Technology Category
- Analytics & Modeling - Predictive Analytics
- Cybersecurity & Privacy - Security Compliance
Applicable Industries
- Equipment & Machinery
- Transportation
Applicable Functions
- Logistics & Transportation
- Quality Assurance
Use Cases
- Leasing Finance Automation
- Supply Chain Visibility
Services
- Testing & Certification
About The Customer
The customer is a well-known chocolate and confectionary giant with a complex supply chain. The company's supply chain involves transporting and processing cocoa, production, and further transportation to retailers and customers worldwide. The company primarily uses active cooling Full-Truckload (FTL) transport to move chocolates from the manufacturing unit to depots using domestic transportation. This process involves several transporters, making quality compliance both essential and complex. The company was facing significant challenges in its supply chain, including breaches in quality compliance and a lack of actionable information due to delayed, inaccurate, and sometimes inaccessible data from transporters.
The Challenge
A renowned chocolate and confectionary company was facing significant challenges in its supply chain. The company's primary goal was to monitor their active cooling Full-Truckload (FTL) transport, which moved chocolates from the manufacturing unit to depots using domestic transportation. This process involved several transporters, making quality compliance both essential and complex. The company was struggling with two main challenges. The first was a breach in quality compliance. The company noticed spoilage in some of their consignments, but the data from their 3PLs was delayed, second-hand, inaccurate, and unverifiable. Many packages were reaching the destination spoiled due to unchecked temperature excursions. The second challenge was the lack of actionable information. The company depended on vendors and transporters for data, but the data was often delayed, inaccurate, and sometimes even inaccessible. The company was unable to make timely decisions due to the lack of real-time visibility on the shipment’s location and condition.
The Solution
The company partnered with Roambee to address their supply chain challenges. Roambee provided an innovative solution that included a 24x7 supply chain control tower, transporter effort, and company point-of-contact effort. This three-part approach helped the company get verifiable real-time location and condition data and use intelligent data analytics for better logistics decisions. The solution worked on identifying anomalies and collaborating with transporters with the support of the company's logistics team. Roambee's solution gave the customer the leverage to place devices anywhere, ensuring that accurate temperature is reported even at hotspots. The solution included battery-powered sensor devices placed in the truck for real-time temperature data, timely pre-emptive alerts for quick actions on anomalies, and a 24x7 control tower to ensure improved compliance from transporters and 3PLs. The company moved from second-hand, delayed, and inaccurate compliance data to first-hand, live, and actionable compliance data.
Operational Impact
Quantitative Benefit
Case Study missing?
Start adding your own!
Register with your work email and create a new case study profile for your business.
Related Case Studies.

Case Study
Smart Water Filtration Systems
Before working with Ayla Networks, Ozner was already using cloud connectivity to identify and solve water-filtration system malfunctions as well as to monitor filter cartridges for replacements.But, in June 2015, Ozner executives talked with Ayla about how the company might further improve its water systems with IoT technology. They liked what they heard from Ayla, but the executives needed to be sure that Ayla’s Agile IoT Platform provided the security and reliability Ozner required.

Case Study
IoT enabled Fleet Management with MindSphere
In view of growing competition, Gämmerler had a strong need to remain competitive via process optimization, reliability and gentle handling of printed products, even at highest press speeds. In addition, a digitalization initiative also included developing a key differentiation via data-driven services offers.
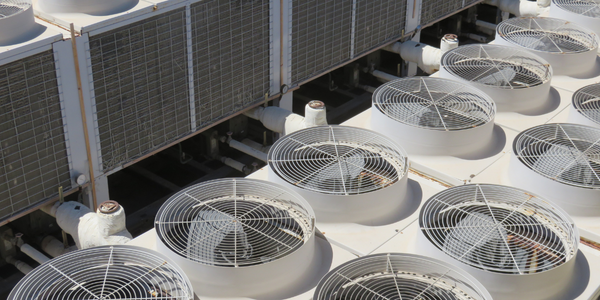
Case Study
Predictive Maintenance for Industrial Chillers
For global leaders in the industrial chiller manufacturing, reliability of the entire production process is of the utmost importance. Chillers are refrigeration systems that produce ice water to provide cooling for a process or industrial application. One of those leaders sought a way to respond to asset performance issues, even before they occur. The intelligence to guarantee maximum reliability of cooling devices is embedded (pre-alarming). A pre-alarming phase means that the cooling device still works, but symptoms may appear, telling manufacturers that a failure is likely to occur in the near future. Chillers who are not internet connected at that moment, provide little insight in this pre-alarming phase.

Case Study
Premium Appliance Producer Innovates with Internet of Everything
Sub-Zero faced the largest product launch in the company’s history:It wanted to launch 60 new products as scheduled while simultaneously opening a new “greenfield” production facility, yet still adhering to stringent quality requirements and manage issues from new supply-chain partners. A the same time, it wanted to increase staff productivity time and collaboration while reducing travel and costs.

Case Study
Integration of PLC with IoT for Bosch Rexroth
The application arises from the need to monitor and anticipate the problems of one or more machines managed by a PLC. These problems, often resulting from the accumulation over time of small discrepancies, require, when they occur, ex post technical operations maintenance.
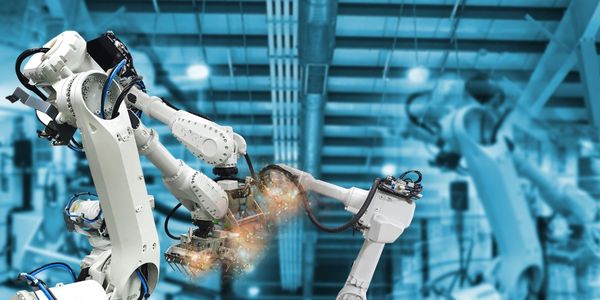
Case Study
Robot Saves Money and Time for US Custom Molding Company
Injection Technology (Itech) is a custom molder for a variety of clients that require precision plastic parts for such products as electric meter covers, dental appliance cases and spools. With 95 employees operating 23 molding machines in a 30,000 square foot plant, Itech wanted to reduce man hours and increase efficiency.