PLZ Aeroscience Improves Production Control, Increases Sales
Customer Company Size
Large Corporate
Region
- America
Country
- United States
Product
- GainSeeker Suite
Tech Stack
- Digital Gaging Equipment
- Computerized Quality Tracking System
Implementation Scale
- Enterprise-wide Deployment
Impact Metrics
- Cost Savings
- Productivity Improvements
- Customer Satisfaction
- Revenue Growth
Technology Category
- Analytics & Modeling - Real Time Analytics
- Functional Applications - Enterprise Resource Planning Systems (ERP)
- Functional Applications - Remote Monitoring & Control Systems
Applicable Industries
- Consumer Goods
- Chemicals
Applicable Functions
- Quality Assurance
- Business Operation
Use Cases
- Machine Condition Monitoring
- Predictive Maintenance
- Process Control & Optimization
- Real-Time Location System (RTLS)
Services
- System Integration
- Software Design & Engineering Services
About The Customer
PLZ Aeroscience is North America’s largest custom aerosol manufacturer and packager, producing private brand products, custom formulations, and providing contract filling for other customers. With over 100 years in business, PLZ has experienced significant growth in the last six years, driven by acquisitions and expansion of privately owned brands. The company operates multiple plants, each with its own legacy processes and systems, necessitating a consolidation of information systems to manage growth effectively. PLZ's reputation for quality is paramount, and they have focused on improving their quality data systems to maintain and enhance this reputation.
The Challenge
PLZ Aeroscience faced significant challenges due to their legacy paper-based data management systems. As the company grew through acquisitions and expansion, they needed to consolidate these legacy systems to improve operating efficiencies. The existing quality systems were inefficient, with inspectors manually recording data on paper, leading to difficulties in understanding product performance and comparing different machines or tooling. The information was often stuck on the factory floor, hidden from view, and the quality team spent considerable time managing rework when processes ranged out of specification. Rising staffing costs, customer complaints, poor efficiencies, and high inventory carrying costs further impacted profitability. The company was caught between high corporate expectations and the current reality of operating performance, necessitating a change.
The Solution
PLZ decided to replace their manual, paper-based quality tracking processes with a state-of-the-art computerized system. They selected Hertzler Systems’s GainSeeker Suite after a thorough competitive search, confident in its flexibility to handle the volume and diversity of products. The implementation began on two lines at their Pacific and St. Clair, Missouri facilities, with immediate payback. Hertzler worked with PLZ to custom-configure the GainSeeker Suite to match specific processes, setting up a system to collect data on production lines and in the quality lab. Measurements were automatically collected from digital gaging equipment or manually posted using a computer keyboard. Data is now logged automatically into a single database, visible in real-time, allowing operators to see their data plotted on charts and react to trends before they become problems.
Operational Impact
Quantitative Benefit
Case Study missing?
Start adding your own!
Register with your work email and create a new case study profile for your business.
Related Case Studies.
.png)
Case Study
Improving Vending Machine Profitability with the Internet of Things (IoT)
The vending industry is undergoing a sea change, taking advantage of new technologies to go beyond just delivering snacks to creating a new retail location. Intelligent vending machines can be found in many public locations as well as company facilities, selling different types of goods and services, including even computer accessories, gold bars, tickets, and office supplies. With increasing sophistication, they may also provide time- and location-based data pertaining to sales, inventory, and customer preferences. But at the end of the day, vending machine operators know greater profitability is driven by higher sales and lower operating costs.
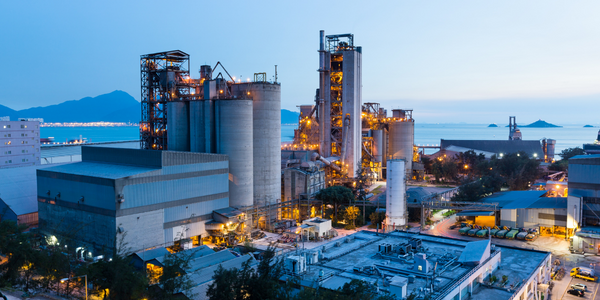
Case Study
Honeywell - Tata Chemicals Improves Data Accessibility with OneWireless
Tata was facing data accessibility challenges in the cement plant control room tapping signals from remote process control areas and other distant locations, including the gas scrubber. Tata needed a wireless solution to extend its control network securely to remote locations that would also provide seamless communication with existing control applications.

Case Study
Advanced Elastomer Systems Upgrades Production
In order to maintain its share of the international market for thermoplastic elastomers AES recently expanded its Florida plant by adding a new production line. While the existing lines were operating satisfactorily using a PROVOX distributed control system with traditional analog I/O, AES wanted advanced technology on the new line for greater economy, efficiency, and reliability. AES officials were anxious to get this line into production to meet incoming orders, but two hurricanes slowed construction.
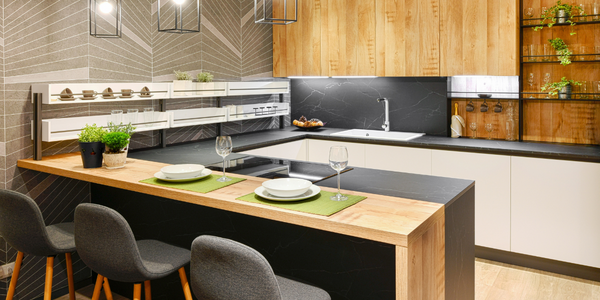
Case Study
Series Production with Lot-size-1 Flexibility
Nobilia manufactures customized fitted kitchens with a lot size of 1. They require maximum transparency of tracking design data and individual processing steps so that they can locate a particular piece of kitchen furniture in the sequence of processes.