Powering innovation with actionable intelligence
Company Size
1,000+
Product
- InfinityQS ProFicient
Tech Stack
- Statistical Process Control (SPC)
- Automated Data Collection
- Unified Data Repository
Implementation Scale
- Departmental Deployment
Impact Metrics
- Customer Satisfaction
- Productivity Improvements
- Waste Reduction
Technology Category
- Analytics & Modeling - Predictive Analytics
- Application Infrastructure & Middleware - Data Exchange & Integration
- Functional Applications - Manufacturing Execution Systems (MES)
Applicable Industries
- Consumer Goods
- Electronics
Applicable Functions
- Process Manufacturing
- Quality Assurance
Use Cases
- Machine Condition Monitoring
- Predictive Maintenance
- Process Control & Optimization
Services
- Software Design & Engineering Services
- System Integration
About The Customer
Umicore Technical Materials is a leading global provider of electrical contact materials that are essential for various everyday applications, such as lighting, electric kettles, space heaters, thermostats, and electric cars. The company is committed to creating future-oriented technologies, products, and services while maintaining the highest possible quality and efficiency to compete in the global market. Umicore's customer base is also focused on innovation, requiring the company to be a partner in their advancements. The company must adhere to strict national and international standards, including ISO 9001 and 14001, EU Directive 2002/95/ED (RoHS), EU regulation REACH, and Conflict of Materials. Umicore's internal culture emphasizes quality, tracking internal and customer complaints to identify trends and opportunities for improvement.
The Challenge
This strong customer-centric focus and drive toward futureproof technologies has produced a culture of quality at Umicore. As Quality Engineer Mark Gaumond explains: • Customers want zero defects and often require capability studies. • Processes must be stable and meet specifications that vary from customer to customer. • Umicore must meet strict national and international standards, including ISO 9001 and 14001; European Union (EU) Directive 2002/95/ED, Restriction of Hazardous Substances (RoHS); EU regulation Registration, Evaluation, Authorization and Restriction of Chemicals (REACH); and Conflict of Materials. For Umicore, quality isn’t only an external issue: It’s internal as well. Mr. Gaumond notes, “We are careful to track internal complaints, customer complaints, and internal issues so that we have a historical record to inform us about trends and opportunities for improvement and prevention.” But quality never stands still. To stay ahead of the needs of future-looking customers, Umicore needed to make quality and process control even more efficient. To do that, the company turned to InfinityQS® ProFicient™.
The Solution
Before adopting InfinityQS ProFicient, Umicore's line operators manually collected data in spreadsheets and converted it for use in a third-party data-analysis tool, which was error-prone and time-intensive. To improve quality and process control, Umicore automated data collection and centralized data storage for analysis. Working with InfinityQS, Umicore implemented ProFicient on its stamping lines, where quality is essential, and specific Statistical Process Control (SPC) requirements apply. The tolerances for the height of contact materials are extremely precise, and many process variables are in play. ProFicient ensures the critical accuracy of the stamping lines by automating data collection through the plant's existing dial indicators and micrometers. Operators simply push a button on the gauge, eliminating manual errors and streamlining data collection. The collected data is automatically stored in ProFicient's Unified Data Repository, making it easy for both operators and managers to access various charts and reports. This improved visibility into manufacturing processes helps ensure that any process changes are data-driven.
Operational Impact
Case Study missing?
Start adding your own!
Register with your work email and create a new case study profile for your business.
Related Case Studies.
.png)
Case Study
Improving Vending Machine Profitability with the Internet of Things (IoT)
The vending industry is undergoing a sea change, taking advantage of new technologies to go beyond just delivering snacks to creating a new retail location. Intelligent vending machines can be found in many public locations as well as company facilities, selling different types of goods and services, including even computer accessories, gold bars, tickets, and office supplies. With increasing sophistication, they may also provide time- and location-based data pertaining to sales, inventory, and customer preferences. But at the end of the day, vending machine operators know greater profitability is driven by higher sales and lower operating costs.

Case Study
Remote Temperature Monitoring of Perishable Goods Saves Money
RMONI was facing temperature monitoring challenges in a cold chain business. A cold chain must be established and maintained to ensure goods have been properly refrigerated during every step of the process, making temperature monitoring a critical business function. Manual registration practice can be very costly, labor intensive and prone to mistakes.
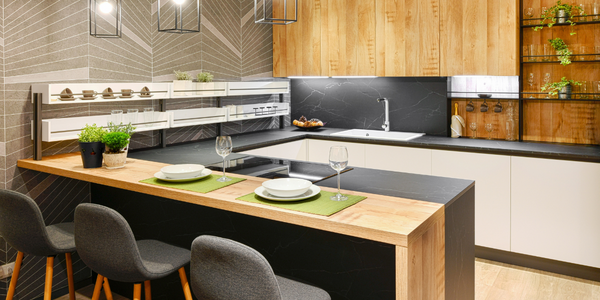
Case Study
Series Production with Lot-size-1 Flexibility
Nobilia manufactures customized fitted kitchens with a lot size of 1. They require maximum transparency of tracking design data and individual processing steps so that they can locate a particular piece of kitchen furniture in the sequence of processes.