Technology Category
- Functional Applications - Computerized Maintenance Management Systems (CMMS)
- Functional Applications - Inventory Management Systems
Applicable Industries
- Food & Beverage
- Transportation
Applicable Functions
- Maintenance
- Warehouse & Inventory Management
Use Cases
- Inventory Management
- Picking, Sorting & Positioning
Services
- Testing & Certification
- Training
About The Customer
Fulcher’s Seafood is a North Carolina-based seafood company that specializes in prepared foods. The company was founded by Chaz Fulcher and his sister Christina Fulcher-Cahoon, who launched their prepared food business with just four products. The company has since grown, expanding its product range to include six, eight, and then 12 items. Despite the challenges posed by the pandemic, the company experienced a surge in demand, doubling its sales in just three months. Fulcher’s Seafood prides itself on its commitment to food safety and quality, with 80% of its customers requiring HACCP, FDA FSMA, and SQF certification.
The Challenge
Fulcher’s Seafood, a North Carolina-based seafood company, was facing a significant challenge in scaling up their operations. The company experienced a sudden surge in demand for its prepared foods due to the pandemic, doubling their sales in just three months. However, hiring and training new employees to meet this demand was not feasible due to budget and time constraints. The company was also grappling with stringent food safety certification requirements, which were prerequisites for 80% of their customers. Furthermore, the company was struggling with poor inventory control, which was causing late deliveries, stock-outs, and short orders. The manual system of using pens and spreadsheets was proving to be inefficient and error-prone, leading to a domino effect of issues downstream.
The Solution
Fulcher’s Seafood turned to Mar-Kov’s food manufacturing software to address these challenges. The software provided real-time inventory control, enabling the company to meet unprecedented production and delivery targets. It also helped the company comply with food safety certification requirements. The software allowed employees to update inventory every shift, and the quarterly inventory count was streamlined, taking only 36 hours with the help of bar code scanners and tablets. Mar-Kov’s software also proved invaluable during the eight annual scheduled and random internal and third-party audits. It enabled instant access to accurate, detailed information, reducing the time required to pull data and create reports from hours to just a few minutes. The software also stored the company’s 40 to 60 recipes, recorded updates, and ensured the correct ingredients were used in the right amounts.
Operational Impact
Quantitative Benefit
Case Study missing?
Start adding your own!
Register with your work email and create a new case study profile for your business.
Related Case Studies.

Case Study
The Kellogg Company
Kellogg keeps a close eye on its trade spend, analyzing large volumes of data and running complex simulations to predict which promotional activities will be the most effective. Kellogg needed to decrease the trade spend but its traditional relational database on premises could not keep up with the pace of demand.
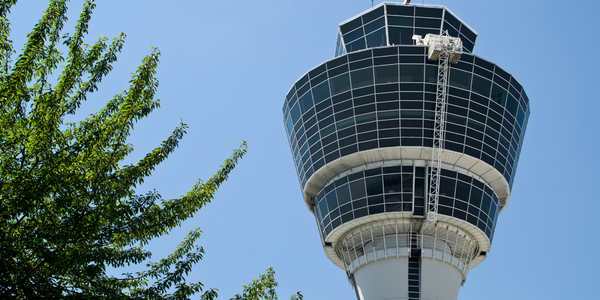
Case Study
Airport SCADA Systems Improve Service Levels
Modern airports are one of the busiest environments on Earth and rely on process automation equipment to ensure service operators achieve their KPIs. Increasingly airport SCADA systems are being used to control all aspects of the operation and associated facilities. This is because unplanned system downtime can cost dearly, both in terms of reduced revenues and the associated loss of customer satisfaction due to inevitable travel inconvenience and disruption.
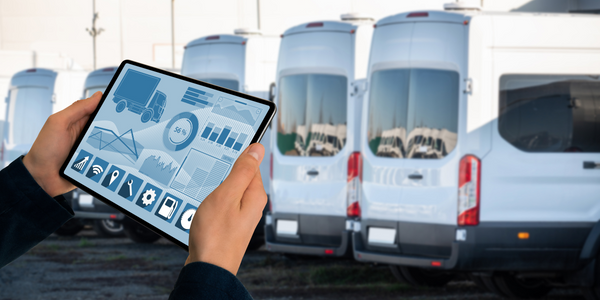
Case Study
IoT-based Fleet Intelligence Innovation
Speed to market is precious for DRVR, a rapidly growing start-up company. With a business model dependent on reliable mobile data, managers were spending their lives trying to negotiate data roaming deals with mobile network operators in different countries. And, even then, service quality was a constant concern.

Case Study
HEINEKEN Uses the Cloud to Reach 10.5 Million Consumers
For 2012 campaign, the Bond promotion, it planned to launch the campaign at the same time everywhere on the planet. That created unprecedented challenges for HEINEKEN—nowhere more so than in its technology operation. The primary digital content for the campaign was a 100-megabyte movie that had to play flawlessly for millions of viewers worldwide. After all, Bond never fails. No one was going to tolerate a technology failure that might bruise his brand.Previously, HEINEKEN had supported digital media at its outsourced datacenter. But that datacenter lacked the computing resources HEINEKEN needed, and building them—especially to support peak traffic that would total millions of simultaneous hits—would have been both time-consuming and expensive. Nor would it have provided the geographic reach that HEINEKEN needed to minimize latency worldwide.
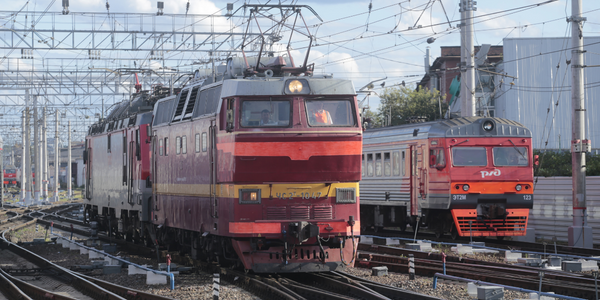
Case Study
Digitize Railway with Deutsche Bahn
To reduce maintenance costs and delay-causing failures for Deutsche Bahn. They need manual measurements by a position measurement system based on custom-made MEMS sensor clusters, which allow autonomous and continuous monitoring with wireless data transmission and long battery. They were looking for data pre-processing solution in the sensor and machine learning algorithms in the cloud so as to detect critical wear.
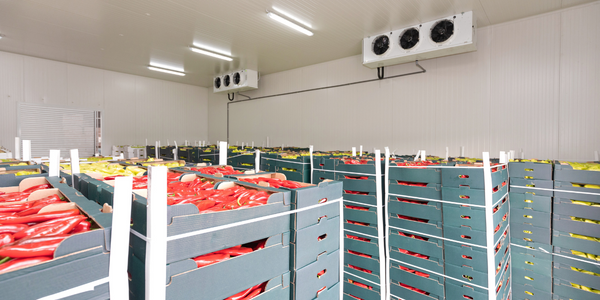
Case Study
Cold Chain Transportation and Refrigerated Fleet Management System
1) Create a digital connected transportation solution to retrofit cold chain trailers with real-time tracking and controls. 2) Prevent multi-million dollar losses due to theft or spoilage. 3) Deliver a digital chain-of-custody solution for door to door load monitoring and security. 4) Provide a trusted multi-fleet solution in a single application with granular data and access controls.