Customer Company Size
Large Corporate
Region
- Europe
Country
- United Kingdom
Product
- Vocollect Voice Directed Distribution
- Manhattan Associates’ WMOS
Tech Stack
- Voice Technology
- Warehouse Management System (WMS)
- Real-time Productivity Status Reporting
Implementation Scale
- Enterprise-wide Deployment
Impact Metrics
- Productivity Improvements
- Customer Satisfaction
- Employee Satisfaction
Technology Category
- Functional Applications - Warehouse Management Systems (WMS)
- Functional Applications - Remote Monitoring & Control Systems
Applicable Industries
- Food & Beverage
Applicable Functions
- Warehouse & Inventory Management
- Logistics & Transportation
Use Cases
- Inventory Management
- Warehouse Automation
- Fleet Management
Services
- System Integration
- Training
About The Customer
3663 supplies a wide choice of foods and commercial kitchen equipment to all areas of the foodservice market. They deliver frozen, fresh, chilled, non-food, and catering equipment products to a range of customers, from small independents to large national accounts. With 23 depots and 4 regional distribution centres spread throughout the UK, 3663 is the UK’s leading foodservice company with sales of over £1.6 billion a year, delivering quality ingredients, finished products, and equipment to the catering industry. 3663 has over 4,200 employees and a modern fleet of 800 temperature-controlled vehicles, making an average of 45,000 deliveries a week to their customer base which includes Burger King, KFC, and Nandos. The management team at 3663 is always looking for new ways of improving operational performance, with the aim of increasing profitability while continuing to deliver outstanding customer service.
The Challenge
With an entire supply chain relying on its operations, time is of the essence for 3663’s Logistics division. The division has a long-standing commitment to moving goods to the right place at the right time without incident or error. For the business to sustain increased growth and profitability, 3663 could not afford unexpected costs such as sending out half-empty lorries or high levels of inaccurate selection. In addition to accuracy, productivity and speed are of vital importance to the company’s profit margins. The more products the company can move in a day, the greater the increase in revenue, so having a focused approach to ensuring processes are not duplicated needlessly is essential. In their quest for logistics excellence, 3663 turned the spotlight on the company’s long-standing, paper-driven processes to see how voice technology could help to increase accuracy, speed up order selection, gain better visibility of stock, streamline processes and make the best possible use of its workforce.
The Solution
To meet its needs, 3663’s warehouse operations chose Vocollect’s Voice Directed Distribution in conjunction with the Manhattan Associates’ WMOS. This facilitated order verification very early upstream, as soon as the article is picked, not just on the basis of its location in the warehouse. 3663 approached one of Vocollect’s certified partners to roll out a fully integrated Warehouse Management System (WMS) driven by Vocollect Voice across four logistics depots: Banbury; Litchfield; Royton and Heywood. The Vocollect Voice application allowed employees on the ground to move stock more quickly and accurately through all stages of the warehouse cycle. The distribution centre employees wear a lightweight Vocollect wearable mobile computing device and headset, allowing them to work Hands-Free, Eyes-Free in a safer environment. The previous process was very complex, running almost entirely on a paper-based system, supported by manual control processes. Now, the WMS incorporates a voice management console, providing the business units with a unified overview of all processes in real-time throughout the day – allowing faster response times, the ability to spot variances in performance and better planning and reporting.
Operational Impact
Quantitative Benefit
Case Study missing?
Start adding your own!
Register with your work email and create a new case study profile for your business.
Related Case Studies.

Case Study
The Kellogg Company
Kellogg keeps a close eye on its trade spend, analyzing large volumes of data and running complex simulations to predict which promotional activities will be the most effective. Kellogg needed to decrease the trade spend but its traditional relational database on premises could not keep up with the pace of demand.

Case Study
HEINEKEN Uses the Cloud to Reach 10.5 Million Consumers
For 2012 campaign, the Bond promotion, it planned to launch the campaign at the same time everywhere on the planet. That created unprecedented challenges for HEINEKEN—nowhere more so than in its technology operation. The primary digital content for the campaign was a 100-megabyte movie that had to play flawlessly for millions of viewers worldwide. After all, Bond never fails. No one was going to tolerate a technology failure that might bruise his brand.Previously, HEINEKEN had supported digital media at its outsourced datacenter. But that datacenter lacked the computing resources HEINEKEN needed, and building them—especially to support peak traffic that would total millions of simultaneous hits—would have been both time-consuming and expensive. Nor would it have provided the geographic reach that HEINEKEN needed to minimize latency worldwide.

Case Study
Energy Management System at Sugar Industry
The company wanted to use the information from the system to claim under the renewable energy certificate scheme. The benefit to the company under the renewable energy certificates is Rs 75 million a year. To enable the above, an end-to-end solution for load monitoring, consumption monitoring, online data monitoring, automatic meter data acquisition which can be exported to SAP and other applications is required.

Case Study
Coca Cola Swaziland Conco Case Study
Coco Cola Swaziland, South Africa would like to find a solution that would enable the following results: - Reduce energy consumption by 20% in one year. - Formulate a series of strategic initiatives that would enlist the commitment of corporate management and create employee awareness while helping meet departmental targets and investing in tools that assist with energy management. - Formulate a series of tactical initiatives that would optimize energy usage on the shop floor. These would include charging forklifts and running cold rooms only during off-peak periods, running the dust extractors only during working hours and basing lights and air-conditioning on someone’s presence. - Increase visibility into the factory and other processes. - Enable limited, non-intrusive control functions for certain processes.

Case Study
Temperature Monitoring for Restaurant Food Storage
When it came to implementing a solution, Mr. Nesbitt had an idea of what functionality that he wanted. Although not mandated by Health Canada, Mr. Nesbitt wanted to ensure quality control issues met the highest possible standards as part of his commitment to top-of-class food services. This wish list included an easy-to use temperature-monitoring system that could provide a visible display of the temperatures of all of his refrigerators and freezers, including historical information so that he could review the performance of his equipment. It also had to provide alert notification (but email alerts and SMS text message alerts) to alert key staff in the event that a cooling system was exceeding pre-set warning limits.
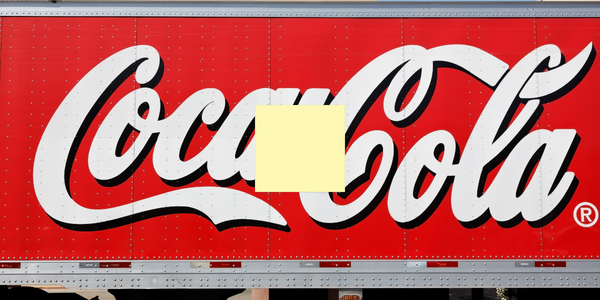
Case Study
Coca-Cola Refreshments, U.S.
Coca-Cola Refreshments owns and manages Coca-Cola branded refrigerators in retail establishments. Legacy systems were used to locate equipment information by logging onto multiple servers which took up to 8 hours to update information on 30-40 units. The company had no overall visibility into equipment status or maintenance history.