
Splunk was faced with the need to meet emerging customer demands for interfacing IoT projects to its suite of services. The company required an IoT partner that would be able to easily and quickly integrate with its Splunk Enterprise platform, rather than allocating development resources and time to building out an IoT interface and application platform.