PSP Limited Brings Buildings to Life with Optimized Mobile Inventory
Customer Company Size
SME
Region
- Pacific
Country
- New Zealand
Product
- NetSuite
- RF-SMART
Tech Stack
- Inventory Management Software
- Warehouse Management System
Implementation Scale
- Enterprise-wide Deployment
Impact Metrics
- Customer Satisfaction
- Productivity Improvements
- Waste Reduction
Technology Category
- Functional Applications - Inventory Management Systems
- Functional Applications - Warehouse Management Systems (WMS)
Applicable Industries
- Construction & Infrastructure
- Buildings
Applicable Functions
- Warehouse & Inventory Management
- Logistics & Transportation
Use Cases
- Inventory Management
- Warehouse Automation
- Supply Chain Visibility
Services
- System Integration
- Training
About The Customer
PSP Limited is a New Zealand-based importer and supplier of a wide range of innovative architectural and building products. The company has been in operation for over 30 years, providing high-quality construction materials such as sheeting, cladding, signage, translucent roofing, and vinyl film to architects, builders, and designers. With a reputation for quality and consistency, PSP Limited operates six warehouses and manages a product range of over 3,000 items. The company is committed to supplying the highest quality materials and ensuring efficient operations to meet the needs of their clients.
The Challenge
PSP Limited, an importer and supplier of architectural and building products in New Zealand, faced significant challenges in managing their inventory across six warehouses and a product range exceeding 3,000 items. The company needed to improve inventory visibility and accuracy to prevent mispicks and incorrect orders, which were common due to the manual processes in place. Additionally, the reliance on paper-based systems led to inefficiencies and errors, further complicating their operations. The need for a more streamlined and automated inventory management system was evident to enhance operational efficiency and accuracy.
The Solution
To address their inventory management challenges, PSP Limited implemented NetSuite and RF-SMART in 2018. This solution was widely accepted by warehouse staff, admin, accounts, sales, and management without any issues. The integration of RF-SMART provided significant improvements in inventory visibility, allowing the company to track stock accurately and prevent mispicks. The system enabled batch recording of items and custom drop-shipping for specific projects, ensuring that stock was not stored with similar items to avoid errors. The implementation of cycle counts with RF-SMART replaced the bi-annual stock counts, improving confidence in inventory levels and enabling quicker error identification and rectification. Additionally, the mobile inventory management system eliminated double-handling of transactions, reducing manual errors and increasing efficiency. The organization of the warehouse space by bin locations optimized picking processes, further enhancing inventory accuracy.
Operational Impact
Quantitative Benefit
Case Study missing?
Start adding your own!
Register with your work email and create a new case study profile for your business.
Related Case Studies.

Case Study
Energy Saving & Power Monitoring System
Recently a university in Taiwan was experiencing dramatic power usage increases due to its growing number of campus buildings and students. Aiming to analyze their power consumption and increase their power efficiency across 52 buildings, the university wanted to build a power management system utilizing web-based hardware and software. With these goals in mind, they contacted Advantech to help them develop their system and provide them with the means to save energy in the years to come.

Case Study
IoT System for Tunnel Construction
The Zenitaka Corporation ('Zenitaka') has two major business areas: its architectural business focuses on structures such as government buildings, office buildings, and commercial facilities, while its civil engineering business is targeted at structures such as tunnels, bridges and dams. Within these areas, there presented two issues that have always persisted in regard to the construction of mountain tunnels. These issues are 'improving safety" and "reducing energy consumption". Mountain tunnels construction requires a massive amount of electricity. This is because there are many kinds of electrical equipment being used day and night, including construction machinery, construction lighting, and ventilating fan. Despite this, the amount of power consumption is generally not tightly managed. In many cases, the exact amount of power consumption is only ascertained when the bill from the power company becomes available. Sometimes, corporations install demand-monitoring equipment to help curb the maximum power demanded. However, even in these cases, the devices only allow the total volume of power consumption to be ascertained, or they may issue warnings to prevent the contracted volume of power from being exceeded. In order to tackle the issue of reducing power consumption, it was first necessary to obtain an accurate breakdown of how much power was being used in each particular area. In other words, we needed to be able to visualize the amount of power being consumed. Safety, was also not being managed very rigorously. Even now, tunnel construction sites often use a 'name label' system for managing entry into the work site. Specifically, red labels with white reverse sides that bear the workers' names on both sides are displayed at the tunnel work site entrance. The workers themselves then flip the name label to the appropriate side when entering or exiting from the work site to indicate whether or not they are working inside the tunnel at any given time. If a worker forgets to flip his or her name label when entering or exiting from the tunnel, management cannot be performed effectively. In order to tackle the challenges mentioned above, Zenitaka decided to build a system that could improve the safety of tunnel construction as well as reduce the amount of power consumed. In other words, this new system would facilitate a clear picture of which workers were working in each location at the mountain tunnel construction site, as well as which processes were being carried out at those respective locations at any given time. The system would maintain the safety of all workers while also carefully controlling the electrical equipment to reduce unnecessary power consumption. Having decided on the concept, our next concern was whether there existed any kind of robust hardware that would not break down at the construction work site, that could move freely in response to changes in the working environment, and that could accurately detect workers and vehicles using radio frequency identification (RFID). Given that this system would involve many components that were new to Zenitaka, we decided to enlist the cooperation of E.I.Sol Co., Ltd. ('E.I.Sol') as our joint development partner, as they had provided us with a highly practical proposal.

Case Study
Intelligent Building Automation System and Energy Saving Solution
One of the most difficult problems facing the world is conserving energy in buildings. However, it is not easy to have a cost-effective solution to reduce energy usage in a building. One solution for saving energy is to implement an intelligent building automation system (BAS) which can be controlled according to its schedule. In Indonesia a large university with a five floor building and 22 classrooms wanted to save the amount of energy being used.

Case Study
Powering Smart Home Automation solutions with IoT for Energy conservation
Many industry leaders that offer Smart Energy Management products & solutions face challenges including:How to build a scalable platform that can automatically scale-up to on-board ‘n’ number of Smart home devicesData security, solution availability, and reliability are the other critical factors to deal withHow to create a robust common IoT platform that handles any kind of smart devicesHow to enable data management capabilities that would help in intelligent decision-making
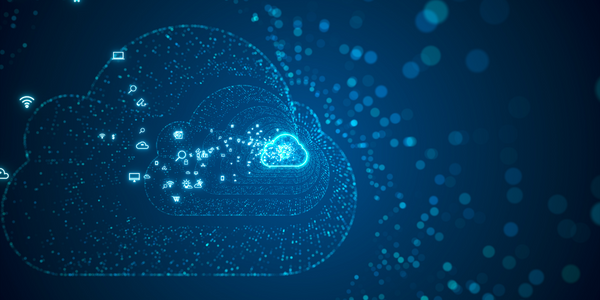
Case Study
Splunk Partnership Ties Together Big Data & IoT Services
Splunk was faced with the need to meet emerging customer demands for interfacing IoT projects to its suite of services. The company required an IoT partner that would be able to easily and quickly integrate with its Splunk Enterprise platform, rather than allocating development resources and time to building out an IoT interface and application platform.