Powering Growth and Productivity
Customer Company Size
Large Corporate
Region
- America
Country
- United States
Product
- Raymond Model 8400 pallet trucks
- Raymond Model 4200 stand-up counterbalanced lift trucks
- Raymond Model 7400 Reach-Fork® trucks
- Raymond Model 9600 Swing-Reach® truck
Tech Stack
- Electric lift trucks
- Battery charging schedules
Implementation Scale
- Enterprise-wide Deployment
Impact Metrics
- Cost Savings
- Productivity Improvements
- Customer Satisfaction
Technology Category
- Functional Applications - Fleet Management Systems (FMS)
- Functional Applications - Warehouse Management Systems (WMS)
Applicable Industries
- Automotive
- Transportation
Applicable Functions
- Warehouse & Inventory Management
- Logistics & Transportation
Use Cases
- Fleet Management
- Energy Management System
- Warehouse Automation
Services
- System Integration
About The Customer
AP Exhaust Products is a manufacturer that has been supplying auto service professionals with a complete line of automotive, light truck, SUV, and heavy-duty exhaust and emissions products for more than 80 years. The company’s headquarters in Goldsboro, N.C., ships up to 31,000 parts per day in a single-shift operation. To move parts efficiently on the plant floor and within the distribution center, AP Exhaust Products relies on a fleet of Raymond® lift trucks, which are serviced through a maintenance package with Carolina Handling, an authorized Sales and Service Center of The Raymond Corporation.
The Challenge
In 2010, AP Exhaust Products was experiencing significant growth and wanted to ensure its material handling equipment was positioned to aid the company during current and future expansion. The company decided to evaluate its lift truck fleet to ensure it was as efficient and cost-effective as possible. They previously purchased refurbished equipment, but the cost of maintenance became too high. They decided to analyze their current costs and determine the return on investment for purchasing new equipment.
The Solution
With help from Carolina Handling, AP Exhaust Products updated its existing fleet of LP and electric lift trucks to a fleet of new electric vehicles. The newly optimized fleet includes Raymond Model 8400 pallet trucks, Raymond Model 4200 stand-up counterbalanced lift trucks, Raymond Model 7400 Reach-Fork® trucks, and the Raymond Model 9600 Swing-Reach® truck. These trucks assist AP Exhaust in reducing the number of trips for delivering and receiving products within its facility, and increased lift and acceleration capabilities. Carolina Handling also implemented a comprehensive maintenance management program to handle preventive and unscheduled maintenance needs for a fixed monthly cost. Through this program, AP Exhaust Products reduced maintenance costs between 35 and 45 percent. Additionally, Carolina Handling helped AP Exhaust Products customize and implement a complete power program for its lift truck battery charging, in which AP Exhaust Products pays a monthly fee for its battery power, and a third party handles battery charging schedules.
Operational Impact
Quantitative Benefit
Case Study missing?
Start adding your own!
Register with your work email and create a new case study profile for your business.
Related Case Studies.
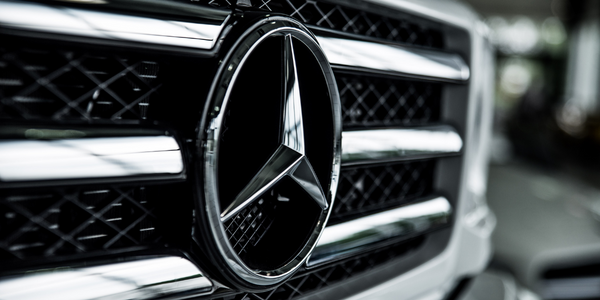
Case Study
Integral Plant Maintenance
Mercedes-Benz and his partner GAZ chose Siemens to be its maintenance partner at a new engine plant in Yaroslavl, Russia. The new plant offers a capacity to manufacture diesel engines for the Russian market, for locally produced Sprinter Classic. In addition to engines for the local market, the Yaroslavl plant will also produce spare parts. Mercedes-Benz Russia and his partner needed a service partner in order to ensure the operation of these lines in a maintenance partnership arrangement. The challenges included coordinating the entire maintenance management operation, in particular inspections, corrective and predictive maintenance activities, and the optimizing spare parts management. Siemens developed a customized maintenance solution that includes all electronic and mechanical maintenance activities (Integral Plant Maintenance).
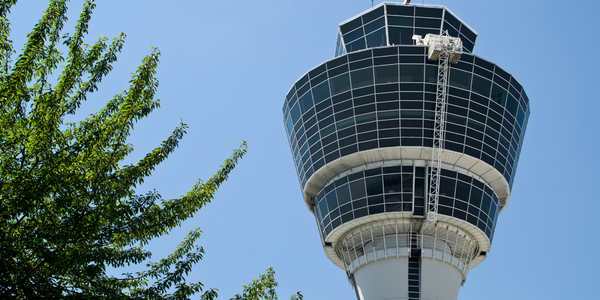
Case Study
Airport SCADA Systems Improve Service Levels
Modern airports are one of the busiest environments on Earth and rely on process automation equipment to ensure service operators achieve their KPIs. Increasingly airport SCADA systems are being used to control all aspects of the operation and associated facilities. This is because unplanned system downtime can cost dearly, both in terms of reduced revenues and the associated loss of customer satisfaction due to inevitable travel inconvenience and disruption.
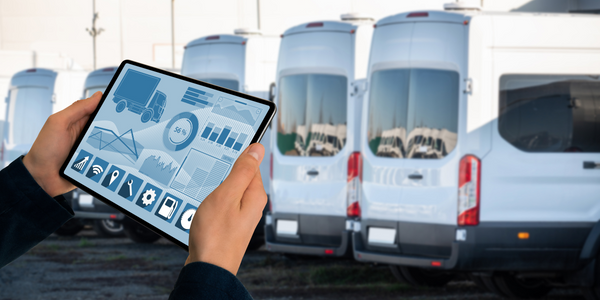
Case Study
IoT-based Fleet Intelligence Innovation
Speed to market is precious for DRVR, a rapidly growing start-up company. With a business model dependent on reliable mobile data, managers were spending their lives trying to negotiate data roaming deals with mobile network operators in different countries. And, even then, service quality was a constant concern.
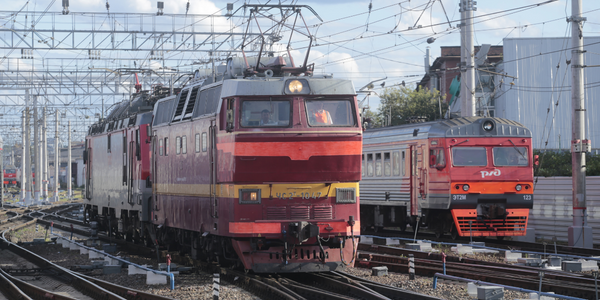
Case Study
Digitize Railway with Deutsche Bahn
To reduce maintenance costs and delay-causing failures for Deutsche Bahn. They need manual measurements by a position measurement system based on custom-made MEMS sensor clusters, which allow autonomous and continuous monitoring with wireless data transmission and long battery. They were looking for data pre-processing solution in the sensor and machine learning algorithms in the cloud so as to detect critical wear.