Technology Category
- Analytics & Modeling - Process Analytics
- Functional Applications - Manufacturing Execution Systems (MES)
Applicable Industries
- Paper & Pulp
Applicable Functions
- Quality Assurance
Use Cases
- Process Control & Optimization
- Visual Quality Detection
Services
- Testing & Certification
About The Customer
Euro Caps is a leading coffee manufacturer based in the Netherlands. Since its foundation in 2012, the company has focused on achieving the highest possible quality standards to deliver superior coffee capsules for its customers and millions of coffee-drinkers around the world. Following a period of exceptional growth, the company found that its existing business processes were no longer adequate for the volume of goods it now produced. Today, Euro Caps uses K2 Software across all its business departments, with at least one K2 Five process in every department. The company is continuously working to improve its processes and aims to become a paperless factory.
The Challenge
Euro Caps, a leading coffee manufacturer, was facing challenges in managing its business processes due to rapid growth. The company's existing email and spreadsheet processes were no longer adequate for the volume of goods it was producing and its enlarged workforce. Employees were sharing spreadsheets and documents via email, leading to multiple versions of the same files. Additionally, there were numerous ways of collecting data across the business, and the same data would be entered into different applications by different people. Despite these inefficiencies, the company's processes were vital to upholding its high standards for the quality of their goods. The company also aimed to become a paperless factory, which required implementing more automated, digitized solutions across the company.
The Solution
Euro Caps implemented Microsoft SharePoint with Nintex K2 Five, recommended by local IT partner Thysia Information, to centralize its document management and automate business processes. Over the course of 2 years, Euro Caps built more than 25 K2 Software solutions, simplifying data collection and streamlining processes from the shop floor to the board room. Two key K2 Five solutions, Operator Tiles and Operator Portal, provided employees on the shop floor with instant access to product manuals and the ability to view and record grind history for different types of coffee beans and pallet configurations. In the HR department, K2 Five processes covered everything from hiring new employees to extending contracts and managing the company’s Facebook profile. The company also developed 4 integrated K2 Five processes for approving new suppliers, creating a new commodity item, validating the combination of materials and approving new products. In the Finance Department, traditional paper-based processes like expense claims have been fully digitized and automated using K2 Five.
Operational Impact
Quantitative Benefit
Case Study missing?
Start adding your own!
Register with your work email and create a new case study profile for your business.
Related Case Studies.

Case Study
Wireless Improves Efficiency in Compressed Air Systems
Hollingsworth and Vose wanted to improve the efficiency of their compressed air system, lower the electricity expense component of manufacturing cost in their commodity industry, and conserve energy leading to lowered greenhouse gas emissions. Compressed air systems degrade over time and become leaky and inefficient. Hollingsworth and Vose wanted to increase the frequency of system inspections without paying the high cost of manual labor.
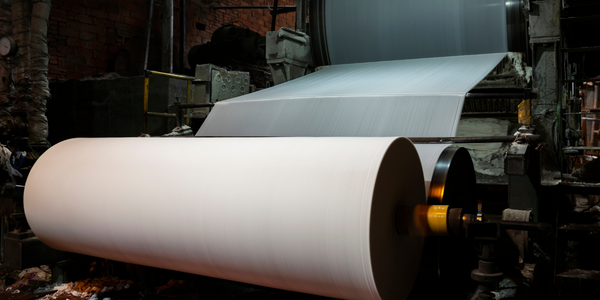
Case Study
Process Predictive Analysis in Pulp and Paper Mill
Common paper breaks consequently lead up to 60 minutes of downtime, delaying a potential $10K per hour of production value process. Thus, defective products cause financial and damage company's reputation. Improving quality and reducing defect rates can generate millions of dollars of revenue per year for your company.
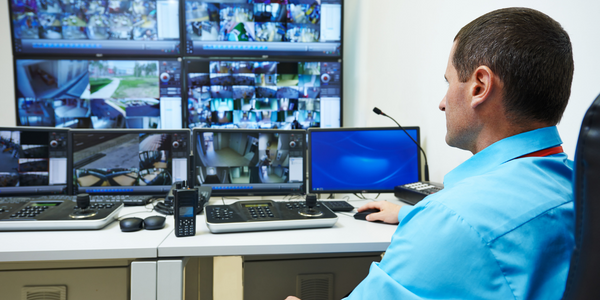
Case Study
Industrial Video Monitoring for Security and Regulatory Compliance
Because of the Stevenson mill’s proximity to the Tennessee River, WestRock was required by the USCG to comply with the Maritime Security 33CFR (MARSEC) regulations. WestRock needed a video security system but wanted to add other applications not required by the government, such as video process monitoring, condition monitoring, and wireless network management. WestRock needed a reliable video solution to avoid the compliance fines and possible security risks – but the solution needed to be implemented in the most cost-effective manner possible.
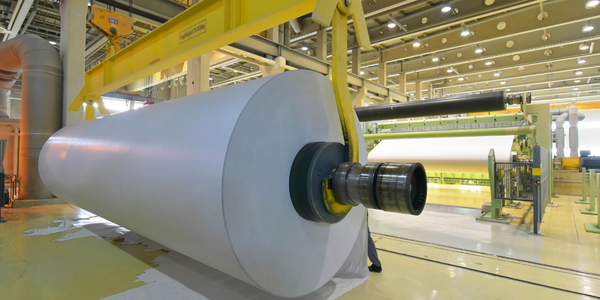
Case Study
ECOsine Active Increased Reliability in the Paper Industry
The paper and pulp industry is interlinking intelligent hi-tech machines to highly efficient production lines. Higher power DC and AC motor drives perform the automation tasks. Every kind of interference that negatively affects the reliability and safety of the installation may lead to production downtime and consequently to significant financial losses. AC and DC motor drives are so-called non-linear loads as they draw a nonsinusoidal current from the grid. Resulting harmonics of current and voltage can interfere with the operation of nearby consumers and overload the electrical infrastructure. In this particular application, the load cycles of the drives often caused interruptions in the production process because of disturbances coupling into the fieldbus system.