Company Size
11-200
Region
- America
Country
- United States
Product
- Sage 100 ERP
- Sage PFW ERP
Tech Stack
- ERP
Implementation Scale
- Enterprise-wide Deployment
Impact Metrics
- Customer Satisfaction
- Productivity Improvements
Technology Category
- Functional Applications - Enterprise Resource Planning Systems (ERP)
Applicable Industries
- Electronics
Applicable Functions
- Discrete Manufacturing
- Sales & Marketing
Use Cases
- Inventory Management
- Manufacturing System Automation
Services
- System Integration
About The Customer
OptoSigma is the United States subsidiary of Sigma Koki, a large Japanese optical component manufacturer. Since 1995, OptoSigma has been distributing highly specialized products to medical device manufacturers, testing firms, and research universities. The company bases its reputation on delivering exceptional products backed by a knowledgeable and responsive staff. OptoSigma is located in Santa Ana, California and operates from one location. The company is in the industry of Industrial Optical, Mechanical and Motorized Components.
The Challenge
OptoSigma had been using an older version of Sage PFW ERP which was no longer meeting its needs. The company was looking for a powerful, modern ERP solution that could meet all of its requirements. The company needed a solution that was intuitive to use, had strong inventory control capabilities, and bill of materials functionality. The company also wanted a solution that could be easily customized to match its workflow.
The Solution
OptoSigma migrated to Sage 100 ERP as part of a larger technology upgrade. Sage 100 ERP met all of the company’s requirements for its new ERP solution. It is intuitive to use, plus the screens can be easily customized to match the company's workflow. Most importantly, it has strong inventory control capabilities and bill of materials functionality. The company’s Sage business partner used the tools within Sage 100 ERP to import the company’s purchase order, sales order, payable, receivable, and inventory data into Sage 100 ERP. This enabled staff to work with actual business data from the start.
Operational Impact
Case Study missing?
Start adding your own!
Register with your work email and create a new case study profile for your business.
Related Case Studies.

Case Study
Remote Temperature Monitoring of Perishable Goods Saves Money
RMONI was facing temperature monitoring challenges in a cold chain business. A cold chain must be established and maintained to ensure goods have been properly refrigerated during every step of the process, making temperature monitoring a critical business function. Manual registration practice can be very costly, labor intensive and prone to mistakes.
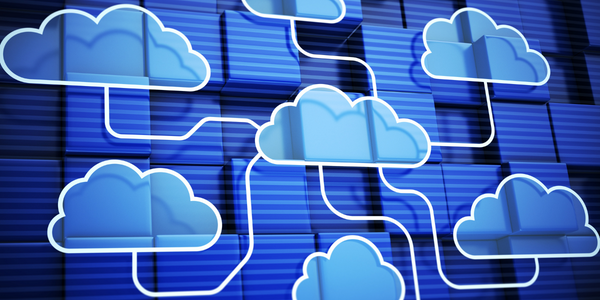
Case Study
Cloud Solution for Energy Management Platform-Schneider Electric
Schneider Electric required a cloud solution for its energy management platform to manage high computational operations, which were essential for catering to client requirements. As the business involves storage and analysis of huge amounts of data, the company also needed a convenient and scalable storage solution to facilitate operations efficiently.
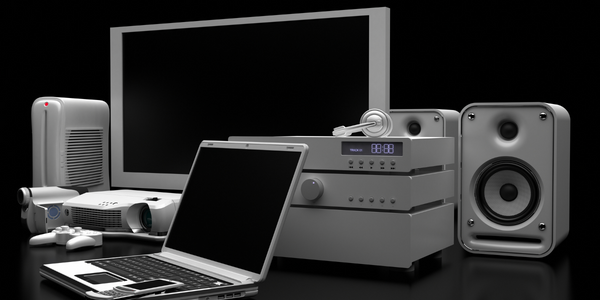
Case Study
Leveraging the IoT to Gain a Competitive Edge in International Competition
Many large manufacturers in and outside Japan are competing for larger market share in the same space, expecting a growing demand for projectors in the areas of entertainment, which requires glamor and strong visual performance as well as digital signage that can attract people’s attention. “It is becoming more and more difficult to differentiate ourselves with stand-alone hardware products,” says Kazuyuki Kitagawa, Director of Service & Support at Panasonic AVC Networks. “In order for Panasonic to grow market share and overall business, it is essential for us to develop solutions that deliver significant added value.” Panasonic believes projection failure and quality deterioration should never happen. This is what and has driven them to make their projectors IoT-enabled. More specifically, Panasonic has developed a system that collects data from projectors, visualizes detailed operational statuses, and predicts issues and address them before failure occurs. Their projectors are embedded with a variety of sensors that measure power supply, voltage, video input/ output signals, intake/exhaust air temperatures, cooling fan operations, and light bulb operating time. These sensors have been used to make the projector more intelligent, automatically suspending operation when the temperature rises excessively, and automatically switching light bulbs. Although this was a great first step, Panasonic projectors were still not equipped with any capability to send the data over a network.