Polmetasa integrates information and refines control of actions with SoftExpert solution
Customer Company Size
Large Corporate
Region
- Europe
Country
- Spain
Product
- SoftExpert PPM Suite
- SE Document
Tech Stack
- Business Intelligence (BI)
Implementation Scale
- Enterprise-wide Deployment
Impact Metrics
- Productivity Improvements
- Customer Satisfaction
- Digital Expertise
Technology Category
- Functional Applications - Enterprise Resource Planning Systems (ERP)
Applicable Industries
- Automotive
Applicable Functions
- Quality Assurance
- Business Operation
Use Cases
- Predictive Maintenance
- Process Control & Optimization
- Remote Asset Management
Services
- System Integration
- Software Design & Engineering Services
About The Customer
PMG Polmetasa is a member of the PMG group, with a global presence in Europe, NAFTA countries, and China. It employs directly approximately 2100 persons, of which roughly 250 are in the Polmetasa plant. PMG Polmetasa is a manufacturer of components and systems for the automotive industry. The company's portfolio focuses on powder metal parts used in automotive shock absorber applications, among which the key examples are pistons and banded pistons, base valves/cylinder ends, and rod guides with or without the inserted bushing.
The Challenge
An ISO 14001, ISO/TS 16949 and BS OHSAS 18001 certified company, Polmetasa needed to reduce the time spent on collecting information and on monitoring actions. It was also necessary to conduct a real-time analysis of indicators, since this was only carried out after the data collection and treatment. Finally, information such as indicators and parts history, for example, was not centralized, taking up considerable time for the employees in charge.
The Solution
A SoftExpert customer since 2010, Polmetasa adopted the SoftExpert component for nonconformity management, corrective and preventive actions, and for the exploration of results through BI (Business Intelligence SoftExpert PPM). The company has currently increased the number of SE components with the acquisition of the incorporating the modules of projects, portfolios, and documents. SE PPM assists in the prioritization, planning, management, and execution of projects, portfolios, and programs. As it is an integrated suite, it allows organizations to easily manage their services, projects, products, and resources. To Polmetasa, the solution mainly meets the demand of managers and executives for having a real-time vision of the indicators, resources, and the initiatives of the organization, training the decision-makers to prioritize their investment according to critical criteria, such as benefits, time, cost, and risks in order to ensure a better alignment with the organization’s business strategies and governance policies. The document management component being implemented, SE Document, will supplement the entire management of the generated documentation.
Operational Impact
Quantitative Benefit
Case Study missing?
Start adding your own!
Register with your work email and create a new case study profile for your business.
Related Case Studies.
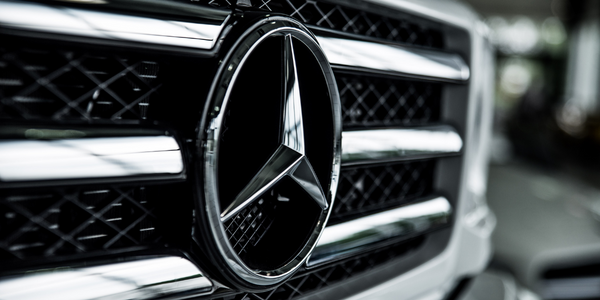
Case Study
Integral Plant Maintenance
Mercedes-Benz and his partner GAZ chose Siemens to be its maintenance partner at a new engine plant in Yaroslavl, Russia. The new plant offers a capacity to manufacture diesel engines for the Russian market, for locally produced Sprinter Classic. In addition to engines for the local market, the Yaroslavl plant will also produce spare parts. Mercedes-Benz Russia and his partner needed a service partner in order to ensure the operation of these lines in a maintenance partnership arrangement. The challenges included coordinating the entire maintenance management operation, in particular inspections, corrective and predictive maintenance activities, and the optimizing spare parts management. Siemens developed a customized maintenance solution that includes all electronic and mechanical maintenance activities (Integral Plant Maintenance).
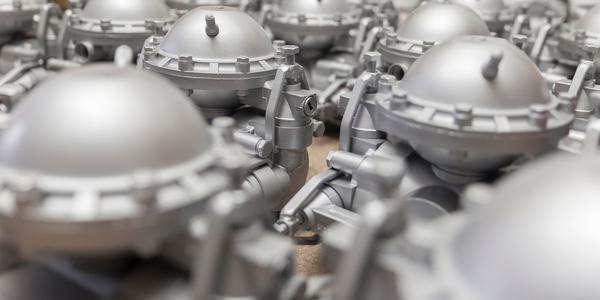
Case Study
Monitoring of Pressure Pumps in Automotive Industry
A large German/American producer of auto parts uses high-pressure pumps to deburr machined parts as a part of its production and quality check process. They decided to monitor these pumps to make sure they work properly and that they can see any indications leading to a potential failure before it affects their process.