Company Size
200-1,000
Region
- America
Country
- Canada
- United States
Product
- Sage 100 ERP
- Sage 100 ERP e-Business Manager module
- Sage 100 ERP Bar Code module
- Sage 100 ERP Visual Integrator module
- Sage 100 ERP Paperless Office
Tech Stack
- ERP
- Bar Coding
- E-commerce
- Data Integration
Implementation Scale
- Enterprise-wide Deployment
Impact Metrics
- Cost Savings
- Productivity Improvements
- Revenue Growth
Technology Category
- Functional Applications - Enterprise Resource Planning Systems (ERP)
Applicable Functions
- Logistics & Transportation
- Warehouse & Inventory Management
Use Cases
- Inventory Management
- Supply Chain Visibility
- Warehouse Automation
Services
- System Integration
About The Customer
AM Appliance Group, Inc. is a North American wholesaler of high-end washers, dryers, and dishwashers from European manufacturers ASKO and Eurotech. The company was established in the late 1980s and has grown into a $75 million a year success. It supports 25 major distributors selling to appliance dealerships across the United States and Canada. The company maintains a physical warehouse primarily to house spare parts. It also uses a virtual warehouse to track the products in transit from European manufacturers. The majority of the company’s orders are drop shipped directly to its distributors. The company also provides distributors, dealers, and service centers with the spare parts required to make repairs.
The Challenge
AM Appliance Group, Inc. is a North American wholesaler of high-end washers, dryers, and dishwashers from European manufacturers ASKO and Eurotech. The company supports 25 major distributors selling to appliance dealerships across the United States and Canada. However, the company was struggling with its entry-level software which was not able to keep up with the company's growth. The software would often shut down during periods of peak usage and had to be restarted. The company was also struggling with its spare parts division which was outsourced to a parts distributor. This was both cumbersome and costly. The company was also struggling with tracking its orders in transit from European manufacturers. The company also had to manually process warranty claims which was time-consuming and inefficient.
The Solution
AM Appliance Group implemented the Sage 100 ERP solution to help it efficiently manage its accounting and operations. The Sage 100 ERP software allowed AM Appliance Group to bring its spare parts division entirely in-house. Parts are now stocked in the company’s warehouse, and orders are received electronically from the Sage 100 ERP e-Business Manager module running on AM Appliance Group’s web server. The Sage 100 ERP Bar Code module was used to streamline the company’s shipping process. Warehouse personnel equipped with handheld scanning devices scan the picking ticket and then scan the shelf tag, to verify that the proper item is selected. The data collected in the handheld is then uploaded into Sage 100 ERP, which creates an invoice for the items shipped. The company also uses Paperless Office, a Sage 100 ERP Extended Solution, to create Adobe PDF files of its invoices, statements, and orders. The PDFs are then emailed to customers and vendors. The company also uses the Sage 100 ERP Visual Integrator module to facilitate warranty processing.
Operational Impact
Quantitative Benefit
Case Study missing?
Start adding your own!
Register with your work email and create a new case study profile for your business.
Related Case Studies.

Case Study
Remote Temperature Monitoring of Perishable Goods Saves Money
RMONI was facing temperature monitoring challenges in a cold chain business. A cold chain must be established and maintained to ensure goods have been properly refrigerated during every step of the process, making temperature monitoring a critical business function. Manual registration practice can be very costly, labor intensive and prone to mistakes.
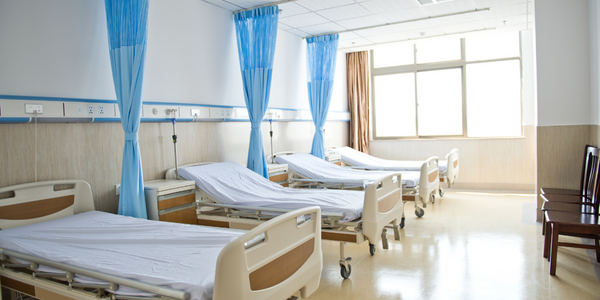
Case Study
Hospital Inventory Management
The hospital supply chain team is responsible for ensuring that the right medical supplies are readily available to clinicians when and where needed, and to do so in the most efficient manner possible. However, many of the systems and processes in use at the cancer center for supply chain management were not best suited to support these goals. Barcoding technology, a commonly used method for inventory management of medical supplies, is labor intensive, time consuming, does not provide real-time visibility into inventory levels and can be prone to error. Consequently, the lack of accurate and real-time visibility into inventory levels across multiple supply rooms in multiple hospital facilities creates additional inefficiency in the system causing over-ordering, hoarding, and wasted supplies. Other sources of waste and cost were also identified as candidates for improvement. Existing systems and processes did not provide adequate security for high-cost inventory within the hospital, which was another driver of cost. A lack of visibility into expiration dates for supplies resulted in supplies being wasted due to past expiry dates. Storage of supplies was also a key consideration given the location of the cancer center’s facilities in a dense urban setting, where space is always at a premium. In order to address the challenges outlined above, the hospital sought a solution that would provide real-time inventory information with high levels of accuracy, reduce the level of manual effort required and enable data driven decision making to ensure that the right supplies were readily available to clinicians in the right location at the right time.
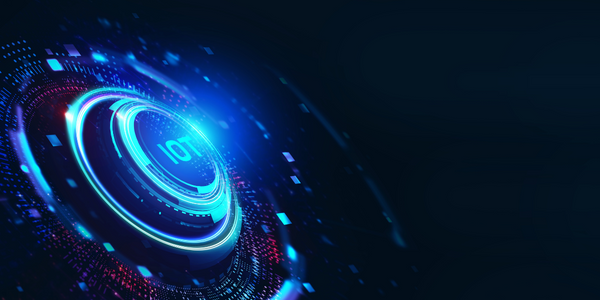
Case Study
IoT Solution for Cold Chain
Most of the customer's warehouses run on utility and generator power. Since these warehouses are in remote locations, power outages are a very common scenario. Diesel fuel, thereby, becomes a significant cost for these warehouses. Energy consumption was also very high due to the lack of a consistent temperature throughout the facility. This lack of a consistent temperature in all areas and no way to control it, resulted in the customer losing a significant amount of their temperature sensitive goods due to spoilage.