Real Time Fab Monitoring At A High Volume Semiconductor Back-End
Customer Company Size
Large Corporate
Region
- Asia
Country
- China
Product
- CMNavigo
Tech Stack
- Microsoft Silverlight
Implementation Scale
- Enterprise-wide Deployment
Impact Metrics
- Productivity Improvements
- Digital Expertise
Technology Category
- Application Infrastructure & Middleware - API Integration & Management
Applicable Industries
- Semiconductors
Applicable Functions
- Discrete Manufacturing
Use Cases
- Real-Time Location System (RTLS)
- Factory Operations Visibility & Intelligence
Services
- System Integration
About The Customer
The customer is a company founded in the 1980s and is one of the world's largest providers of semiconductor manufacturing assembly and test services. The company operates a high-volume manufacturing site in China that consists of several buildings with multiple production floors per building and with several thousand processing equipment in total. The company's operations are large-scale, requiring a solution that can handle the volume and complexity of its operations. The company also has a specific equipment state model that consists of six main states with approximately one hundred sub-states.
The Challenge
The company, one of the world's largest providers of semiconductor manufacturing assembly and test services, was facing challenges in tracking, monitoring, and optimizing the utilization of its several thousand processing equipment in its high-volume manufacturing site in China. The main requirements were to capture equipment status and historical information automatically for real-time knowledge and performance analysis over time, and to visualize the status of all the equipment in real-time in a graphical manner representing the actual physical fab layout. The large scale of the operation necessitated a solution that was scalable, flexible, and had state-of-the-art visualization and reporting capabilities.
The Solution
To address the challenges, the company selected a Next Generation Manufacturing Execution System which provided Equipment Tracking and Real Time Graphical Fab Monitoring capabilities. The solution, CMNavigo, is functionally comprehensive, unified, and integrated, leveraging the latest hardware and software technologies to implement open, scalable, flexible, and extensible shop floor control systems. The implementation of the solution consisted mainly in the configuration of the Equipment Tracking and Real Time Graphical Fab Monitor modules of CMNavigo and an equipment integration module to supply the MES with real-time events from the equipment. The company also used the design module of CMNavigo to draw multiple layouts representing the real physical layout of the fab.
Operational Impact
Case Study missing?
Start adding your own!
Register with your work email and create a new case study profile for your business.
Related Case Studies.
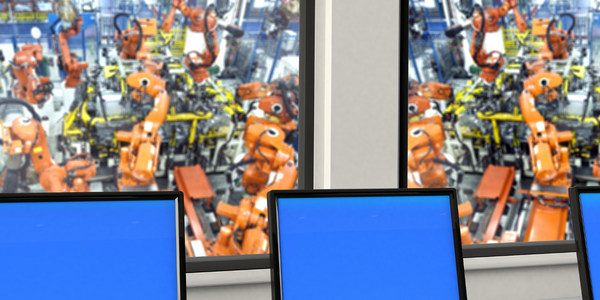
Case Study
KINESYS Semiconductor Factory Automation Software
KINESYS Software provides both Integrated Device Manufacturer (IDM) and Original Equipment Manufacturer (OEM) customers world-class software products and solutions for advanced wafer and device traceability and process management. KINESYS offers state of the art database technology with a core focus on SEMI standards. KINESYS’ challenge was to make back-end processing failure-free and easy to use for clients while supporting licensing models more adaptable to changing industry needs.
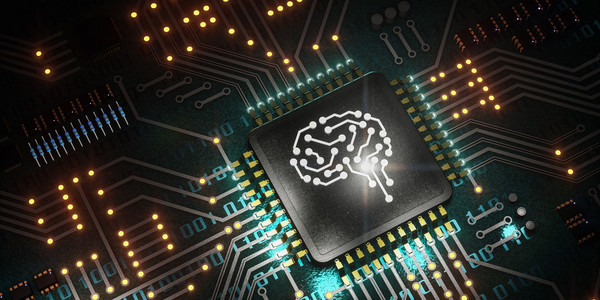
Case Study
Modular AI Defect Inspection Solution for Efficient Semiconductor Equipment Upgrades
Smasoft Technology Co., Ltd., a System Integrator that develops industrial automation software and offers AI application solutions, was commissioned by a semiconductor equipment manufacturer to implement AI inspection features into their Extreme Ultraviolet Light (EUV) pod inspection machines. The existing AOI software in the EUV pod inspection machines could only identify defective products but could not trace the cause of the defects. The manufacturer wanted to upgrade their machines with AI features to make the products more useful. The AI solution needed to complete the analysis of 380 images for a single pod within two minutes and inspect different materials simultaneously. This required multiple sets of AI models for interpretation. The solution also needed to be installed in a cabinet in the lower half of the machines, which posed a challenge due to the limited space. Smasoft needed to purchase a hardware solution with strong computing performance, stable operation, compact size, and flexible configuration to overcome these challenges.

Case Study
Rapid Hybrid Services Deployment for Global Semiconductor Company
The U.S. manufacturer of engineered materials, optoelectronic components, and semiconductors was focused on growth through mergers and acquisitions (M&As). In 2019–2020, it acquired a global electronics firm and needed immediate connectivity and visibility into the acquired firm’s geo-distributed operations. The company had a highly compressed timeline, with only days to integrate the firm’s DDI operations, while deferring a full network migration to a future date. The company was actively engaged in acquiring and merging strategically aligned companies as a key global growth strategy. The company needed to rapidly integrate its new operations, which included significant remote locations in Asia. The company turned to Infoblox to quickly design a highly secure, available, and reliable solution that could deliver full visibility into new sites. It needed dynamic scalability to accommodate its growing operations and the ability to unify a disparate, geo-diverse infrastructure.
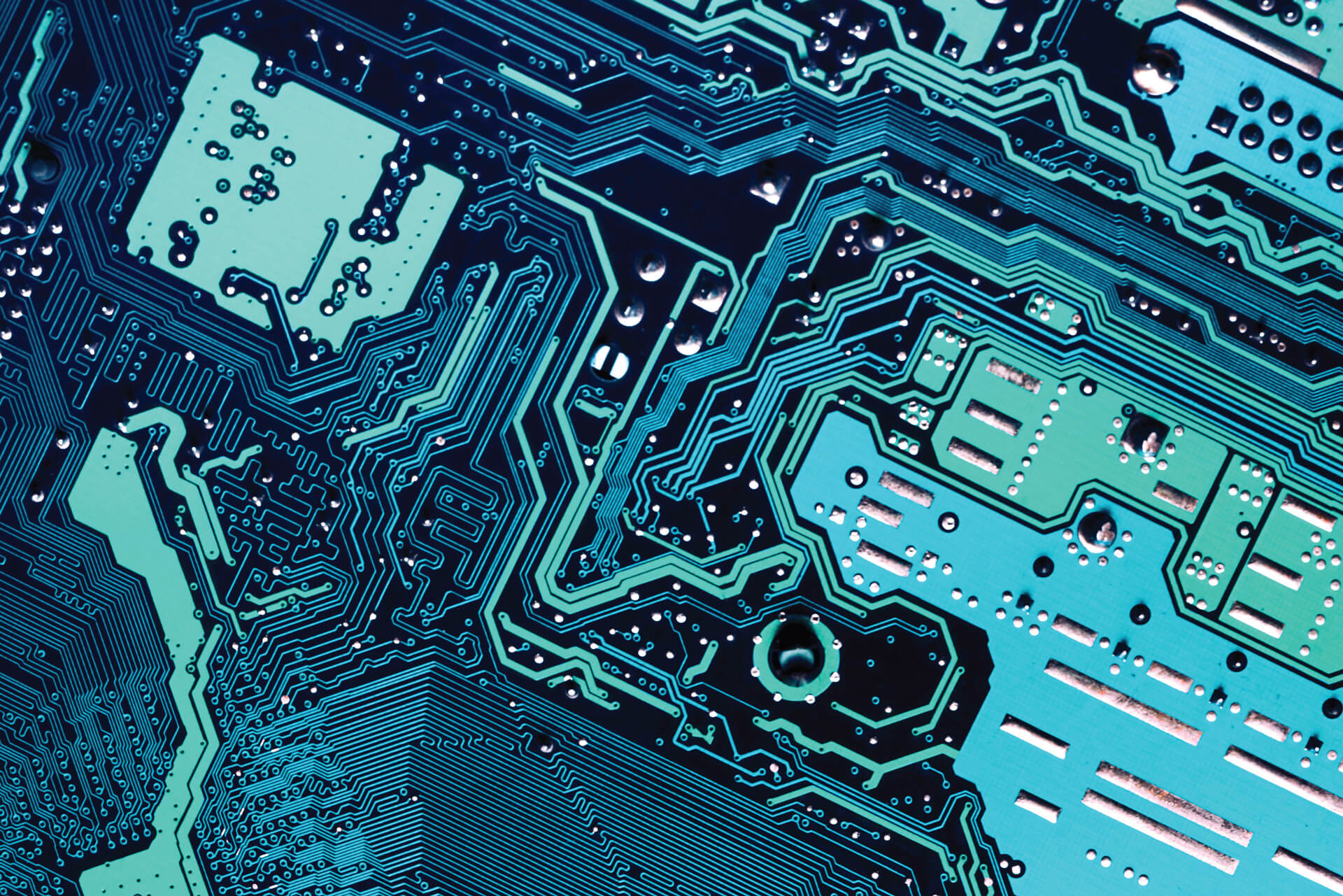
Case Study
Optimizing Semiconductor Manufacturing Yield with IoT
A large U.S.-based manufacturer of high-performance semiconductors was facing a significant challenge in optimizing the manufacturing process of its wireless products. The company, which designs and delivers a broad set of cutting-edge products including radio frequency filters, amplifiers, modulators, attenuators, and more, was experiencing lower than expected overall yield in some of its most complex products. This was affecting the company's productivity and profitability, and there was a need for a solution that could predict low-yield wafers early in the process and identify process improvements to increase overall yield.
Case Study
Leveraging Xenko Game Engine for Immersive VR Experiences: A StarBreach Case Study
Silicon Studio, the developer of the open-source cross-platform game engine Xenko, was looking to showcase the impressive graphical capabilities of their product. They aimed to demonstrate the engine's compatibility with VR and its ability to deliver high-quality virtual reality experiences and games. To achieve this, they needed to create a demo game, StarBreach, that would effectively highlight these features. However, they required an experienced art production team that could create high-quality game art for StarBreach. The challenge was not only to create visually appealing assets but also to demonstrate the technological possibilities of the Xenko game engine.