Technology Category
- Analytics & Modeling - Robotic Process Automation (RPA)
- Functional Applications - Enterprise Resource Planning Systems (ERP)
Applicable Industries
- Education
- Equipment & Machinery
Applicable Functions
- Product Research & Development
Use Cases
- Time Sensitive Networking
- Virtual Training
Services
- Hardware Design & Engineering Services
- Training
About The Customer
The customer is a large industrial services company based in Australia. The company operates in the construction and building materials industry and machinery sector. It has thousands of employees and was struggling with slow, labor-intensive processes that were impacting its growth. The company had tried to automate its processes using traditional .NET development but found the existing systems to be problematic and time-consuming. After six months of unproductive efforts, the company decided to look for a better solution and implemented Nintex K2 Five, an intelligent automation software.
The Challenge
An Australia-based industrial services company was struggling with slow, labor-intensive processes that were hampering its growth. The company had attempted to automate its workflows using traditional .NET development, but the results were unsatisfactory. The existing systems were not only time-consuming but also prone to errors and difficult to troubleshoot. For instance, employees had to individually submit training requests, chase approvals, and gather additional supporting information for each step. After six months of unproductive efforts, the company decided to abandon its .NET attempts and look for a better solution.
The Solution
The company decided to implement Nintex K2 Five, an intelligent automation software. One employee was able to completely recreate its training request form and equipment movements and disposal (EMD) process using this software. The training request workflows were completely reinvented, making the previously time-consuming task instantly efficient. The software was integrated with the company’s existing systems, allowing all requests to be approved by the relevant managers while simultaneously collecting supporting material and submitting it for processing. The EMD workflows were also simplified as Nintex K2 Five seamlessly integrated with the company’s enterprise resource planning (ERP) system. This allowed the staff to easily notify all relevant stakeholders on the listing and status of any asset. The new solution also enabled real-time actioning of modifications for improved hardware requests and system access forms.
Operational Impact
Quantitative Benefit
Case Study missing?
Start adding your own!
Register with your work email and create a new case study profile for your business.
Related Case Studies.

Case Study
Smart Water Filtration Systems
Before working with Ayla Networks, Ozner was already using cloud connectivity to identify and solve water-filtration system malfunctions as well as to monitor filter cartridges for replacements.But, in June 2015, Ozner executives talked with Ayla about how the company might further improve its water systems with IoT technology. They liked what they heard from Ayla, but the executives needed to be sure that Ayla’s Agile IoT Platform provided the security and reliability Ozner required.

Case Study
IoT enabled Fleet Management with MindSphere
In view of growing competition, Gämmerler had a strong need to remain competitive via process optimization, reliability and gentle handling of printed products, even at highest press speeds. In addition, a digitalization initiative also included developing a key differentiation via data-driven services offers.
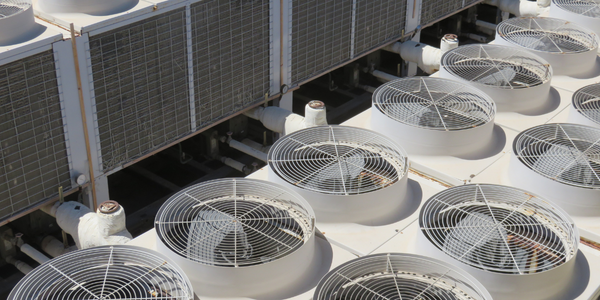
Case Study
Predictive Maintenance for Industrial Chillers
For global leaders in the industrial chiller manufacturing, reliability of the entire production process is of the utmost importance. Chillers are refrigeration systems that produce ice water to provide cooling for a process or industrial application. One of those leaders sought a way to respond to asset performance issues, even before they occur. The intelligence to guarantee maximum reliability of cooling devices is embedded (pre-alarming). A pre-alarming phase means that the cooling device still works, but symptoms may appear, telling manufacturers that a failure is likely to occur in the near future. Chillers who are not internet connected at that moment, provide little insight in this pre-alarming phase.

Case Study
Premium Appliance Producer Innovates with Internet of Everything
Sub-Zero faced the largest product launch in the company’s history:It wanted to launch 60 new products as scheduled while simultaneously opening a new “greenfield” production facility, yet still adhering to stringent quality requirements and manage issues from new supply-chain partners. A the same time, it wanted to increase staff productivity time and collaboration while reducing travel and costs.

Case Study
Integration of PLC with IoT for Bosch Rexroth
The application arises from the need to monitor and anticipate the problems of one or more machines managed by a PLC. These problems, often resulting from the accumulation over time of small discrepancies, require, when they occur, ex post technical operations maintenance.
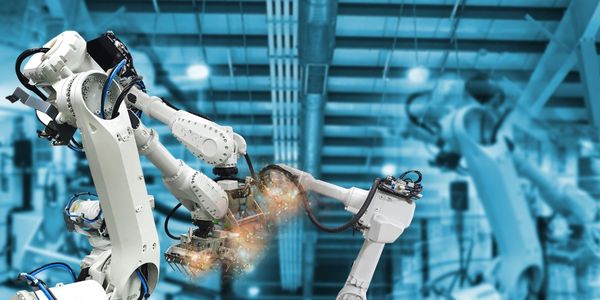
Case Study
Robot Saves Money and Time for US Custom Molding Company
Injection Technology (Itech) is a custom molder for a variety of clients that require precision plastic parts for such products as electric meter covers, dental appliance cases and spools. With 95 employees operating 23 molding machines in a 30,000 square foot plant, Itech wanted to reduce man hours and increase efficiency.