Technology Category
- Sensors - Autonomous Driving Sensors
Applicable Industries
- Automotive
- Cement
Applicable Functions
- Product Research & Development
- Quality Assurance
Use Cases
- Experimentation Automation
- Time Sensitive Networking
Services
- Testing & Certification
About The Customer
American Railcar Industries, headquartered in St. Charles, Missouri, is a leading designer and manufacturer of commercial railroad cars. The company produces every part of the car above the wheels and its customers use these railcars to transport a wide variety of liquid and solid raw materials, including oil, coal, cement, sand, grain, and other substances. The company's designs include boxcars, gondolas, and hoppers, among other styles. Each design is tailored to the specific cargo it will carry, taking into account the unique properties and regulations associated with each material.
The Challenge
American Railcar Industries, a leading manufacturer of commercial railroad cars, was facing a significant challenge in modifying railcar designs. The company had to design state-of-the-art cars while considering the specific materials to be transported. For instance, designing a car to transport chlorine, a highly corrosive substance, required a robust design that complied with federal and state regulations. The company also had to ensure that the railcar was cost-competitive, which meant developing the least costly design that provided high levels of efficiency. The company had been using finite element analysis software for many years, but the limitations of that software had begun to slow their innovation processes. The company maintains base models for various types of cars, but each customer requires modifications to tailor the cars for the specific cargos they will carry. As a result, engineers had to re-run the model for different load cases. The company was also projecting an increase in projects involving structural dynamics, which were previously contracted out due to the lack of appropriate software.
The Solution
The company adopted HyperMesh, a pre-processing tool within Altair’s HyperWorks CAE suite, to overcome these challenges. HyperMesh offered an easy-to-use interface and advanced features that addressed the company's needs. When engineers needed to change the geometry of a car, the mesh updated quickly, eliminating the need to delete and re-mesh. Moreover, the same set of HyperWorks units could be used for any software tool in the suite or offered by the Altair Partner Alliance. This meant that if a fluid dynamics analysis was needed, there was no need to purchase additional software. The company also started using MotionSolve to design mechanisms, eliminating the need to contract out the analysis to someone else. The company is now considering the use of HyperCrash to develop models that accurately indicate the behavior of various types of cargo when the railcar experiences an impact.
Operational Impact
Quantitative Benefit
Case Study missing?
Start adding your own!
Register with your work email and create a new case study profile for your business.
Related Case Studies.

Case Study
System 800xA at Indian Cement Plants
Chettinad Cement recognized that further efficiencies could be achieved in its cement manufacturing process. It looked to investing in comprehensive operational and control technologies to manage and derive productivity and energy efficiency gains from the assets on Line 2, their second plant in India.
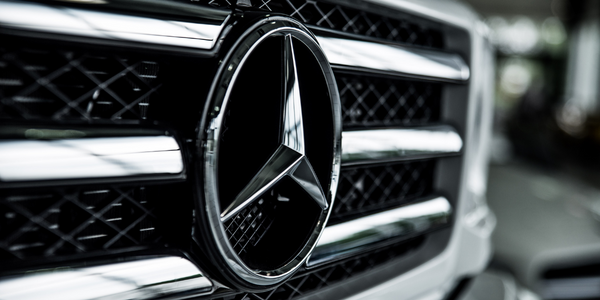
Case Study
Integral Plant Maintenance
Mercedes-Benz and his partner GAZ chose Siemens to be its maintenance partner at a new engine plant in Yaroslavl, Russia. The new plant offers a capacity to manufacture diesel engines for the Russian market, for locally produced Sprinter Classic. In addition to engines for the local market, the Yaroslavl plant will also produce spare parts. Mercedes-Benz Russia and his partner needed a service partner in order to ensure the operation of these lines in a maintenance partnership arrangement. The challenges included coordinating the entire maintenance management operation, in particular inspections, corrective and predictive maintenance activities, and the optimizing spare parts management. Siemens developed a customized maintenance solution that includes all electronic and mechanical maintenance activities (Integral Plant Maintenance).
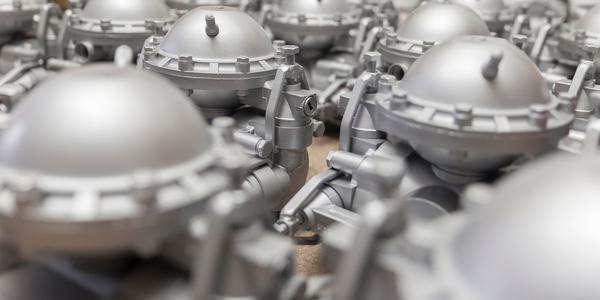
Case Study
Monitoring of Pressure Pumps in Automotive Industry
A large German/American producer of auto parts uses high-pressure pumps to deburr machined parts as a part of its production and quality check process. They decided to monitor these pumps to make sure they work properly and that they can see any indications leading to a potential failure before it affects their process.