Politecnico of Torino Student Team Uses HyperWorks to Reduce Vehicle Weight and Fuel Consumption in Shell Eco Marathon
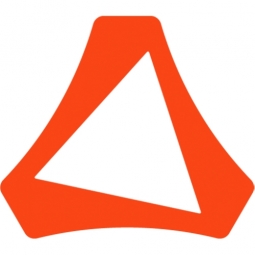
Technology Category
- Robots - Autonomous Guided Vehicles (AGV)
- Sensors - Autonomous Driving Sensors
Applicable Industries
- Aerospace
- Automotive
Applicable Functions
- Logistics & Transportation
- Product Research & Development
Use Cases
- Smart Parking
- Vehicle Performance Monitoring
About The Customer
The H2politO team is a group of students from the Politecnico di Torino. The students’ backgrounds and profiles are very diverse, with students coming from various engineering disciplines. Each of them contributes his or her special expertise and together they compose the team that is responsible for the car’s design and construction. The engineering disciplines involved in the project range from automotive and mechanical to electronics, aerospace, energy, mathematics, computer science, mechatronics, management, cinema & media and industrial design. The team is based in the Mechanical and Aerospace Engineering Department (DIMEAS) of Turin’s Politecnico, and led by Prof. Massimiliana Carello. The team’s mission is to shape a new generation of engineers: leaders in their fields, who represent the educational excellence in regard to each of their competencies.
The Challenge
The H2politO team, a group of students from the Politecnico di Torino, participated in the Shell Eco-marathon (SEM), a competition that challenges student teams to design, build, and drive the most energy-efficient car. The team competed in the “Prototype” category with a hydrogen fuel cell vehicle, and in the “Urban Concept” category with a hybrid vehicle. The main challenge for the team was to reduce frictions and masses to minimize fuel consumption. One of the most critical issues was the wheel rim design. Lighter rims lead to less rotating masses, reducing energy consumption and improving the dynamic behavior of the vehicle. The geometry of this specific component had to be optimized: the ideal structure and mass distribution had to be determined, while also taking manufacturing constraints into account. For these development tasks, the H2politO team had to apply sophisticated computer-aided engineering (CAE) tools which would support a simulation driven design process and enable early decision making by proposing possible design directions for further improvements of the vehicles.
The Solution
The H2politO team applied Altair’s HyperWorks suite to design and optimize the rims. The tools enabled them to consider any technical constraints such as tire design specifications and constraints that might apply to the chosen manufacturing technology for the rims, which were in this case turning and milling. The material the team wanted to use was an aluminum alloy. To optimize the rim structure, the students used OptiStruct, Altair’s FE solver and optimization tool, which is included in HyperWorks. The first step was the definition of the component’s design space, which in this use case was the full rim cylinder (divided in different zones) including a zone for hub linkage and the tire profile. Then occurring loads and other boundary conditions were applied. The following optimization study simulated the real test for the rims, applying the forces to the most critical zone near the hub. The resulting mass distribution provided the basis for a detailed CAD model of the rim. In a last step, the team used static analyses to validate the results.
Operational Impact
Quantitative Benefit
Case Study missing?
Start adding your own!
Register with your work email and create a new case study profile for your business.
Related Case Studies.
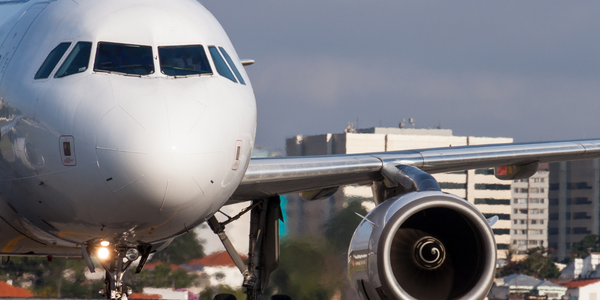
Case Study
Airbus Soars with Wearable Technology
Building an Airbus aircraft involves complex manufacturing processes consisting of thousands of moving parts. Speed and accuracy are critical to business and competitive advantage. Improvements in both would have high impact on Airbus’ bottom line. Airbus wanted to help operators reduce the complexity of assembling cabin seats and decrease the time required to complete this task.
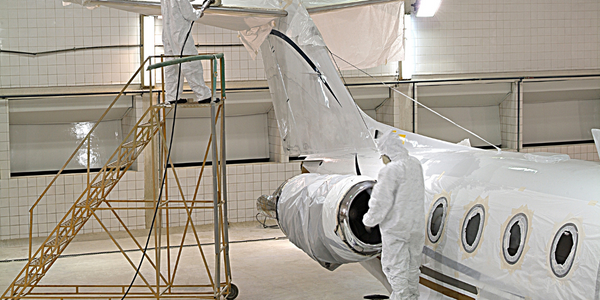
Case Study
Aircraft Predictive Maintenance and Workflow Optimization
First, aircraft manufacturer have trouble monitoring the health of aircraft systems with health prognostics and deliver predictive maintenance insights. Second, aircraft manufacturer wants a solution that can provide an in-context advisory and align job assignments to match technician experience and expertise.
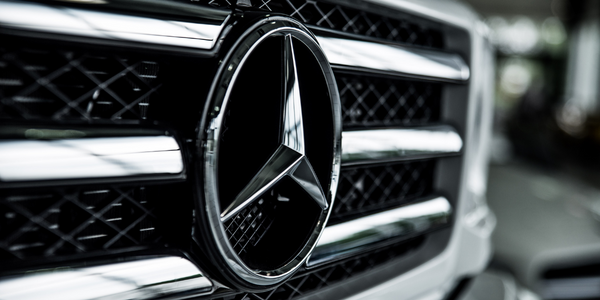
Case Study
Integral Plant Maintenance
Mercedes-Benz and his partner GAZ chose Siemens to be its maintenance partner at a new engine plant in Yaroslavl, Russia. The new plant offers a capacity to manufacture diesel engines for the Russian market, for locally produced Sprinter Classic. In addition to engines for the local market, the Yaroslavl plant will also produce spare parts. Mercedes-Benz Russia and his partner needed a service partner in order to ensure the operation of these lines in a maintenance partnership arrangement. The challenges included coordinating the entire maintenance management operation, in particular inspections, corrective and predictive maintenance activities, and the optimizing spare parts management. Siemens developed a customized maintenance solution that includes all electronic and mechanical maintenance activities (Integral Plant Maintenance).
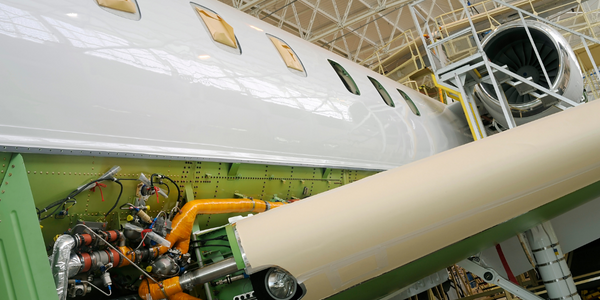
Case Study
Aerospace & Defense Case Study Airbus
For the development of its new wide-body aircraft, Airbus needed to ensure quality and consistency across all internal and external stakeholders. Airbus had many challenges including a very aggressive development schedule and the need to ramp up production quickly to satisfy their delivery commitments. The lack of communication extended design time and introduced errors that drove up costs.