Customer Company Size
Large Corporate
Region
- Europe
- Asia
- America
Country
- France
- Romania
- India
- Korea
- Spain
Product
- Dassault Systemes’ Version 6 PLM platform
- 3DLive
- CATIA V6
Tech Stack
- PLM
- 3D collaboration
- Data Management
Implementation Scale
- Enterprise-wide Deployment
Impact Metrics
- Productivity Improvements
- Cost Savings
- Digital Expertise
Technology Category
- Platform as a Service (PaaS) - Application Development Platforms
- Application Infrastructure & Middleware - Data Exchange & Integration
Applicable Industries
- Automotive
Applicable Functions
- Product Research & Development
- Quality Assurance
Use Cases
- Manufacturing System Automation
- Predictive Maintenance
- Digital Twin
Services
- Software Design & Engineering Services
- System Integration
About The Customer
Renault is a global automotive company that aims to bring high quality, affordable vehicles that meet the market’s expectations for advances in customer experience and environmental responsibility. The company has more than 40% of its engineers located outside of France in “technocentres” in Romania, India, Korea, South America and Spain. Renault is committed to delivering on these challenges and setting itself clearly apart from its competitors. To achieve its strategic growth plans, Renault needs to ensure its performance in R&D and investments. That performance depends on reducing development cycle times and standardizing the components it develops.
The Challenge
Renault, a global automotive company, was seeking an enterprise-wide PLM solution that would effectively address issues of standardization for its processes and design tools. With more than 40% of its engineers located outside of France in “technocentres” in Romania, India, Korea, South America and Spain, the company needed a global engineering tool that would allow its designers to effectively and efficiently collaborate around the globe. Renault also sought a solution that would allow it to easily access and manage all of the company’s data – from product design and process to simulation, testing and resources information – while ensuring its traceability. The company wanted a single PDM that could be deployed worldwide to cover all of Renault’s needs for data management across product, process, simulation and performance.
The Solution
Renault chose Dassault Systemes’ Version 6 PLM platform as the cornerstone of its global automotive engineering processes to support an internal program called NewPDM. Version 6 met these requirements, while offering a strong dose of ergonomics over older systems. It was important for Renault to simplify 3D navigation through a vehicle or engine that allowed access to all of its engineering documents or deliverables. Through Renault’s Quick Win deployment approach the company has been able to implement 3D collaboration with 3DLive among its sites. A single database prevents problems with data reconciliation. Document management also is vastly improved with Version 6. With Version 6, Renault will have full traceability of all of its deliverables. The documents are easily accessible and, in some cases, even rework is avoided, since at any moment you can refer to past studies and transmit know-how and results to downstream teams.
Operational Impact
Quantitative Benefit
Case Study missing?
Start adding your own!
Register with your work email and create a new case study profile for your business.
Related Case Studies.
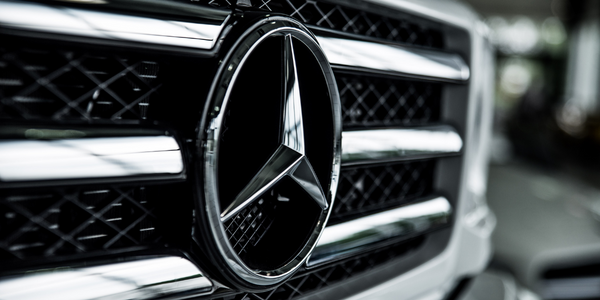
Case Study
Integral Plant Maintenance
Mercedes-Benz and his partner GAZ chose Siemens to be its maintenance partner at a new engine plant in Yaroslavl, Russia. The new plant offers a capacity to manufacture diesel engines for the Russian market, for locally produced Sprinter Classic. In addition to engines for the local market, the Yaroslavl plant will also produce spare parts. Mercedes-Benz Russia and his partner needed a service partner in order to ensure the operation of these lines in a maintenance partnership arrangement. The challenges included coordinating the entire maintenance management operation, in particular inspections, corrective and predictive maintenance activities, and the optimizing spare parts management. Siemens developed a customized maintenance solution that includes all electronic and mechanical maintenance activities (Integral Plant Maintenance).
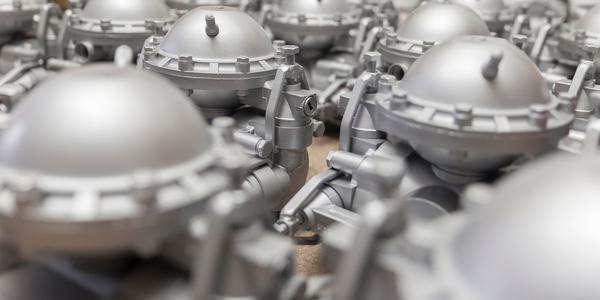
Case Study
Monitoring of Pressure Pumps in Automotive Industry
A large German/American producer of auto parts uses high-pressure pumps to deburr machined parts as a part of its production and quality check process. They decided to monitor these pumps to make sure they work properly and that they can see any indications leading to a potential failure before it affects their process.