Semiconductor Equipment Manufacturer Gains Double Digit % Savings on Parts Using aPriori
Company Size
1,000+
Region
- America
Country
- United States
Product
- aPriori Product Cost Management
- aPriori Virtual Production Environments (VPEs)
Tech Stack
- Computer-Aided Design (CAD)
- Intelligent Cost Models
- ERP Integration
- PLM Integration
Implementation Scale
- Enterprise-wide Deployment
Impact Metrics
- Cost Savings
- Customer Satisfaction
- Productivity Improvements
Technology Category
- Analytics & Modeling - Predictive Analytics
- Application Infrastructure & Middleware - Data Exchange & Integration
- Functional Applications - Product Lifecycle Management Systems (PLM)
Applicable Industries
- Semiconductors
Applicable Functions
- Procurement
- Product Research & Development
- Quality Assurance
Use Cases
- Predictive Maintenance
Services
- Software Design & Engineering Services
- System Integration
About The Customer
This semiconductor equipment manufacturer is a leading provider of equipment and services to the semiconductor manufacturing industry. The company is known for its relentless pursuit of operational excellence and innovation. Its customers include many of the world’s largest semiconductor manufacturers, who rely on its equipment and process expertise to develop transistors for various electronics, such as smartphones, tablets, laptops, and personal music players. The company offers a powerful suite of manufacturing technologies for the IC manufacturing process and extensive aftermarket service and support, including spare parts, equipment upgrades, maintenance services, and customer training. It works closely with customers to tailor its offerings to their unique needs and goals.
The Challenge
The semiconductor equipment manufacturer faced significant challenges in estimating the costs of high-tech, complex parts produced in low volumes. These parts often require precision machining and have a high sensitivity to geometric tolerances, making cost estimation particularly difficult. The company needed a solution to provide accurate cost estimates early in the product design process to make informed design decisions, compress cycle times, reduce development costs, and bring new products to market more quickly.
The Solution
The semiconductor equipment manufacturer implemented aPriori’s Product Cost Management software platform to reduce product costs. The software equips engineering, manufacturing, and sourcing professionals with the knowledge and technology infrastructure to quickly and precisely determine the cost of a part or complete product. It leverages computer-aided design and intelligent cost models to generate detailed manufacturing analysis and cost estimates, quantifying the impact of changes to product design, materials, manufacturing processes, volumes, and location in real time. The software also enables users to refine costs by providing detailed inputs and overriding defaults to create a should-cost for supplier negotiation or a manufacturing estimate. Additionally, it allows for the import of complex engineering Bills of Materials (BOMs) from ERP, PLM, MRP, or other enterprise applications, facilitating communication of product cost information across all functional organizations involved in product definition and delivery.
Operational Impact
Quantitative Benefit
Case Study missing?
Start adding your own!
Register with your work email and create a new case study profile for your business.
Related Case Studies.
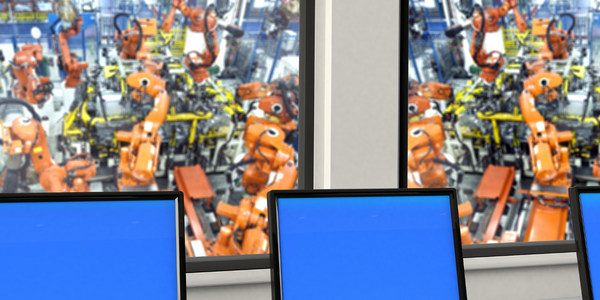
Case Study
KINESYS Semiconductor Factory Automation Software
KINESYS Software provides both Integrated Device Manufacturer (IDM) and Original Equipment Manufacturer (OEM) customers world-class software products and solutions for advanced wafer and device traceability and process management. KINESYS offers state of the art database technology with a core focus on SEMI standards. KINESYS’ challenge was to make back-end processing failure-free and easy to use for clients while supporting licensing models more adaptable to changing industry needs.
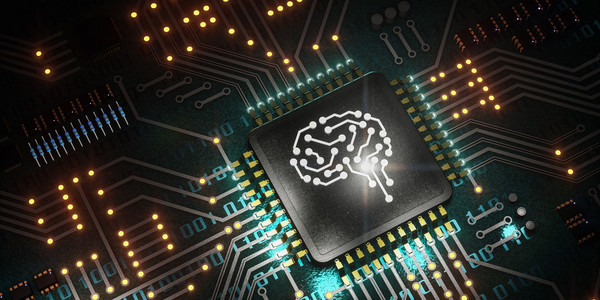
Case Study
Modular AI Defect Inspection Solution for Efficient Semiconductor Equipment Upgrades
Smasoft Technology Co., Ltd., a System Integrator that develops industrial automation software and offers AI application solutions, was commissioned by a semiconductor equipment manufacturer to implement AI inspection features into their Extreme Ultraviolet Light (EUV) pod inspection machines. The existing AOI software in the EUV pod inspection machines could only identify defective products but could not trace the cause of the defects. The manufacturer wanted to upgrade their machines with AI features to make the products more useful. The AI solution needed to complete the analysis of 380 images for a single pod within two minutes and inspect different materials simultaneously. This required multiple sets of AI models for interpretation. The solution also needed to be installed in a cabinet in the lower half of the machines, which posed a challenge due to the limited space. Smasoft needed to purchase a hardware solution with strong computing performance, stable operation, compact size, and flexible configuration to overcome these challenges.

Case Study
Rapid Hybrid Services Deployment for Global Semiconductor Company
The U.S. manufacturer of engineered materials, optoelectronic components, and semiconductors was focused on growth through mergers and acquisitions (M&As). In 2019–2020, it acquired a global electronics firm and needed immediate connectivity and visibility into the acquired firm’s geo-distributed operations. The company had a highly compressed timeline, with only days to integrate the firm’s DDI operations, while deferring a full network migration to a future date. The company was actively engaged in acquiring and merging strategically aligned companies as a key global growth strategy. The company needed to rapidly integrate its new operations, which included significant remote locations in Asia. The company turned to Infoblox to quickly design a highly secure, available, and reliable solution that could deliver full visibility into new sites. It needed dynamic scalability to accommodate its growing operations and the ability to unify a disparate, geo-diverse infrastructure.
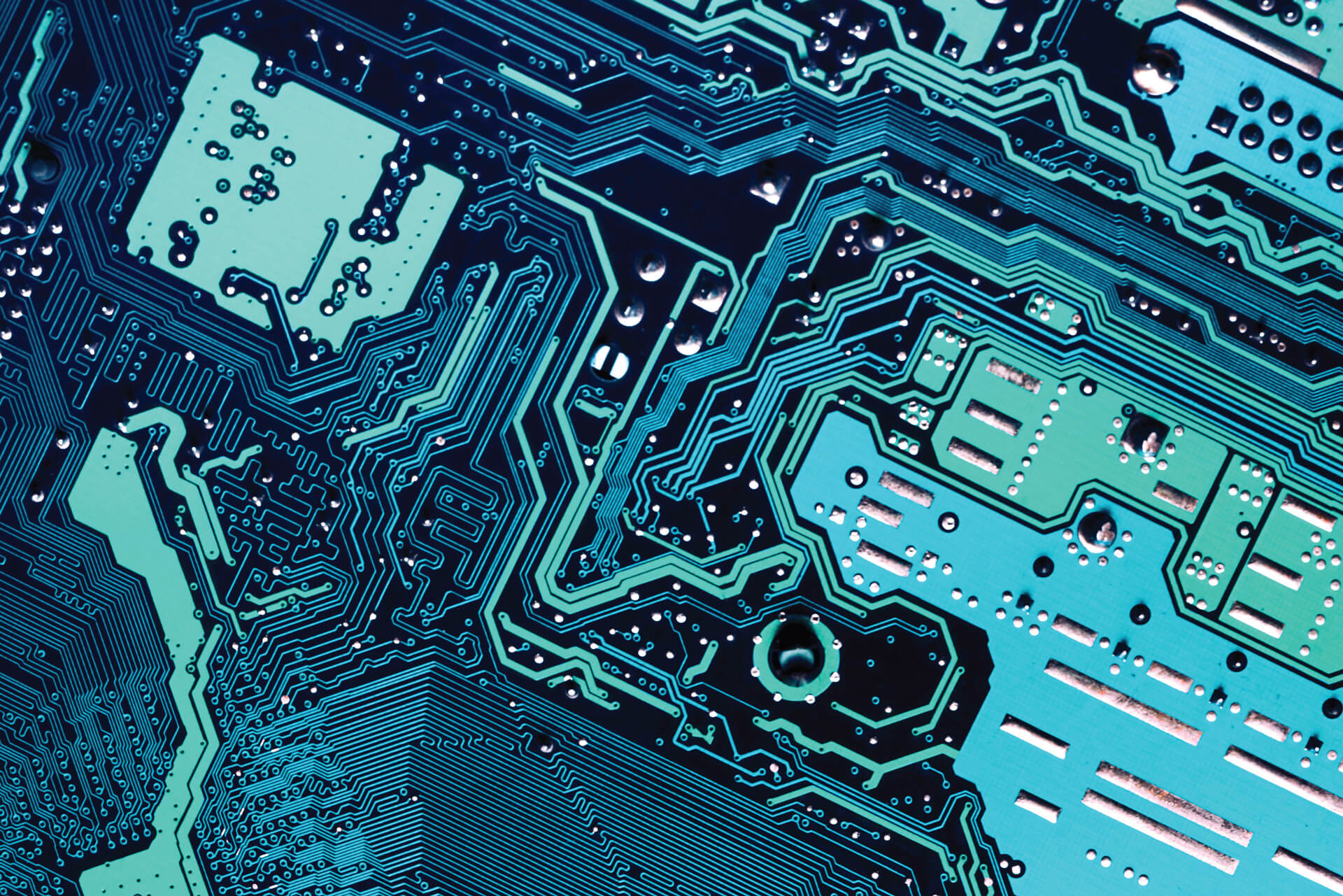
Case Study
Optimizing Semiconductor Manufacturing Yield with IoT
A large U.S.-based manufacturer of high-performance semiconductors was facing a significant challenge in optimizing the manufacturing process of its wireless products. The company, which designs and delivers a broad set of cutting-edge products including radio frequency filters, amplifiers, modulators, attenuators, and more, was experiencing lower than expected overall yield in some of its most complex products. This was affecting the company's productivity and profitability, and there was a need for a solution that could predict low-yield wafers early in the process and identify process improvements to increase overall yield.
Case Study
Leveraging Xenko Game Engine for Immersive VR Experiences: A StarBreach Case Study
Silicon Studio, the developer of the open-source cross-platform game engine Xenko, was looking to showcase the impressive graphical capabilities of their product. They aimed to demonstrate the engine's compatibility with VR and its ability to deliver high-quality virtual reality experiences and games. To achieve this, they needed to create a demo game, StarBreach, that would effectively highlight these features. However, they required an experienced art production team that could create high-quality game art for StarBreach. The challenge was not only to create visually appealing assets but also to demonstrate the technological possibilities of the Xenko game engine.