Renault Automaker uses LMS Imagine.Lab Amesim to optimize design of electrical systems early in the development cycle
Company Size
1,000+
Region
- Europe
Country
- France
Product
- LMS Imagine.Lab Amesim
- Simulink
Tech Stack
- Multi-domain simulation software
- Numerical solver
- Hardware-in-the-loop platforms
Implementation Scale
- Enterprise-wide Deployment
Impact Metrics
- Cost Savings
- Customer Satisfaction
- Productivity Improvements
Technology Category
- Analytics & Modeling - Predictive Analytics
- Functional Applications - Remote Monitoring & Control Systems
- Platform as a Service (PaaS) - Connectivity Platforms
Applicable Industries
- Automotive
Applicable Functions
- Product Research & Development
- Quality Assurance
Use Cases
- Energy Management System
- Predictive Maintenance
- Remote Asset Management
Services
- Software Design & Engineering Services
- System Integration
About The Customer
Renault is a French multinational vehicle manufacturer that was established in 1899. The company produces a range of cars and vans and employs over 127,000 people. Renault has a significant global presence, operating in 128 countries. Known for its innovation and commitment to quality, Renault has been a key player in the automotive industry for over a century. The company has continually adapted to changing market demands and technological advancements, making it a leader in the development of energy-efficient and environmentally friendly vehicles. Renault's commitment to sustainability and innovation is evident in its efforts to optimize electrical systems in its vehicles, aiming to reduce power consumption and improve energy management.
The Challenge
Electric power consumption in automobiles has risen significantly over the last decades. In the near future, even greater electrical power requirements are expected. To limit the associated increase in fuel consumption and exhaust emissions, new strategies for the generation, storage, retrieval, distribution, and consumption of electric power are needed. The challenge that arises now is how to control the power net to obtain maximum energy efficiency within the vehicle. One of the main causes of increased electric consumption is the replacement of mechanical and hydraulic components with electrical devices. The increase in electrical consumption affects the testing and simulation process. In the 1990s, statistical modeling was carried out to monitor various driving cycles in different weather conditions. These experiments could provide the mean value and peak request for electric power. During the development process, the designer could select the appropriate battery and alternator to meet the electric requirements of the vehicle. To be on the safe side, several physical tests had to be done in order to confirm the choice. The trend to shorter development cycles and, therefore, performing fewer tests, really began early in the 21st century. At that time, Renault decided to replace actual testing by virtual validation for selected driving cycles. To minimize electric consumption, emphasis was placed on optimizing the battery and alternator selection by taking into account additional dynamics and using more precise models.
The Solution
To overcome the limitations of their in-house simulation tool, Renault benchmarked several simulation tools and selected LMS Imagine.Lab Amesim from Siemens PLM Software. This tool was chosen because it is a true multi-domain simulation software package with an excellent numerical solver. LMS Amesim is accurate, reliable, and five times faster than Renault's previous in-house tool for the same analysis. The software is fully compatible with Renault's Simulink environment and hardware-in-the-loop platforms, making it easier to share models with other teams. Today, LMS Amesim is used at Renault for precision sizing of the battery and alternator, including worst-case scenario startup validation. Control strategies are optimized as well, allowing advanced voltage control strategies to be evaluated. For example, when power is requested from the combustion engine, circuit voltage can be decreased. The overall objective is to help designers optimize the concept of the electrical systems earlier in the development cycle, reducing physical tests and avoiding late design changes. LMS Amesim also helps reduce electrical power consumption by optimizing energy management, specifically the control laws implemented in the electronics module.
Operational Impact
Quantitative Benefit
Case Study missing?
Start adding your own!
Register with your work email and create a new case study profile for your business.
Related Case Studies.
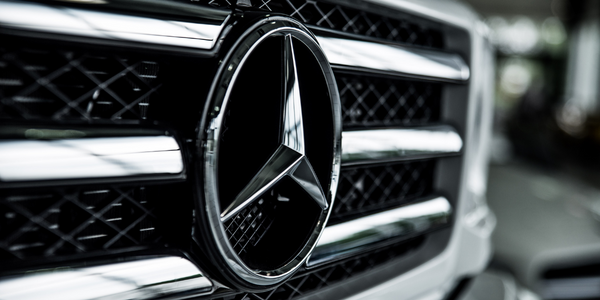
Case Study
Integral Plant Maintenance
Mercedes-Benz and his partner GAZ chose Siemens to be its maintenance partner at a new engine plant in Yaroslavl, Russia. The new plant offers a capacity to manufacture diesel engines for the Russian market, for locally produced Sprinter Classic. In addition to engines for the local market, the Yaroslavl plant will also produce spare parts. Mercedes-Benz Russia and his partner needed a service partner in order to ensure the operation of these lines in a maintenance partnership arrangement. The challenges included coordinating the entire maintenance management operation, in particular inspections, corrective and predictive maintenance activities, and the optimizing spare parts management. Siemens developed a customized maintenance solution that includes all electronic and mechanical maintenance activities (Integral Plant Maintenance).
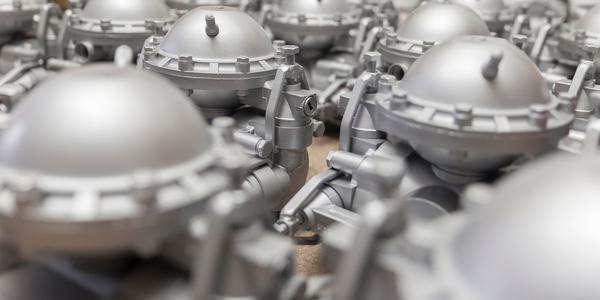
Case Study
Monitoring of Pressure Pumps in Automotive Industry
A large German/American producer of auto parts uses high-pressure pumps to deburr machined parts as a part of its production and quality check process. They decided to monitor these pumps to make sure they work properly and that they can see any indications leading to a potential failure before it affects their process.