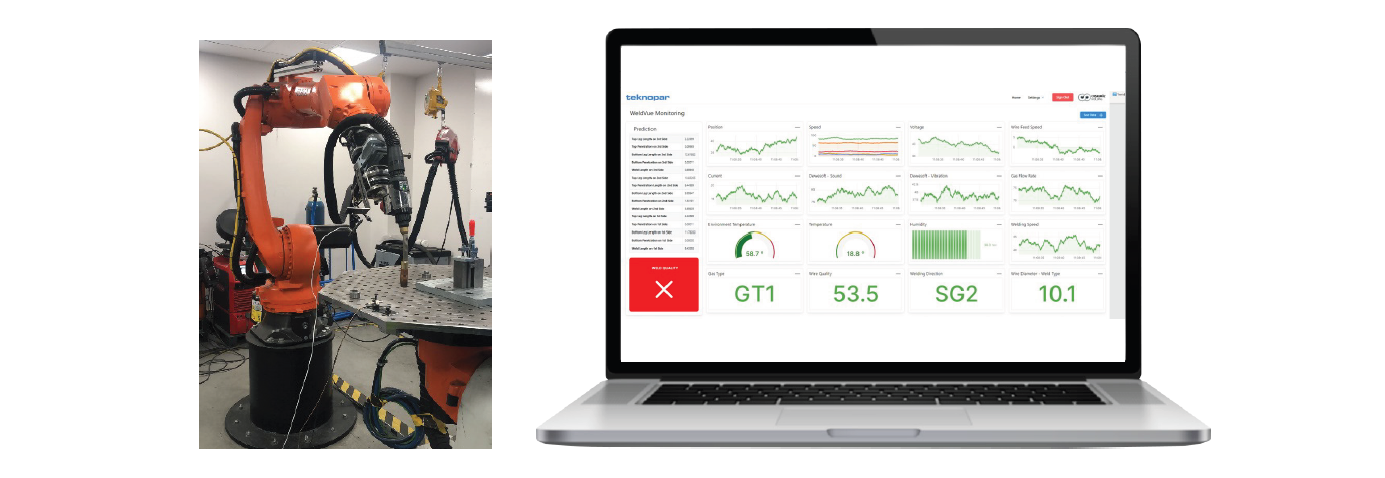
- Analytics & Modeling - Digital Twin / Simulation
- Analytics & Modeling - Predictive Analytics
- Equipment & Machinery
- Metals
- Discrete Manufacturing
- Condition Monitoring
- Digital Twin
- Predictive Maintenance
- Predictive Quality Analytics
- Data Science Services
- Software Design & Engineering Services
- System Integration
Manufacturing of pressed sheet metal parts in the automotive industry.
Automating welding processes with robots enhances productivity and environmental friendliness. However, the quality of robotic welding can deteriorate due to various factory conditions. Continuous monitoring and adjustments are necessary to maintain high standards.
TEKNOPAR integrated data from multiple sensors, including microphone and vibration sensors, environmental sensors, fiberoptic laser sensors, and Magmaweld devices, to create a comprehensive real-time monitoring system. Advanced regression models analyzed these data streams to detect potential quality issues, allowing immediate adjustments to the robot's parameters.
Case Study missing?
Start adding your own!
Register with your work email and create a new case study profile for your business.
Related Case Studies.


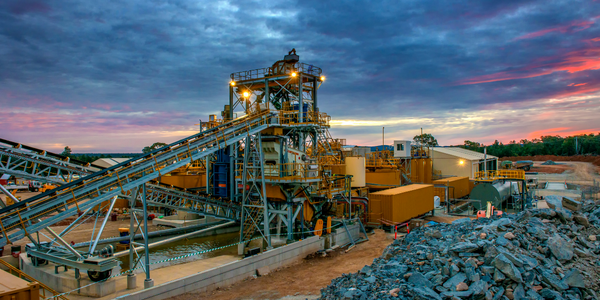
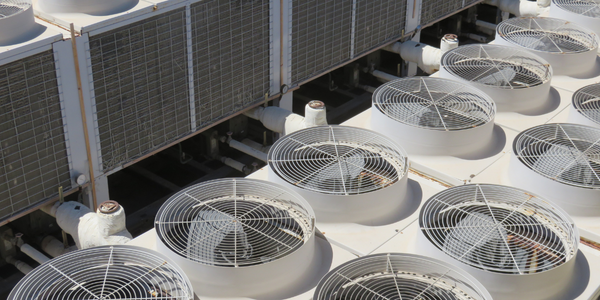

