Technology Category
- Analytics & Modeling - Digital Twin / Simulation
- Robots - Autonomous Guided Vehicles (AGV)
Applicable Industries
- Automotive
- Construction & Infrastructure
Applicable Functions
- Product Research & Development
- Quality Assurance
Use Cases
- Structural Health Monitoring
- Vehicle Performance Monitoring
Services
- Testing & Certification
About The Customer
Rimac Automobili is a technology company that develops and manufactures key electrification systems for global automotive companies. Founded in 2011 by CEO Mate Rimac, the company has an impressive list of clients ranging from automotive OEMs, tier one suppliers, and emerging players. In addition to providing innovative electric vehicle (EV) technology that meets environmental and safety regulations, Rimac has recently introduced a second generation of its own electric hypercar – Rimac C_Two. The company is headquartered on the outskirts of Zagreb, Croatia, and employs more than 600 people. Rimac’s development departments include eight structural CAE engineers who work with HyperWorks to support the structural design of the car.
The Challenge
Rimac Automobili, a leading developer and manufacturer of electrification systems for global automotive companies, faced a significant challenge in the structural design of the monocoque for the Rimac C-Two, the largest single carbon fiber part in the automotive industry. The main challenge was the material, a lightweight, carbon fiber reinforced with epoxy resin. As this carbon fiber is an orthotropic and brittle material, its representation in a finite element (FE) material card is very difficult. One of the most important parameters in designing EV is weight. The lighter the vehicle, the more increase in vehicle range which can lead to a higher acceptance of EV. Following a lightweight approach in the development process of their concept hypercar C_Two, the Rimac engineers were tasked to design the monocoque as a single carbon fiber part with an unprecedented size.
The Solution
To overcome this structural challenge, Rimac engineers utilized Altair HyperWorks. The goal was to achieve the closest correlation between real and virtual testing to minimize failure. The development process began with the part proposal and based on the results of the simulations run, the CAE team developed a proposal with design engineers. The model was then updated and tested again at each component level until the team saw perfect correlation between simulations and physical performance to achieve a design that performed as expected. The simulations performed by the vehicle engineering CAE design team involved 123 load cases. This was at component, system, and vehicle level, as well as linear, non-linear, static and dynamics simulations. The time frame for the whole development project was 5 months. In addition to providing software licenses and specialist support, Altair introduced HyperWorks Unlimited virtual appliance (HWUL-VA), which is part of the Altair innovative cloud offer.
Operational Impact
Quantitative Benefit
Case Study missing?
Start adding your own!
Register with your work email and create a new case study profile for your business.
Related Case Studies.

Case Study
IoT System for Tunnel Construction
The Zenitaka Corporation ('Zenitaka') has two major business areas: its architectural business focuses on structures such as government buildings, office buildings, and commercial facilities, while its civil engineering business is targeted at structures such as tunnels, bridges and dams. Within these areas, there presented two issues that have always persisted in regard to the construction of mountain tunnels. These issues are 'improving safety" and "reducing energy consumption". Mountain tunnels construction requires a massive amount of electricity. This is because there are many kinds of electrical equipment being used day and night, including construction machinery, construction lighting, and ventilating fan. Despite this, the amount of power consumption is generally not tightly managed. In many cases, the exact amount of power consumption is only ascertained when the bill from the power company becomes available. Sometimes, corporations install demand-monitoring equipment to help curb the maximum power demanded. However, even in these cases, the devices only allow the total volume of power consumption to be ascertained, or they may issue warnings to prevent the contracted volume of power from being exceeded. In order to tackle the issue of reducing power consumption, it was first necessary to obtain an accurate breakdown of how much power was being used in each particular area. In other words, we needed to be able to visualize the amount of power being consumed. Safety, was also not being managed very rigorously. Even now, tunnel construction sites often use a 'name label' system for managing entry into the work site. Specifically, red labels with white reverse sides that bear the workers' names on both sides are displayed at the tunnel work site entrance. The workers themselves then flip the name label to the appropriate side when entering or exiting from the work site to indicate whether or not they are working inside the tunnel at any given time. If a worker forgets to flip his or her name label when entering or exiting from the tunnel, management cannot be performed effectively. In order to tackle the challenges mentioned above, Zenitaka decided to build a system that could improve the safety of tunnel construction as well as reduce the amount of power consumed. In other words, this new system would facilitate a clear picture of which workers were working in each location at the mountain tunnel construction site, as well as which processes were being carried out at those respective locations at any given time. The system would maintain the safety of all workers while also carefully controlling the electrical equipment to reduce unnecessary power consumption. Having decided on the concept, our next concern was whether there existed any kind of robust hardware that would not break down at the construction work site, that could move freely in response to changes in the working environment, and that could accurately detect workers and vehicles using radio frequency identification (RFID). Given that this system would involve many components that were new to Zenitaka, we decided to enlist the cooperation of E.I.Sol Co., Ltd. ('E.I.Sol') as our joint development partner, as they had provided us with a highly practical proposal.
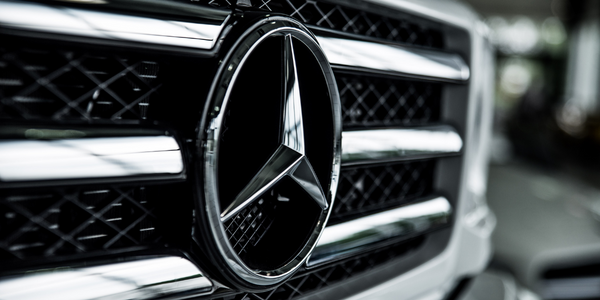
Case Study
Integral Plant Maintenance
Mercedes-Benz and his partner GAZ chose Siemens to be its maintenance partner at a new engine plant in Yaroslavl, Russia. The new plant offers a capacity to manufacture diesel engines for the Russian market, for locally produced Sprinter Classic. In addition to engines for the local market, the Yaroslavl plant will also produce spare parts. Mercedes-Benz Russia and his partner needed a service partner in order to ensure the operation of these lines in a maintenance partnership arrangement. The challenges included coordinating the entire maintenance management operation, in particular inspections, corrective and predictive maintenance activities, and the optimizing spare parts management. Siemens developed a customized maintenance solution that includes all electronic and mechanical maintenance activities (Integral Plant Maintenance).
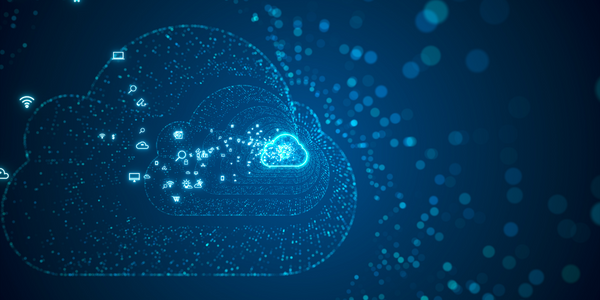
Case Study
Splunk Partnership Ties Together Big Data & IoT Services
Splunk was faced with the need to meet emerging customer demands for interfacing IoT projects to its suite of services. The company required an IoT partner that would be able to easily and quickly integrate with its Splunk Enterprise platform, rather than allocating development resources and time to building out an IoT interface and application platform.