Restech's Transition to Qualio's eQMS for Enhanced Quality Management
Company Size
11-200
Region
- America
Country
- United States
Product
- Qualio
Tech Stack
- Electronic Quality Management System (eQMS)
- Salesforce Integration
Implementation Scale
- Enterprise-wide Deployment
Impact Metrics
- Customer Satisfaction
- Digital Expertise
- Productivity Improvements
Technology Category
- Functional Applications - Computerized Maintenance Management Systems (CMMS)
- Functional Applications - Enterprise Resource Planning Systems (ERP)
Applicable Industries
- Healthcare & Hospitals
Applicable Functions
- Business Operation
- Quality Assurance
Services
- System Integration
- Training
About The Customer
Restech is a medical device company specializing in the production of devices for minimally invasive diagnosis and treatment of reflux disorders. The company has experienced impressive growth and operates in multiple international territories. To support its operations and ensure compliance with various regulations such as FDA 21 CFR 820, ISO 13485, CGMP, EU MDR, and UK Medical Device Regulations, Restech required a carefully constructed Quality Management System (QMS). The company's commitment to quality and regulatory compliance is evident in its adoption of advanced quality management solutions.
The Challenge
Restech and its Director of Quality Assurance, Lowell Hoffman, faced significant challenges with their manual, paper-based quality management system (QMS). The old system was labor-intensive, time-consuming, and prone to human errors. Document control was particularly problematic, with local saving of document copies preventing access to centralized, up-to-date information. The process of creating paper folders and collecting wet signatures was also time-demanding. These inefficiencies hindered Restech's ability to maintain strong document control, which is crucial for a robust QMS, especially in the medical device industry where regulatory compliance is stringent.
The Solution
To address these challenges, Restech decided to adopt an electronic quality management system (eQMS). After evaluating various options, Lowell Hoffman and the senior management team chose Qualio as the optimal platform. The decision was based on several criteria, including cost, ease of use, look and feel, ease of setup and transfer from the old QMS, and long-term customer support. Qualio's eQMS provided a comprehensive solution that eliminated the administrative burden of the paper-based system. It streamlined document control processes, reduced the time required for document updates, and minimized human errors. Additionally, Qualio's digital workflows for managing quality events like CAPAs and deviations significantly improved efficiency.
Operational Impact
Quantitative Benefit
Case Study missing?
Start adding your own!
Register with your work email and create a new case study profile for your business.
Related Case Studies.
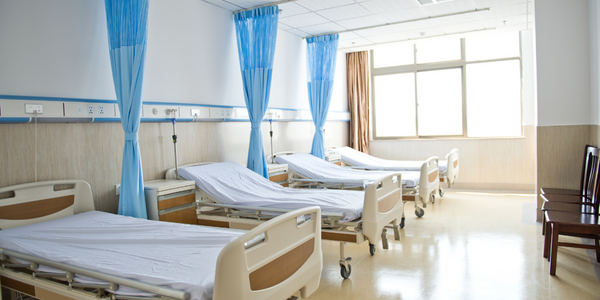
Case Study
Hospital Inventory Management
The hospital supply chain team is responsible for ensuring that the right medical supplies are readily available to clinicians when and where needed, and to do so in the most efficient manner possible. However, many of the systems and processes in use at the cancer center for supply chain management were not best suited to support these goals. Barcoding technology, a commonly used method for inventory management of medical supplies, is labor intensive, time consuming, does not provide real-time visibility into inventory levels and can be prone to error. Consequently, the lack of accurate and real-time visibility into inventory levels across multiple supply rooms in multiple hospital facilities creates additional inefficiency in the system causing over-ordering, hoarding, and wasted supplies. Other sources of waste and cost were also identified as candidates for improvement. Existing systems and processes did not provide adequate security for high-cost inventory within the hospital, which was another driver of cost. A lack of visibility into expiration dates for supplies resulted in supplies being wasted due to past expiry dates. Storage of supplies was also a key consideration given the location of the cancer center’s facilities in a dense urban setting, where space is always at a premium. In order to address the challenges outlined above, the hospital sought a solution that would provide real-time inventory information with high levels of accuracy, reduce the level of manual effort required and enable data driven decision making to ensure that the right supplies were readily available to clinicians in the right location at the right time.
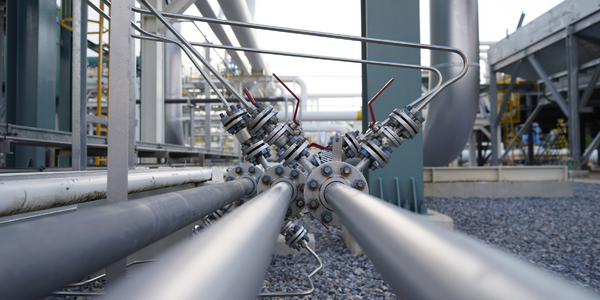
Case Study
Gas Pipeline Monitoring System for Hospitals
This system integrator focuses on providing centralized gas pipeline monitoring systems for hospitals. The service they provide makes it possible for hospitals to reduce both maintenance and labor costs. Since hospitals may not have an existing network suitable for this type of system, GPRS communication provides an easy and ready-to-use solution for remote, distributed monitoring systems System Requirements - GPRS communication - Seamless connection with SCADA software - Simple, front-end control capability - Expandable I/O channels - Combine AI, DI, and DO channels
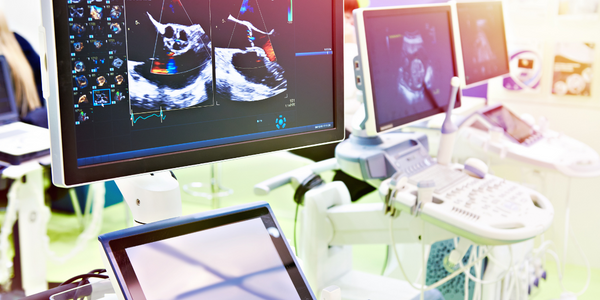
Case Study
Driving Digital Transformations for Vitro Diagnostic Medical Devices
Diagnostic devices play a vital role in helping to improve healthcare delivery. In fact, an estimated 60 percent of the world’s medical decisions are made with support from in vitrodiagnostics (IVD) solutions, such as those provided by Roche Diagnostics, an industry leader. As the demand for medical diagnostic services grows rapidly in hospitals and clinics across China, so does the market for IVD solutions. In addition, the typically high cost of these diagnostic devices means that comprehensive post-sales services are needed. Wanteed to improve three portions of thr IVD:1. Remotely monitor and manage IVD devices as fixed assets.2. Optimizing device availability with predictive maintenance.3. Recommending the best IVD solution for a customer’s needs.
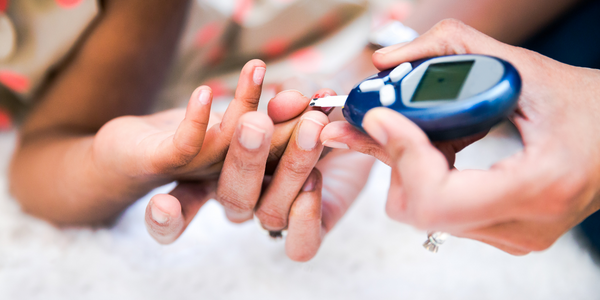
Case Study
HaemoCloud Global Blood Management System
1) Deliver a connected digital product system to protect and increase the differentiated value of Haemonetics blood and plasma solutions. 2) Improve patient outcomes by increasing the efficiency of blood supply flows. 3) Navigate and satisfy a complex web of global regulatory compliance requirements. 4) Reduce costly and labor-intensive maintenance procedures.
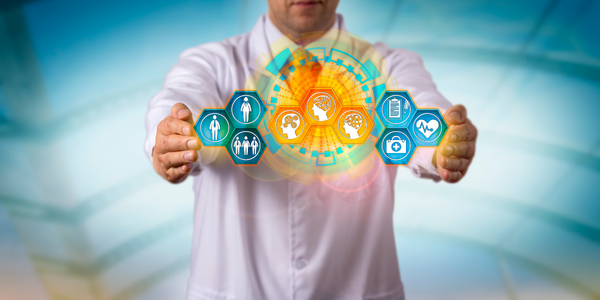
Case Study
Harnessing real-time data to give a holistic picture of patient health
Every day, vast quantities of data are collected about patients as they pass through health service organizations—from operational data such as treatment history and medications to physiological data captured by medical devices. The insights hidden within this treasure trove of data can be used to support more personalized treatments, more accurate diagnosis and more advanced preparative care. But since the information is generated faster than most organizations can consume it, unlocking the power of this big data can be a struggle. This type of predictive approach not only improves patient care—it also helps to reduce costs, because in the healthcare industry, prevention is almost always more cost-effective than treatment. However, collecting, analyzing and presenting these data-streams in a way that clinicians can easily understand can pose a significant technical challenge.